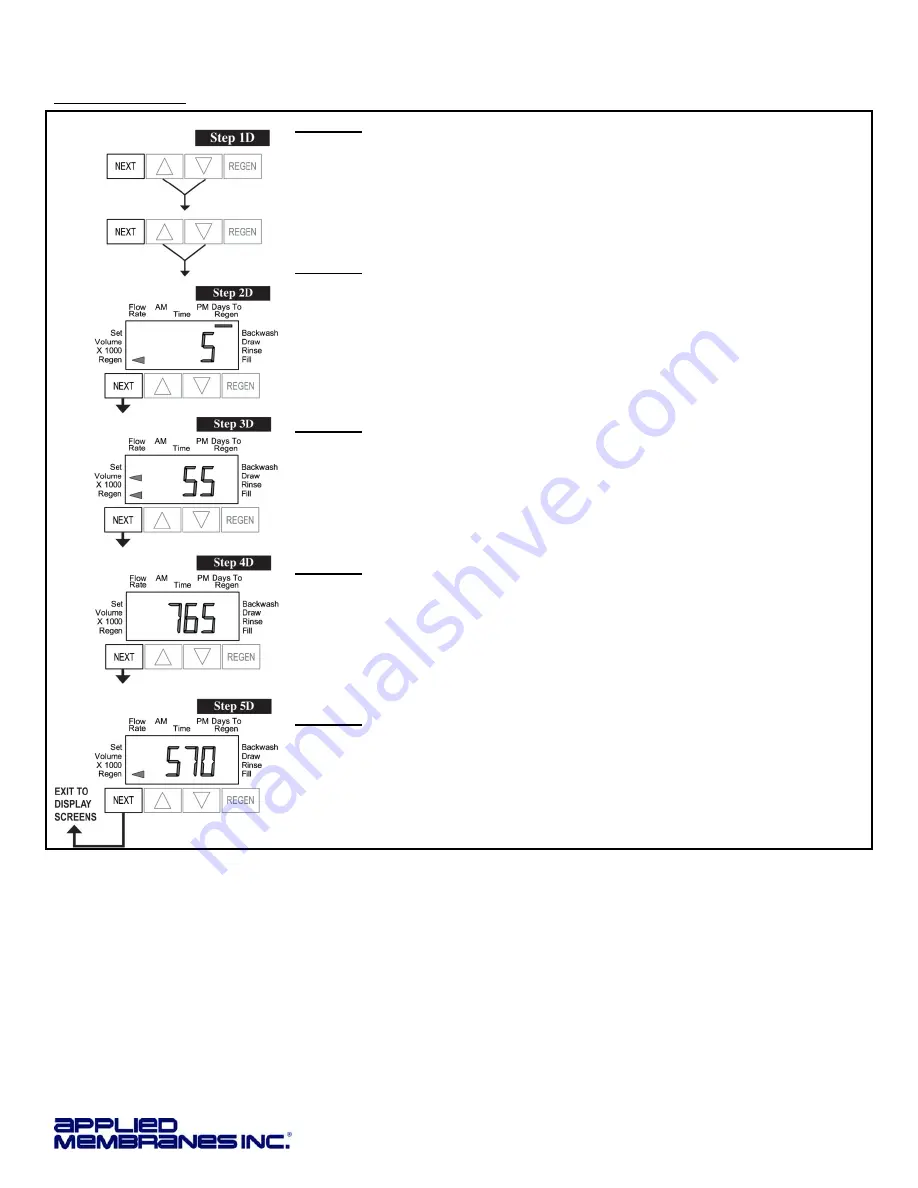
Installation and Service Manual – Carbon Filter
Page 17
Copyright © 2012 Applied Membranes, Inc. All Rights Reserved.
Diagnostics
Step 1D
Press
▲
and
▼
simultaneously for 5 seconds and release.
Then press
▲
and
▼
simultaneously for 3 seconds and release.
If screen in Step 2D does not appear, the lock on the valve is activated. To unlock
press
▼
, NEXT, REGEN,
▲
in sequence, then press
▲
and
▼
simultaneously for 5
seconds and release.
Step 2D
Display shows the number of days since a regeneration last occurred.
Press NEXT to go to next step. Press REGEN to exit Diagnostics.
Step 3D
Display shows the volume of water treated in gallons since the last regeneration.
Display will show zero since there is no meter installed.
Press NEXT to go to next step. Press REGEN to return to previous step.
Step 4D
Display shows the days in service since start up.
Press NEXT to go to next step. Press REGEN to return to previous step.
Step 5D
Display shows the total number of regeneration cycles since start up.
Press NEXT to exit Diagnostics. Press REGEN to return to previous step.