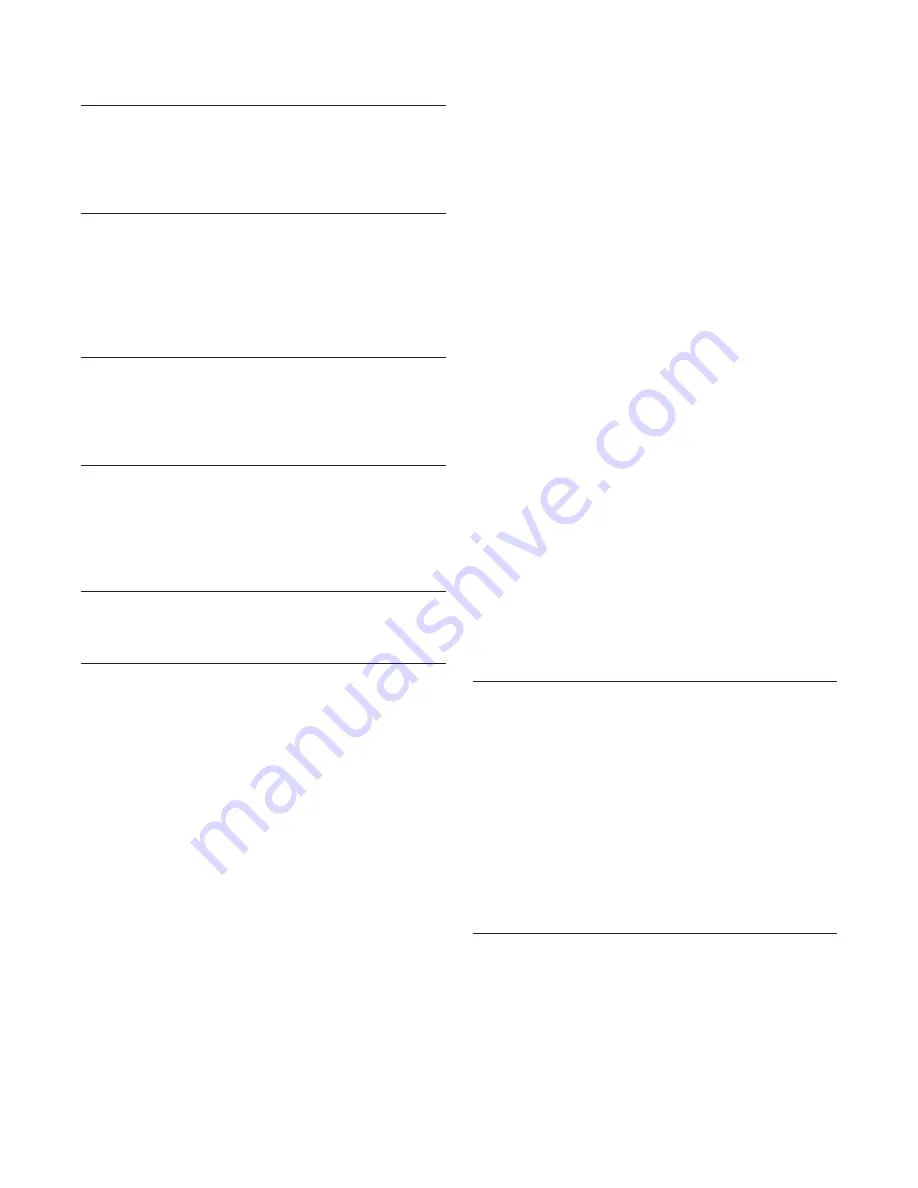
– 35 –
B. Lubrication Instructions
Item
Manufacturer
Bearing
Type
All 3 phase
US., Baldor
Single row ball
fan
motors
or
equal bearings
(1 HP to
100 HP)
ODP, TEFC
Recommendation: See following note.
All 1 phase
Century, G.E.,
Bronze sleeve
motors
or
equal bearings
(Fractional
HP) ODP,
TEFC or
TEAO
Recommendation: See following note.
Fractional HP Century, G.E.
Bronze sleeve
single phase,
or equal
bearings
ODP or
TEFC
Recommendation: See following note.
Fan shaft
Fafnir
Self-aligning
bearings
or equal
single row or
double
row
ball
bearings,
resilient
mounted
Recommendation: See following note.
Dampers
Factory
Sleeve
or
equal
Recommendation: See following note.
1. Blower Motors – Some motors require lubrication
while others do not. Those that require lubrication can
be identifi ed by the presence of grease plugs in the
motor casing at each end. Motors that do not have
grease plugs cannot be greased and are lubricated for
the life of the motor bearing.
Lubrication of motors should be done while the mo-
tor is warm and at a standstill. Remove and clean all
grease plugs and insert a grease fi tting in the upper
hole in the motor casing at each end. (Viewed as if
motor were sitting horizontally on its base). There may
be one or two plugs in each end casing of the motor.
Add a small amount of a clean, good grade ball bear-
ing grease, such as Exxon Polyrex EM or equal, with a
low pressure grease gun. Run the motor fi ve minutes
before removing the grease fi ttings and replacing the
plugs.
CAUTION: An excess of grease will overheat the
bearings.
NOTE: On totally enclosed fan cooled (TEFC)
motors, the rear end fan housing must be removed
to expose the grease plugs.
2. Pillow Block Bearings – Pillow block bearings are used
on supply blower(s). Bearings have been pre-lubricated
with high-quality lithium-complex base grease with
an EP additive. The grease is a lithium-complex base
mineral oil, NLGI Grade 2 consistency, with a base oil
viscosity of ISO VG220. Re-lubrication should be done
with lithium-complex thickened grease with a compa-
rable NLGI consistency and base oil type and viscosity.
Wipe all grease fi ttings clean before adding grease.
Grease should be added slowly, in small amounts at
frequent intervals while the shaft is being manually
rotated.
A slight showing of grease at the seals with accom-
panying normal bearing temperature indicates proper
lubrication. Normal temperature can range from “cool”
to “hot to the touch” depending on size, speed and
surrounding conditions. Excessive bearing temperature
indicates faulty lubrication. An insuffi cient amount of
grease is suggested by a bearing showing no grease
at the seals, and a higher than normal temperature
and noise level. Excessive leakage of grease at the
seals, and a high operating temperature suggest too
much grease.
Frequency of Lubrication – Frequency of lubrica-
tion depends upon operating conditions. The bearing
operating temperature is the best index for determin-
ing a relubrication schedule. The following chart gives
the frequency of relubrication based upon continuous
operation for various operating temperatures and can
be used as a satisfactory guide for determining when
all ball and roller bearings should be relubricated.
Speed
Temperature Cleanliness Interval
100 RPM
Up to 125°F Clean
4 to 10
months
500 RPM
Up to 150°F Clean
1 to 4
months
1000 RPM Up to 210°F Clean
2 weeks
1500 RPM Over 150°F
Clean
weekly
Any Speed Up to 150°F Dirty
1 week
to 1 month
Any Speed Over 150°F
Dirty
daily to
1
week
Any Speed Any Temp.
Very Dirty
daily to
1
week
Any Speed Any Temp.
Extreme
daily to
Conditions
1
week
Roller Bearings
100 RPM Up to 125°F Clean
1 – 4
months
500 RPM Up to 150°F Clean
1 week to
1
month