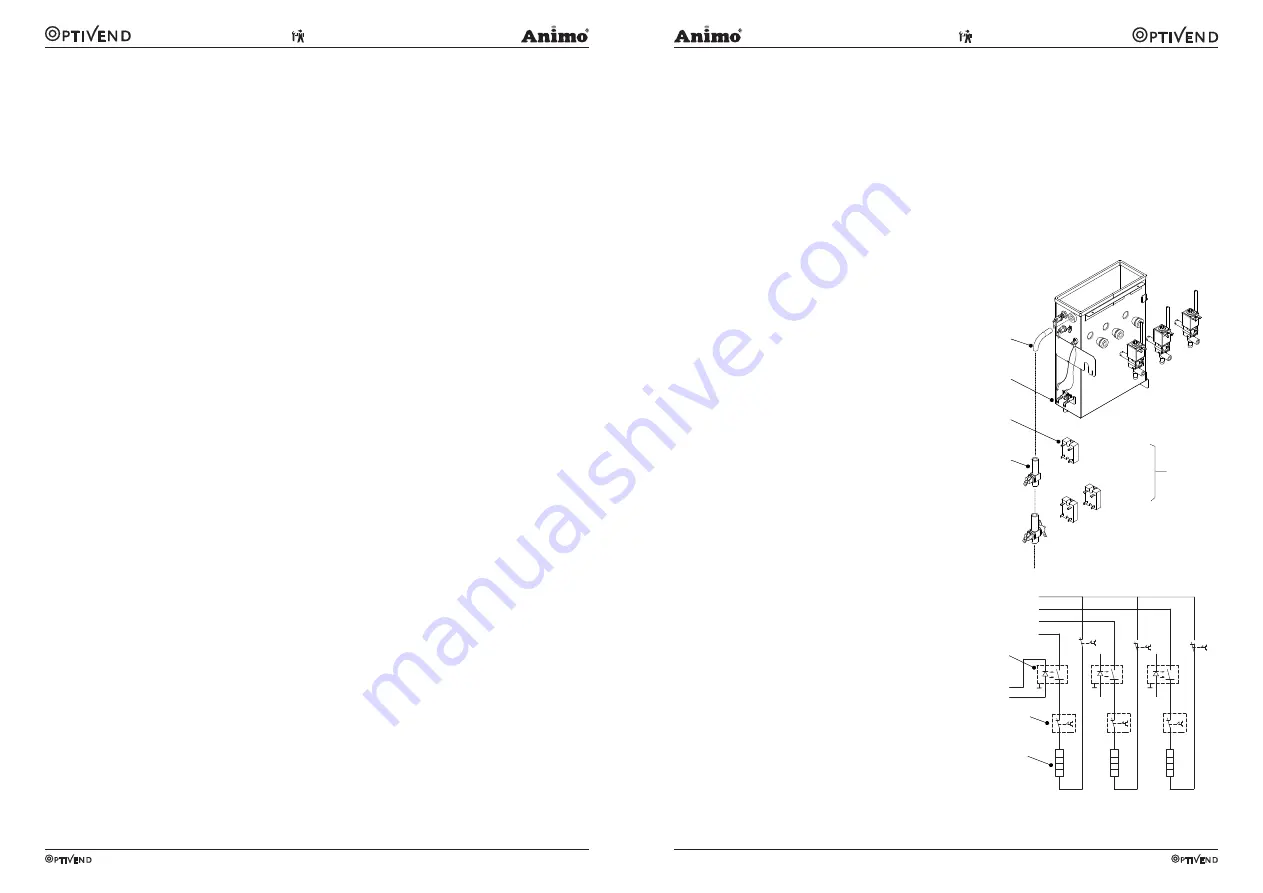
48
06/2011 Rev. 7.4
M o d e l 2 0 0 9
06/2011 Rev. 7.4
49
M o d e l 2 0 0 9
1.1 Boiler System
Turn on the device using the ON/OFF switch. The display will light up.
The magnetic valve ( g. 1-13) will open and the hot water reservoir ( g. 1-4) will be lled to the
maximum electrode. The heating element will be switched on. The display shows [
boiler fi lling
] and
[
boiler heating
]. As soon as the NTC sensor measures the set temperature, the heating element will
be switched off.
When a drink is being dispensed the water level drops and the maximum electrode is released;
the inlet valve (2.5 litres/min.) opens and immediately re lls the reservoir until the maximum level
is reached again. If the water level falls under the minimum electrode level during operation, the
operating panel display will show [re lling boiler]. If the supply of water is not restored within 90
seconds, the display will show the error message [
E3 level error
] and shut off the inlet valve.
1.2 Temperature regulation
The heating element is turned on when the water temperature falls below the temperature setting and
the minimum electrode registers water. The temperature in the water reservoir is measured using an
NTC precision sensor mounted on the outside wall of the reservoir.
The water temperature also drops when drinks are dispensed. To avoid the temperature regulator from
responding too late, the heating element is switched on as soon as the inlet valve ( g. 1-13) opens
and cold water is added. The heating element switches off again as soon as the inlet valve shuts
off. The software can also be used to delay when the heating element switches off. See menu item
2.4 Settings / Temperature in the service menu. The heating element always switches off when the
maximum boiler temperature of 99C is reached.
1.3 Hot water dispensing
When dispensing drinks one of the dispensing valve ( g. 1-3) opens and hot water ows the mixer
system. The ow velocity for each valve is set using the adjustment screw on the valve. The amount of
out ow is determined by the length of time that the valve stays open. In order to rinse the brewer unit
and mixer system, a small amount of rinsing water is released shortly after dispensing to rinse away
any ingredient residue.
1.4 Cold water dispensing (optional)
OptiVend has a built-in cold water special base cabinet with built-in cooling unit. When
dispensing a cold-water recipe, inlet valve DV6 opens ( g. 1-14) and allows water to ow from the
mains to the cooling unit cooling coil ( g.1-15). The cooled water already present ows directly to
the cold water outlet ( g. 1-6). As soon as the valve shuts off again the cold water dispenser stops
immediately.
1.5 Ingredients and mixer system
The ingredients canisters ( g. 1-1) are powered by a 130 RPM motor ( g. 1-2). The instant product
(ingredient) is forced out of the canister by a coil and drops through the dispensing bent pipes into
the mixer unit ( g. 1-8). At the same time, the dispensing valves ( g. 1-3) dispense hot water into the
mixer unit. The mixer motor ( g. 1-15) blends the instant product with water at a speed of 10,700 RPM
using the mixer rotor ( g. 1-10). The drink ows into the cup via the drink outlet ( g. 1-6). All individual
parts mentioned in this section can be sequentially coordinated using adjustable
parameters (timers) in the control unit.
1.6 Evaporation extractor system
Evaporation released during mixing is largely absorbed
by the evaporation extractor ring ( g. 1-7) and sucked
into the machine via the lter cassette ( g. 1-5). The
evaporation and ingredient residue are absorbed by
the lter. The lter ( g. 1-5) can be easily reached (for
cleaning purposes) by dismantling the mixer unit ( g.
1-8). To a large extent, this prevents evaporation from
entering the canister outlet and making ingredients
damp.
1.7 Solid State Relay (SSR)
The heating element is controlled by a solid state relay
( g. 2C), which supersedes the magnetic switch that
was formerly used for this purpose.
1.8 Steam thermostat
The solid state relay ( g. 2C) is secured by a steam
thermostat ( g. 2D) which is build in line with the over-
ow tube ( g. 2A). The steam thermostat contact is in
series with the solid state. This thermostat prevents the
boiler from boiling empty when the solid state breaks
down in a operating condition. The thermostat switches
the heating element OFF ( g. 2B) when steam escapes
from the boiler. The thermostat must be manually reset.
1N~230V
2N~400V
3N~400V
SSR
SSR
SSR
SSR
L2
N
A
B
C
D
B
C
D
24Vdc
SSR
SSR
L1
L3
Fig. 2