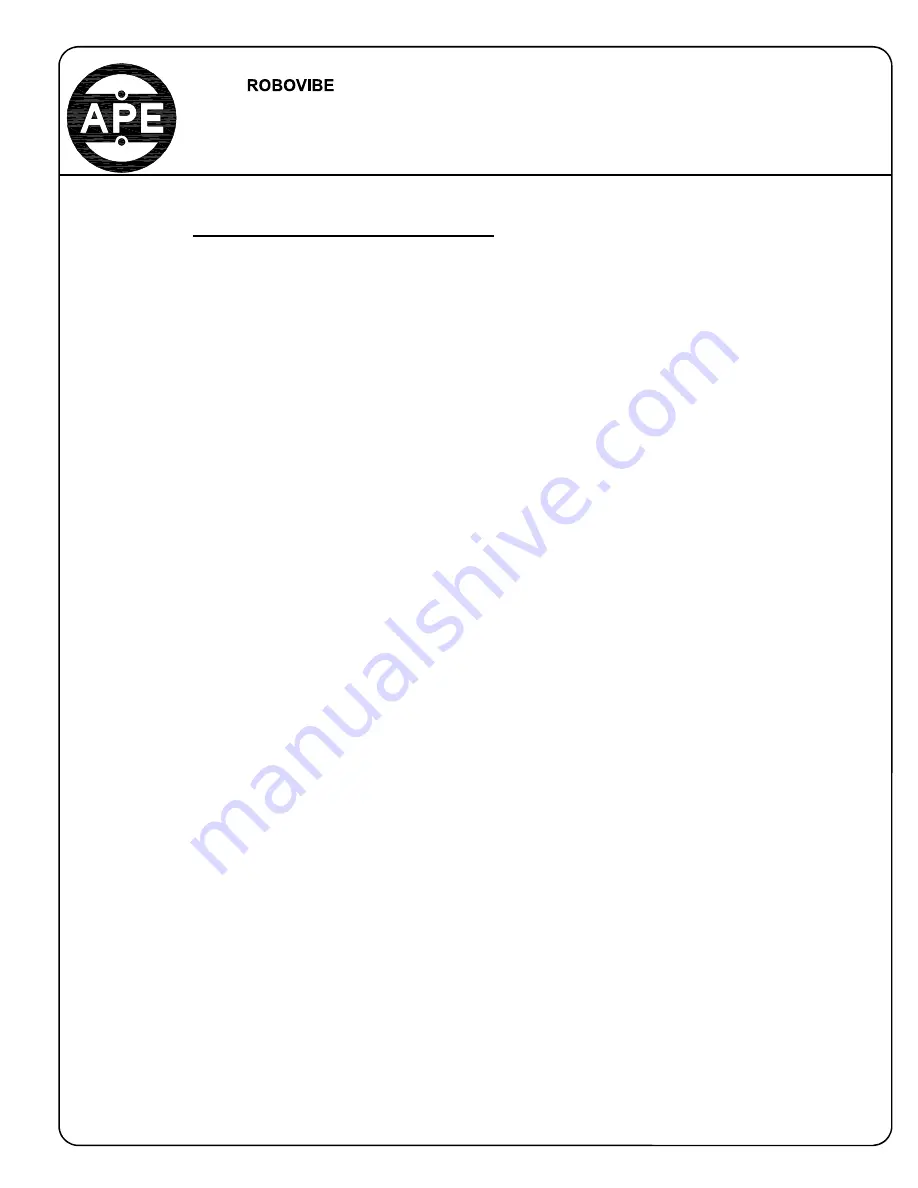
VIBRATORY
DRIVER/EXTRACTOR
II.
PREPARATION FOR OPERATION
C. RIGGING OF VIBRATOR (CONTINUED)
3. GAGE HOSE: It is recommended that a 0-3000 PSI pressure gage be installed,
within convenient view of the excavator operator, for situations when the
operator desires to close the ROBOVIBE clamp, without starting the
vibrator.(See manifold assembly drawing for fitting location).
a. Measure the length of ¼” ID hydraulic hose that will be required to connect
the gage fitting, on the ROBOVIBE manifold, to the desired gage
location. Include enough extra hose length to allow the full range of
motion of the excavator stick and boom. Gage hose pressure rating to
be 3000 PSI minimum.
b. Order and install the hoses measured above. Be sure that the hose working
pressures match or exceed the maximum pressure for your specific
ROBOVIBE application. See the first page of this manual for pressure
settings that are specific to your ROBOVIBE.
c. After the hoses are installed, slowly move the ROBOVIBE, and the
excavator, through full range of motion to be sure that hoses do not bind or
pull tight.
d. Fasten the non-flexing portions of the hoses to convenient structures on the
boom and stick. Re-check range of motion.
e. To bleed the air from the hoses, loosen the two 0.38” ID hoses at the
ROBOVIBE clamp cylinder (approx. one turn). With the excavator running
at low RPM, move the AUX control joy stick
slightly
into the clamp close
posi-tion. Wait until oil flows from the connection at the hydraulic clamp
(clamp close). When oil flows without air, tighten the connection. Now
move the bucket control joy stick
slightly
into the clamp open position.
Wait until oil flows from the connection at the hydraulic clamp (clamp
open). When oil flows without air, tighten the connection.
4. CHANGING EXCAVATORS
a. NEVER SWITCH THE ROBOVIBE TO AN EXCAVATOR OF A
DIFFERENT MAKE OR MODEL WITHOUT CONTACTING APE/J&M.
Moving a ROBOVIBE to a different excavator than it was designed for
can cause serious vibrator damage, or inferior performance. To move
a ROBOVIBE to a different excavator, the following items must be
analyzed by APE/J&M personnel to insure a correct match to the new
excavator;
i.
Yoke width
ii. Yoke pin diameter
iii. Hydraulic motor size
iv. Manifold pressure settings
v. Excavator horsepower
vi. Excavator hydraulic system
b. For the convenience of the owner, a ROBOVIBE application form has
been included as page VIII-20 of this manual. If it is contemplated to
move the ROBOVIBE to a different excavator, complete this form and
mail, e-mail, or fax, this form to your local APE office.
II-5
Summary of Contents for ROBOVIBE
Page 2: ...VIBRATORY DRIVER EXTRACTOR...
Page 5: ...VIBRATORY DRIVER EXTRACTOR...
Page 8: ...VIBRATORY DRIVER EXTRACTOR...
Page 12: ...VIBRATORY DRIVER EXTRACTOR...
Page 28: ...VIBRATORY DRIVER EXTRACTOR...
Page 29: ...VIBRATORY DRIVER EXTRACTOR VI HYDRAULIC CIRCUITRY SCHEMATIC VI 1...
Page 35: ...VIBRATORY DRIVER EXTRACTOR VIII 3...
Page 36: ...VIBRATORY DRIVER EXTRACTOR VIBRATOR 175065 VII 4...
Page 39: ...VIBRATORY DRIVER EXTRACTOR ROTOTILT MULTI ATTACHMENT 150661 VIII 7...
Page 40: ...VIBRATORY DRIVER EXTRACTOR ROTOTILT SUB ASM ROTOR 173043 VIII 8...
Page 41: ...VIBRATORY DRIVER EXTRACTOR ROTOTILT SUB ASM ROTOR 150662 VIII 9...
Page 52: ...VIBRATORY DRIVER EXTRACTOR J BOX VIII 20...
Page 53: ...VIBRATORY DRIVER EXTRACTOR RELAY PANEL VIII 21...
Page 54: ...VIBRATORY DRIVER EXTRACTOR ELECTRICAL SCHEMATIC VIII 22...
Page 55: ...VIBRATORY DRIVER EXTRACTOR ELECTRICAL SCHEMATIC CONT VIII 23...
Page 56: ...VIBRATORY DRIVER EXTRACTOR HYDRAULIC MANIFOLD 173049 VIII 24...
Page 58: ...VIBRATORY DRIVER EXTRACTOR MANIFOLD HYDRAULIC CIRCUIT VIII 26...
Page 60: ...VIBRATORY DRIVER EXTRACTOR...