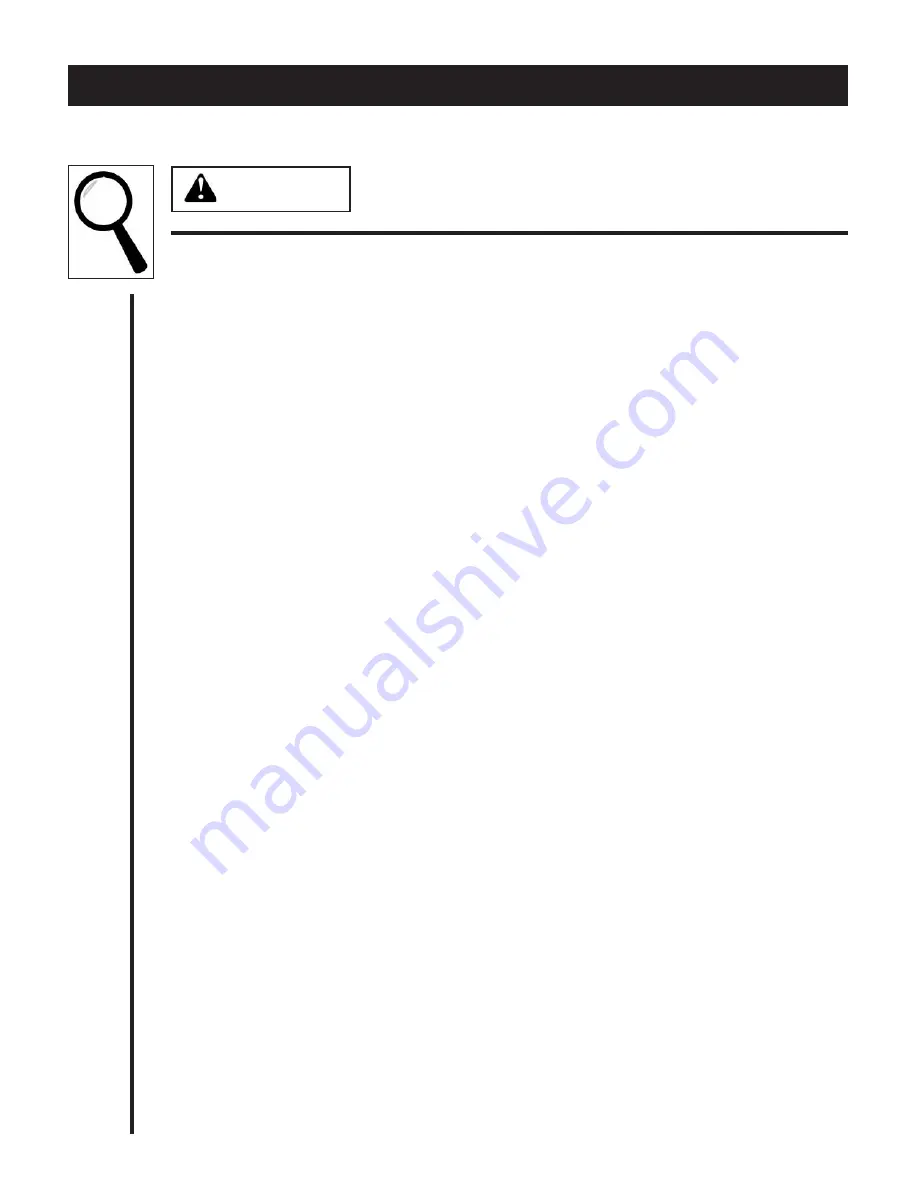
11
1. Fan Does Not Operate
A.)
Check voltage requirements on unit and electrical supply. Check for live receptacle, plug,
power line and unit's power On/Off switch.
B.)
Look for any loose connections inside the main motor's junction box.
2. Unusual Noise
A.)
Squealing at start-up or during operation may be caused by the motor shaft's bearing
seal. Spray with lubricant at the front of the motor where the shaft exits the motor's
frame.
3. No Fog
A.)
If the Flow Control Valve is closed, turn the knob in-line with the valve to open fogging
output. Visually check Feed Line conections leading to the atomizing blade assembly.
B.)
If the unit is automated with a controller, check to see if power is being supplied to the
unit when the controller is on.
C.)
If after checking both the Flow Valve and Controller, if you still do not have any fog,
begin a process of elimination starting with the Feed Pump located in the sump tank.
Disconnect and reconnect your plumbing before and after each device to check for any
obstructions or electrical failures.
4. Poor Quality Fog
A.)
The feed tube (Part #532) may not be pointing properly into the reservoir behind the
blade assembly. The feed tube should be aimed slightly downward, into the slot area
between the motor shaft and the stainless steel plate, rear of the blade assembly.
B.)
Reservoir or blade passageways may be clogged. Fluid entering a clogged reservoir will
sling out of the reservoir instead of entering the passageways of the fan blades. To
clean, remove the blade assembly from the motor shaft and remove the stainless steel
plate. Clean the reservoir area. Attempt to blow and listen for air through each blade. If
clear, assemble and reinstall. If the blades cannot be unclogged, replace with a new
blade assembly (Part #531).
5. Fog Slowly Decreases
If fog output gradually decreases over time, check for kinks in the water supply lines.
Check to make sure the float valve assembly is maintaining a full tank (fully submerging the
pump at all times). If the problem persists, sediment may be slowly building around the inlet
screen of the pump located in the sump tank. Try cleaning this area by removing the tank's
drainage plug (Part #481) to flush out the dirty water.
T
ROUBLESHOOTING
BEFORE INSPECTION AND/OR SERVICE
DISCONNECT AND LOCK OUT POWER SOURCE.
WARNING
www.JigglyGreenhouse.com | (800) 878-7829 | [email protected]