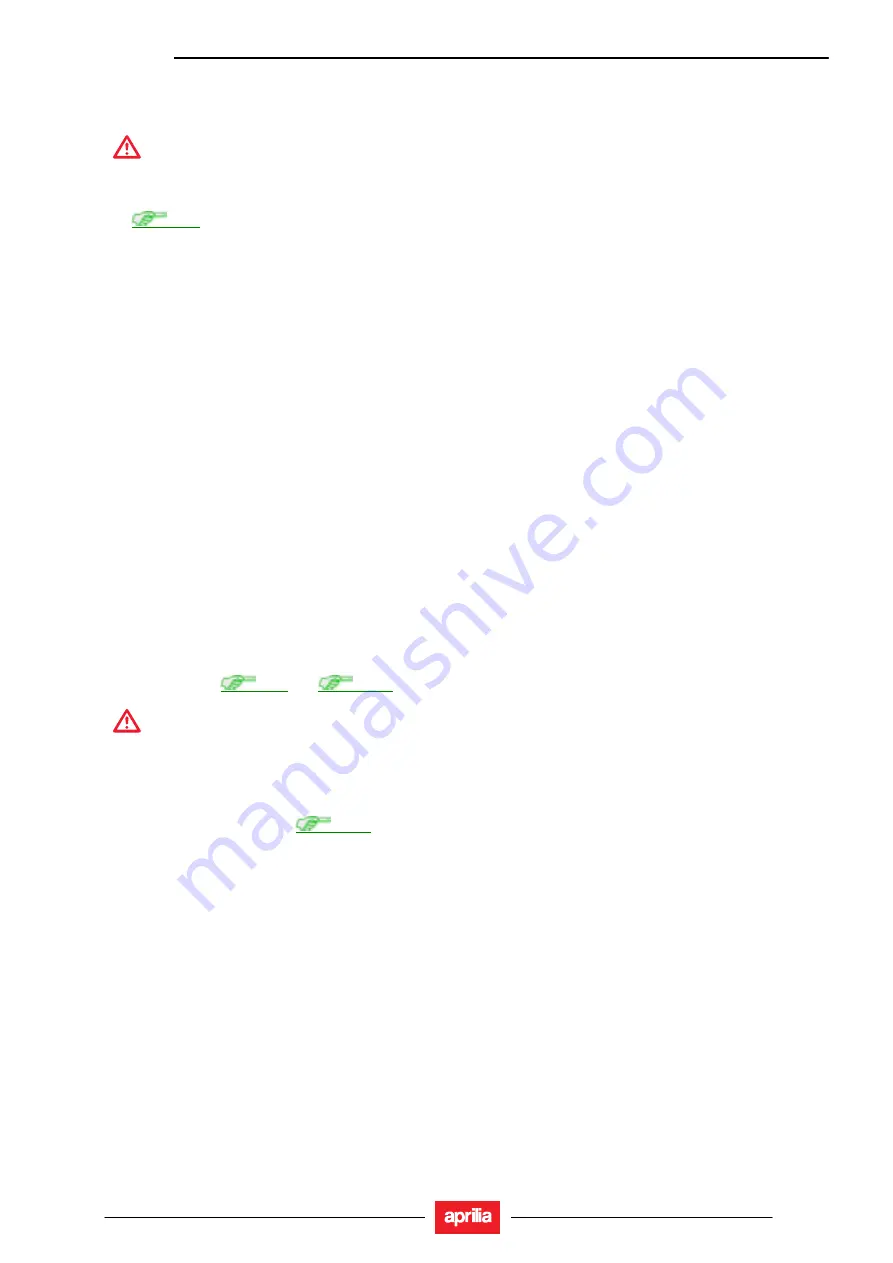
CHASSIS
7 - 73
RS 125
7.6.5.
INSPECTING THE REAR WHEEL
COMPONENTS
WARNING
Check the condition of all components. Pay
particular attention to those listed below.
BEARINGS, SEALS, WHEEL SPINDLE and WHEEL RIM;
see
7.5.4
.
CUSH-DRIVE RUBBER
•
Inspect the cush-drive rubber for damage or wear.
Replace as required.
•
Fit the cush-drive rubber into the wheel hub.
•
Position the complete final drive assembly to the
wheel. Rotate the rear chain sprocket manually in both
directions and check cush-drive play in the hub. If you
feel too much play, change the cush drive.
REAR CHAIN SPROCKET
•
Check the toothing of the front and rear chain
sprockets for wear. In the event excess wear is found,
replace front and rear chain sprockets and drive chain
as a set; see
7.6.4
and
7.13.1
WARNING
Drive chain and front and rear chain sprockets
must always be replaced as a set. Failure to do
so will lead to early wear of the newly fitted
component(s).
TYRE
•
Check tyre condition; see
2.19.1
Summary of Contents for RS 125
Page 7: ...GENERAL INFORMATION RS 125 GENERAL INFORMATION 1 1 1 ...
Page 30: ...GENERAL INFORMATION RS 125 1 24 ...
Page 31: ...ROUTINE MAINTENANCE RS 125 ROUTINE MAINTENANCE 2 2 1 ...
Page 88: ...ROUTINE MAINTENANCE RS 125 2 58 ...
Page 89: ...LUBRICATION RS 125 LUBRICATION 3 3 1 ...
Page 92: ...LUBRICATION RS 125 THIS PAGE HAS BEEN INTENTIONALLY LEFT BLANK 3 4 ...
Page 93: ...FUEL SYSTEM RS 125 FUEL SYSTEM 4 4 1 ...
Page 103: ...COOLING SYSTEM RS 125 COOLING SYSTEM 5 5 1 ...
Page 111: ...ENGINE RS 125 ENGINE 6 6 1 ...
Page 118: ...ENGINE RS 125 Generator 5 Pick up 6 ECU ground 7 Neutral light switch 8 6 8 ...
Page 123: ...ENGINE RS 125 ECU ground 6 Pick up 7 Generator 8 Starter motor 9 6 13 ...
Page 127: ...ENGINE RS 125 6 3 2 SPECIAL TOOLS Exhaust valve extractor ROTAX part no 277 445 6 17 ...
Page 133: ...CHASSIS 7 1 RS 125 CHASSIS 7 ...
Page 238: ...CHASSIS 7 106 RS 125 Pull the shock absorber in a downward motion to remove ...
Page 245: ...ELECTRICAL SYSTEM 8 1 RS 125 ELECTRICAL SYSTEM 8 ...
Page 274: ...ELECTRICAL SYSTEM 8 30 RS 125 8 16 WIRING DIAGRAM 8 16 1 WIRING DIAGRAM ...
Page 276: ...ELECTRICAL SYSTEM 8 32 RS 125 THIS PAGE HAS BEEN INTENTIONALLY LEFT BLANK ...
Page 277: ...TROUBLESHOOTING INFORMATION RS 125 TROUBLESHOOTING INFORMATION 9 9 1 ...
Page 285: ...TROUBLESHOOTING INFORMATION RS 125 FUEL SYSTEM HOSES OIL TUBES B F E G H I 9 9 ...
Page 286: ...TROUBLESHOOTING INFORMATION RS 125 CLUTCH CABLE M L COLD START CABLE N I 9 10 ...
Page 287: ...TROUBLESHOOTING INFORMATION RS 125 THROTTLE CABLE A O H I 9 11 ...
Page 288: ...TROUBLESHOOTING INFORMATION RS 125 COOLING SYSTEM P Q 9 12 ...
Page 289: ...TROUBLESHOOTING INFORMATION RS 125 R T S 9 13 ...
Page 290: ...TROUBLESHOOTING INFORMATION RS 125 THIS PAGE HAS BEEN INTENTIONALLY LEFT BLANK 9 14 ...