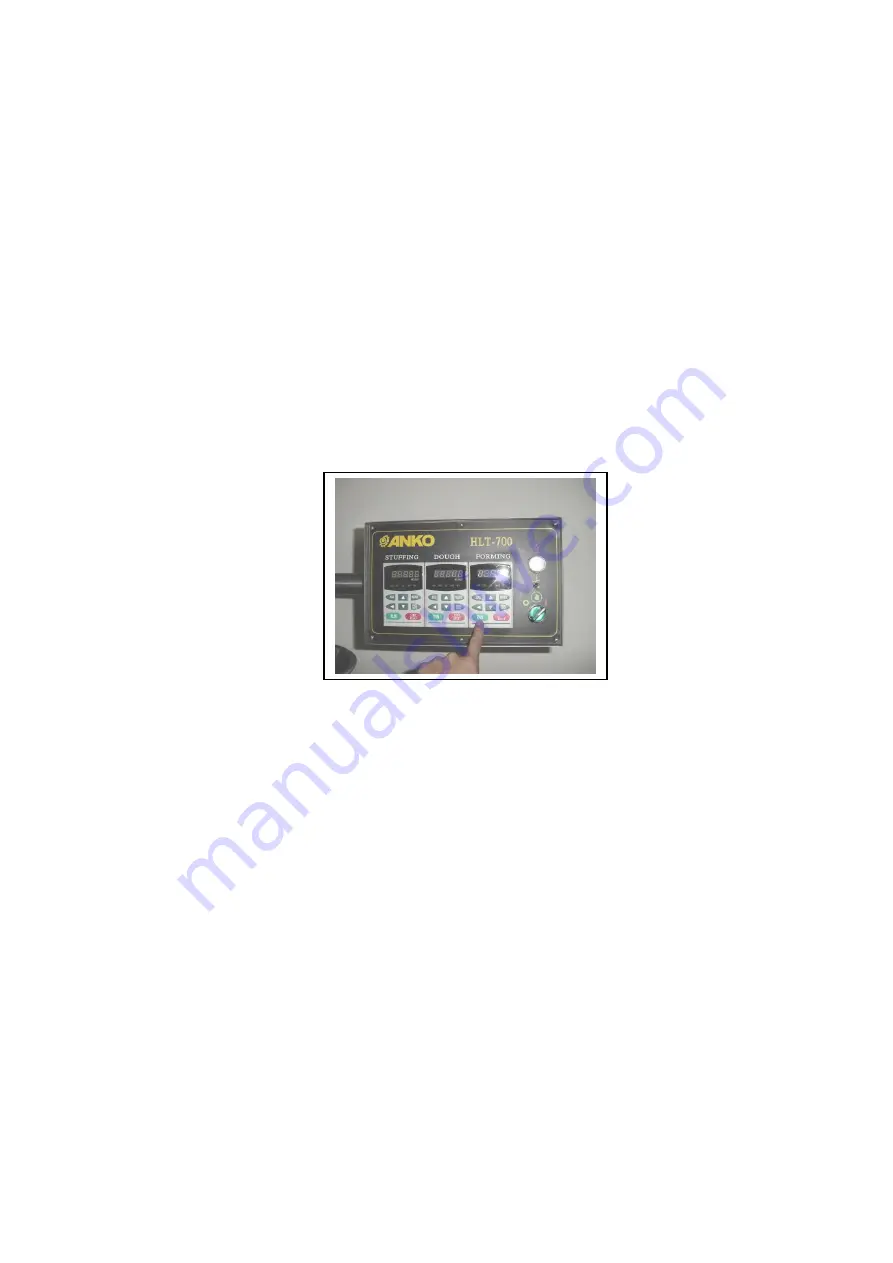
ANKO-OME-0005(A1)
30
F.
1.
Secure the forming mold set with the fixing bolt.
2.
Turn on the forming mold and dough switch at the same time to check
the formed shape of products, adjust the speed of forming system or
dough extrusion system until get proper form.
3.
Turn on the stuffing system and regulate the speed until get proper
volume of stuffing.
※
LED press
△
, the digit will be up and accelerate the speed.
press
▽
, the digit will be down and slow down the speed.
Summary of Contents for 080722
Page 1: ...ANKO OME 0005 A 0 HLT 700 MULTIPURPOSE FILLING FORMING MACHINE OPERATION MANUAL REF 080722 ...
Page 7: ...ANKO OME 0005 A1 4 2 Dimensions ...
Page 14: ...ANKO OME 0005 A1 11 ...
Page 45: ...42 ANKO OME 0005 A1 13 CIRCUIT DIAGRAMS 1 2 2 0 V ...
Page 46: ...43 ANKO OME 0005 A1 ...
Page 47: ...44 ANKO OME 0005 A1 ...
Page 48: ...45 ANKO OME 0005 A1 ...
Page 49: ...46 ANKO OME 0005 A1 ...
Page 50: ...47 ANKO OME 0005 A1 ...
Page 51: ...48 ANKO OME 0005 A1 2 3 8 0 V 4 1 5 V 4 4 0 V ...
Page 52: ...49 ANKO OME 0005 A1 ...
Page 53: ...50 ANKO OME 0005 A1 ...
Page 54: ...51 ANKO OME 0005 A1 ...
Page 55: ...52 ANKO OME 0005 A1 ...
Page 56: ...53 ANKO OME 0005 A1 ...
Page 59: ...ANKO OME 0005 A1 56 15 PARTS LIST A Stuffing Injection System ...
Page 61: ...ANKO OME 0005 A1 58 B Forming Mold System ...
Page 63: ...ANKO OME 0005 A1 60 C Gearbox Dough Extrusion System ...