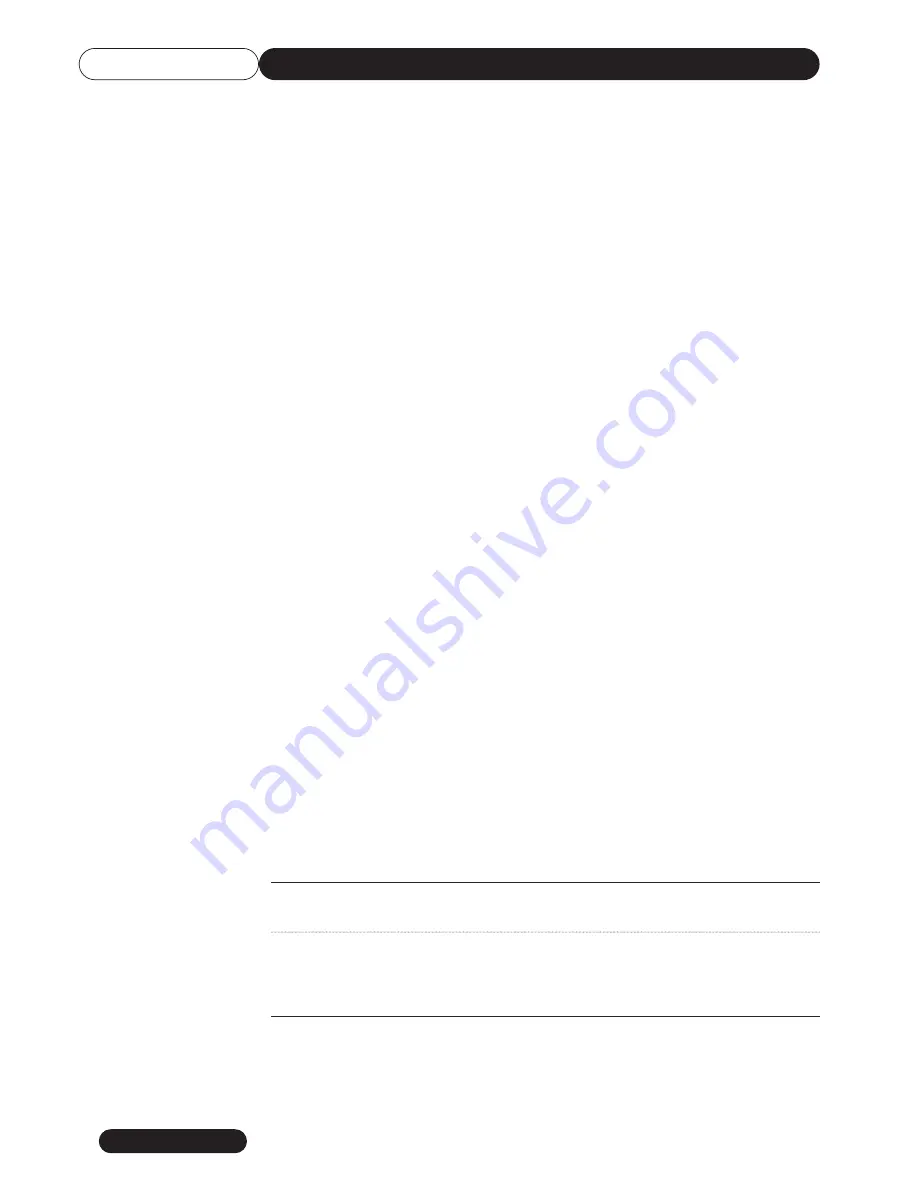
HORIZONTAL
AND VERTICAL
DIRECT FLUE
LENGTHS
INSTALLATION
SECTION 3
Your Andrews Water Heater is a Direct Fan Flued Gas Water Heater where all air for
combustion is obtained from the outside atmosphere and all flue gases are charged to the
outside atmosphere. The flue system is a single coaxial (pipe within pipe) design where
the flue products are discharged through the inside flue tube and the combustion air
supply surrounds the flue surrounded by the outside pipe. The flue system incorporates
both combustion air supply and the flue exhaust. The flue system component which is
outside the building and takes in the combustion air supply and discharges the flue
products (whilst keeping them separate) is referred to as the 'direct flue terminal'.
WARNING!
The direct flue system must be properly installed. Failure to do so could result in property
damage or personal injury. DO NOT install any damaged components. Contact Andrews
Water Heaters for replacement parts. The flow of combustion air must not be restricted.
Keep direct flue terminal openings clear of any objects likely to cause flow restriction.
Direct Flue Terminal
Shall terminate at least 1.5m (5ft) above any forced air inlet located on the same wall.
This provision does not apply to the combustion air intake of a direct flue appliance or
the circulating air inlet and flue gas discharge of listed outdoor appliances.
Shall be installed with at least a 300mm (12in) flue termination clearance from any air
opening into a building.
The bottom of the direct flue terminal shall be located at least 300mm (12in) above
ground.
The Andrews Direct Fan Flued Gas Water Heater is supplied with one direct flue kit.
The flue system supplied with this water heater is a coaxial design with the flue discharge
tube on the inside and combustion air supply on the outside. Optional direct flue
components are available that can extend the horizontal length and/or vertical height of
the direct flue to the maximum distances listed in the table below. This water heater
must be installed using the supplied or optional listed components without modification.
Refer to the table on Page 37 for the various vertical and horizontal direct flue system
components.
NOTE! The supplied horizontal flue terminal may be used through outside walls up to
600mm (24in) thick.
Maximum Flue Distances (Horizontal or Vertical)
Number of 90º Elbows
Maximum length of straight pipe
(excluding vent terminal) to exterior wall
0
7m (22ft 9in)
1
6m (19ft 6in)
2
5m (16ft 3in)
3
4m (13ft 0in)
NOTE! Each 45º elbow reduces the maximum flue distance by 500mm (19.5in).
IMPORTANT! Do not exceed the flue distances or the number of elbows listed
above. This may cause heater malfunction or an unsafe condition.
FLUE
SYSTEMS
12
Summary of Contents for CSC39
Page 3: ......
Page 5: ......
Page 16: ...INSTALLATION SECTION 3 11 Fig 4 Wiring Diagram for LPG Appliance ...