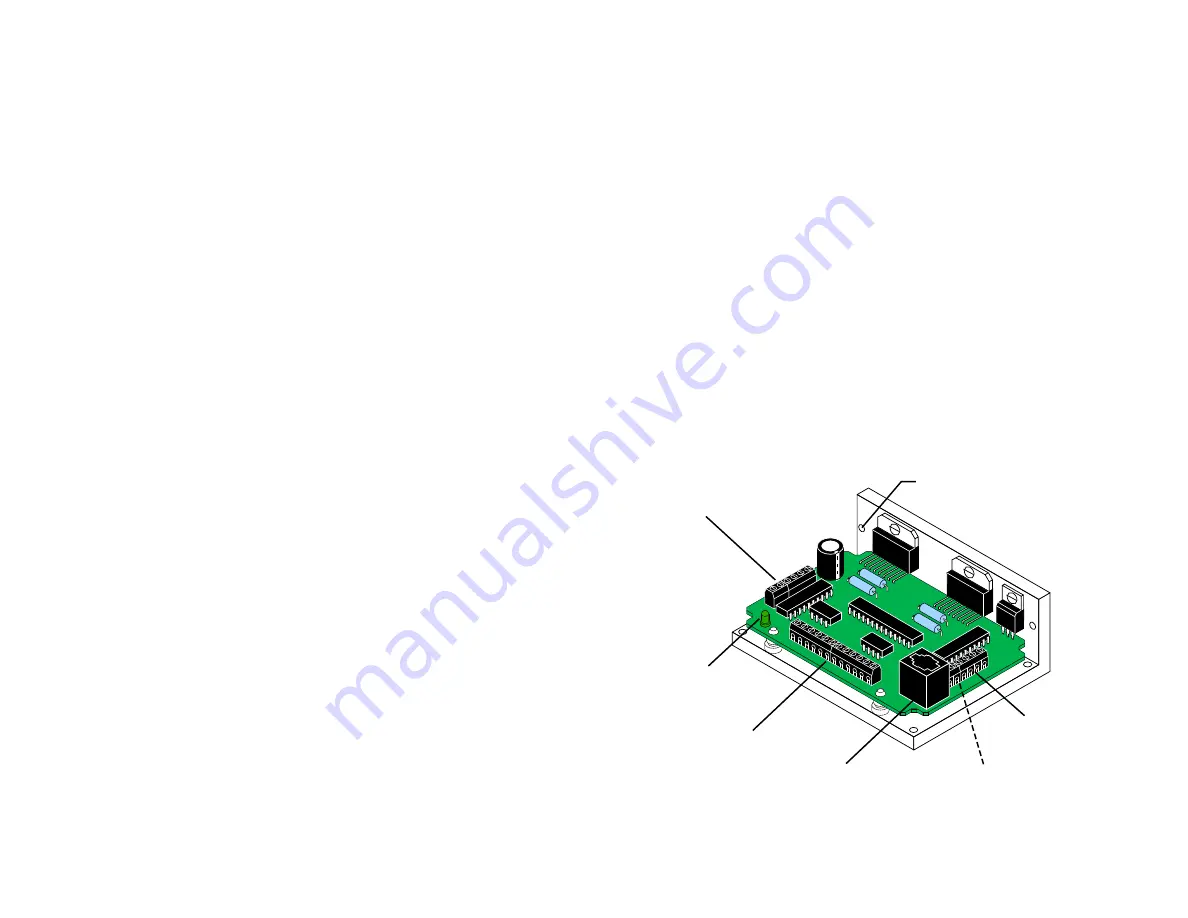
-5-
Getting Started
To use your Applied Motion Products motor control, you will need the following:
• a 12-35 volt DC power supply for the motor. Please read the section entitled
Choosing a Power Supply for help in choosing the right power supply.
• a compatible step motor.
• a small flat blade screwdriver for tightening the connectors (included with drive).
• a personal computer running Microsoft Windows 95, 98, NT, Me, 2000 or XP.
• Applied Motion's eXposition™ software (supplied with drive on CD)
• Applied Motion Si™ programming cable.
If you plan to use the drive in Pulse & Direction Mode:
• a source of step pulses. Signal may be sinking (NPN), sourcing (PNP) or
differential.
• if your application calls for bidirectional rotation, you'll also need a direction
signal. This signal may also be sourcing, sinking or differential.
For Oscillator Mode:
• A run/stop signal or switch and a direction signal or switch. Signals may be
sinking (NPN), sourcing (PNP) or differential.
• Analog speed signal or speed control potentiometer (optional)
connector
• DC power supply
• motor 1
mounting hole (1 of 6)
pc
connector
for programming
power
LED
connector
• output
• motor 2
connector
• step/run1, dir1
• step/run2, dir2
• analog in1
• analog in2
Always use the blue & white Applied
Motion screwdriver to tighten the
screw terminal connectors. Larger
screwdrivers may remove the plastic
dimples that prevent the screws from
falling out.
-12-
Microstepping
Many step motor drives offer a choice between full step and half step resolutions.
In most full step drives, both motor phases are used all the time. Half stepping
divides each step into two smaller steps by alternating between both phases on and
one phase on. Microstepping drives like the 2035XD precisely control the amount
of current in each phase at each step position as a means of electronically subdivid-
ing the steps even further. The 2035XD offers a choice of full step, half step and 13
microstep resolutions. The highest setting divides each full step into 254
microsteps, providing 50,800 steps per revolution when using a 1.8° motor.
In addition to providing precise positioning and smooth motion, microstep drives
can be used to provide motion in convenient units. When the drive is set to 2000
steps/rev (1/10 step) and used with a 5 pitch lead screw, you get .0001 inches/step.
The step resolution is selected using the eXpositon™ software on your PC.
Restrictions
Restrictions
Restrictions
Restrictions
Restrictions:
If an axis is in run/stop mode, the resolution of that axis is automatically 12,800
steps/rev.
If one axis is set for full step (200 steps/rev) or half step (400 steps/rev) then the
other axis must be also set for 200 or 400 steps/rev.
Direction signal must be set at least 10 microseconds before activating the run
signal, or the move may take place in the wrong direction.
SHOP ONLINE at www.airlinehyd.com
800-999-7378