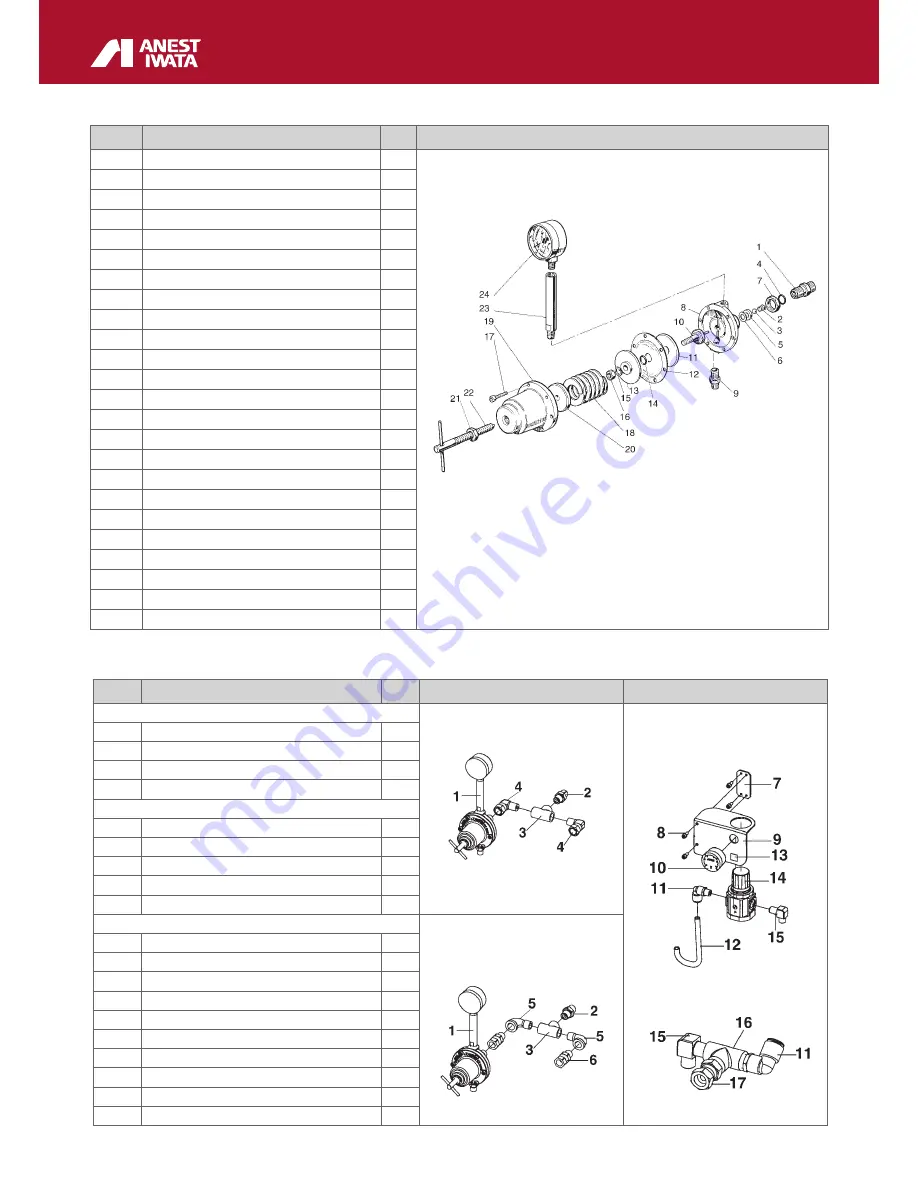
30
Ref.
Description
1
JOINT G3/8”
2
VALVE SPRING
3
CARBIDE BALL
#
4
O’RING
5
CARBIDE SEAT
#
6
PACKING
7
HEX. NUT
8
BODY
•
9
JOINT G1/4”-G3/8”
10
DIAPHRAGM BOLT
11
DIAPHRAGM HOLDER
12
DIAPHRAGM
#
13
DIAPHRAGM STOPPER
14
O’RING
#
15
SPRING WASHER
16
HEXAGON NUT
17
HEX. SOCKET BOLT
18
ADJUSTING SPRING
19
DIAPHRAGM CAP
20
SPRING STOPPER
21
HEXAGON NUT
22
HANDLE SET
23
RISING PIPE
24
PRESSURE GAUGE
10.3 PAINT PRESSURE REGULATOR - A)
PR-5BL | PR-5BLN
Ref. Description
Qty.
for ALUMINIUM TYPE
1
PAINT REGULATOR
1
2
JOINT
1
3
T-JOINT
1
4
ELBOW UNION
2
for STAINLESS STEEL TYPE
1
PAINT REGULATOR
1
2
JOINT
1
3
T-JOINT
1
5
STREET UNION
2
6
UNION JOINT M-F
2
for ALL TYPES
7
SUB PLATE
1
8
BOLT WITH HEX. HOLE
4
9
PLATE
1
10
PRESSURE GAUGE
1
11
ELBOW UNION
2
12
TUBE
1
14
AIR REGULATOR
1
15
ELBOW
2
16
T-JOINT
1
17
UNION JOINT M-F
1
10.4
2-WAY JOINT CONNECTION KIT - OPTIONAL
ALUMINIUM TYPE
ALL TYPES
STAINLESS STEEL TYPE