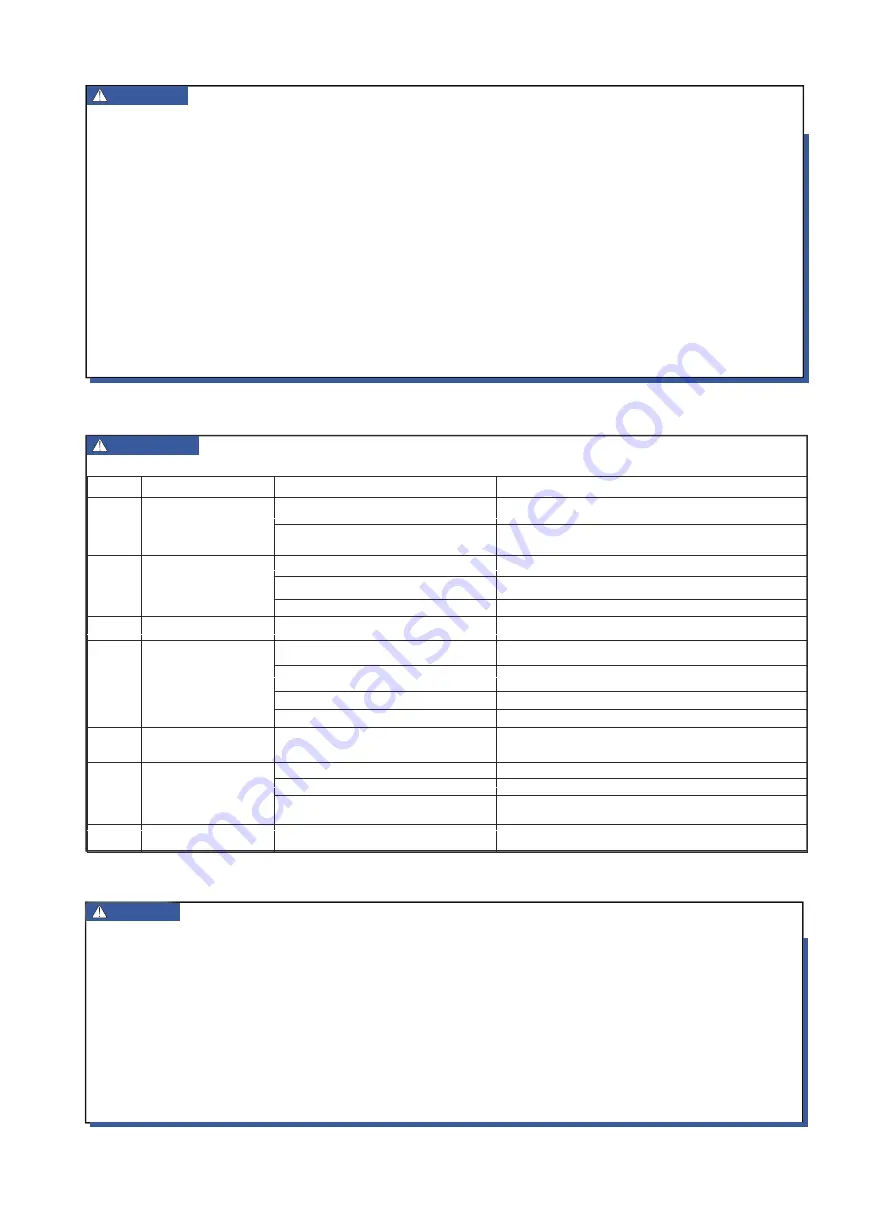
Safety warning
Maintenance
1.
Read the operating instruction carefully before installing and using the device.
2.
The whole equipment must be reliably grounded with a grounding resistance of less than 1 ohms during use; Otherwise, it is easy to
cause abnormal or even damage of ion bar.
3.
Do not use the device when the humidity is higher than 70%.
4.
Do not use the device in inflammable and explosive environment.
5.
It is strictly forbidden to disassemble products without authorization. Internal maintenance and repair must be carried out by
professional personnel.
6. The product is strictly prohibited to touch liquid during use
, otherwise there will be abnormal, resulting in electric shock or fire.
7.
Power must be turned off during inspecting or replacing the product, otherwise it may cause electric shock or fire.
8.
The product is specially designed for removing static electricity and is strictly prohibited for other purposes. Any abnormal use may
cause machine failure, electric shock, fire and other hidden dangers.
9.
It is strictly forbidden to touch the electrode needles when power is on, otherwise it is easy to cause fault and electric shock accident.
10.
Discharge needle is a sharp metal object, please use it with care.
11.
Please check the specifications of the power supply before powering on the product. Any power supply that does not meet the
specifications may cause damage or even failure to the product.
12.
Check the power cord regularly. If it is damaged, replace it immediately; otherwise, leakage and abnormal operation may occur.
NO.
1
The indicator on the
panel is off
Confirm the power supply specification
(
INPUT
:
100—240VAC
50/60Hz
;
OUTPUT
:
24VDC 2000mA
)
2
Whether the discharge seat is tightened
Confirm the discharge seat is tightened
3
4
Panel indicator red light on
Confirm the installation location and stay away from
surrounding conductors
Return to factory for maintenance
Return to factory for maintenance
5
Panel indicator blue light
flashes
Poor grounding of the strip grounding electrodes
on both sides of the electrode needle at the
bottom of the ion bar
Return to factory for maintenance
6
Return to factory for maintenance
Return to factory for maintenance
Main-board chip is damaged caused by poor
grounding or no grounding
7
High voltage module is damaged or insulation
of the discharge seat is damaged
Return to factory for maintenance
7URXEOHVKRRWLQJ
Problems
Reasons
Solutions
The electrostatic removal
performance decreased
obviously
The electrostatic removal
performance decreased
Unable to discharge
The product is smoky or burnt
Poor contact of the power cable
Power supply mismatch
Discharge needle is polluted and damaged
Bearing set
of ion bar is improper
There are conductors or other
ion bar
around
Electromagnetic interference
Abnormal discharge
No power supply for high voltage module
High voltage module is damaged
High voltage module is damaged
Main-board chip is damaged
Check whether the power cable is in good condition and
securely connected
Clean or replace the discharge needle
Confirm the best bearing
set
Remove (moving) conductors or other
ion bar
Turn off the power switch / unplug the power cable, restart
the ion
bar
Check the grounding of the
ion bar
and plant equipment, and return
to the factory for maintenance
1.
The ion bar should be cleaned and maintained in time according to the use environment and the required electrostatic protection
requirements in order to ensure the good performance of the product. That is, gently remove the carbon deposits on the discharge
electrode, discharge socket, and metal discharge body with electrostatic brush, dust-free cotton swab, dust-free cloth dipped in
anhydrous alcohol, which will improve its performance significantly. Note:
A.
Operation must be done 10 minutes after power cut of
f.
B.
It must be cleaned when dust or white
stuff
appear on the tip of the needle during use. Use dust-free cloth dipped in anhydrous
alcohol to clean when brush can not meet the cleaning requirements.
C.
The ion bar must be powered on after alcohol is completely volatilized after cleaning. No other organic solvent can be used to clean
the ion bar.
2.
If the switch working indicator light of the power plug-in port on the panel of the ion bar is off , it should be stopped and repaired by
professional maintenance personnel. It can be used only after the electrical performance index is normal.