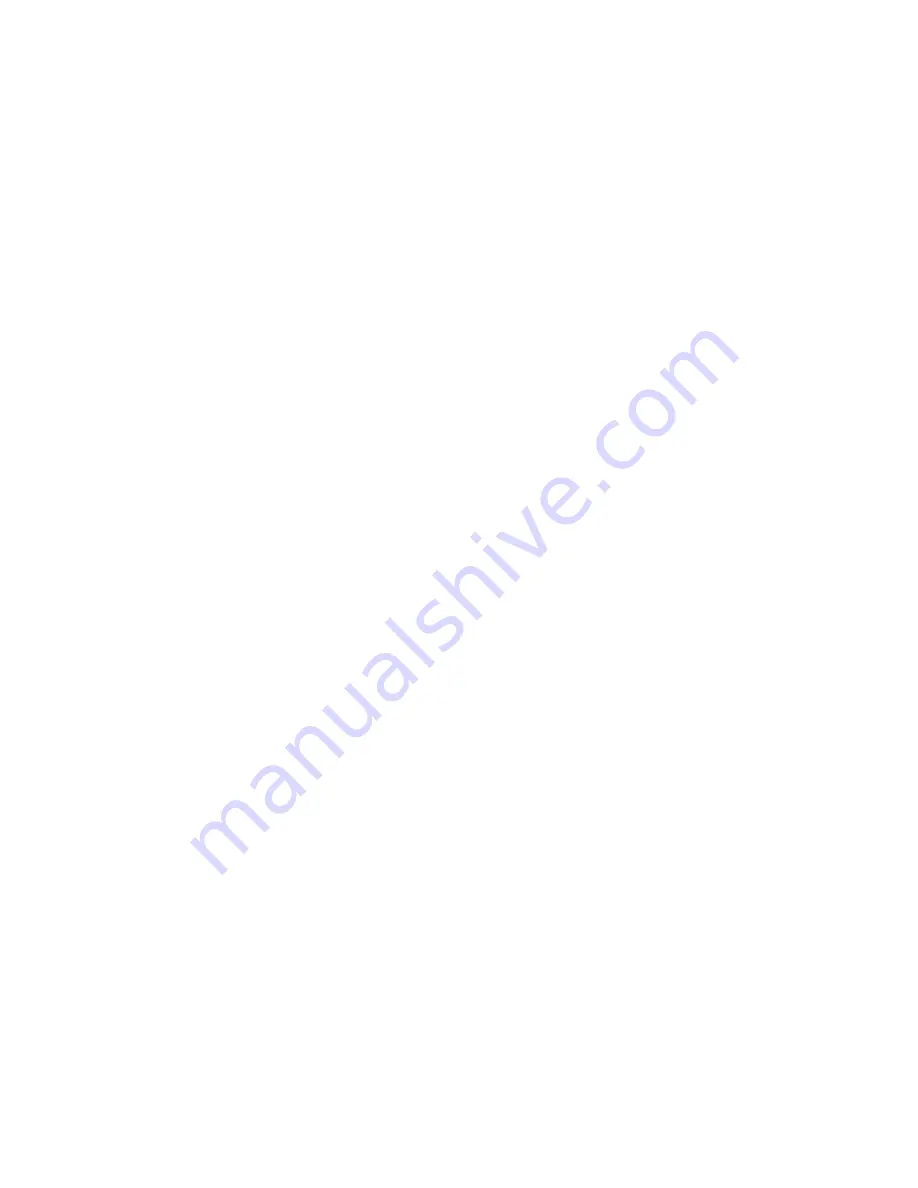
13
#L010155
July 2004
Jog Inputs:
Jog Inputs:
Jog Inputs:
Jog Inputs:
Jog Inputs: The jog switch inputs are internally pulled up by a resistor making them no5 volts.
To activate the input, the pin must be grounded to (0VDC). All jog switch inputs are internally clamped
to +5V, thus allowing voltages of upto +24VDC to be used. Jog is a manual function. The user can
select the direction and speed (fast or slow) by grounding the appropriate combinations of inputs. To
jog a motor, it is necessary to ground the jog input for the direction desired. For fast jog, both the fast
input and jog input for the appropriate direction must be low at the same time. By grounding one of the
jog inputs, the user causes the motor to run at base speed. When the fast input is grounded, the motor
will then accelerate to the programmed jog speed. The position register will keep track of the number of
steps that are taken during jogging. Once a +jog or a -jog function has been performed, the direction
register will retain the last direction of movement; that is, a subsequent go command will be in the same
direction as the last jog command.
Inputs:
Inputs:
Inputs:
Inputs:
Inputs: All inputs (except input 1) are internally pulled up by a resistor making them no5 volts.
To activate the input, the pin must be grounded to (0VDC). All inputs are internally clamped to +5V,
thus allowing voltages of upto +24VDC to be used. Six inputs are provided per axis. The inputs are
TTL, CMOS and 24V compatible. The inputs may be used to initiate a machine cycle, for inter-axis
coordination (in stored program mode), for operator intervention, for sensing a machine condition such
as out of stock or wait for temperature to be reached, etc. A grounded input will read a “0” and an open
or high input will read as a “1”. Input 1 is a special input that is capable of reading an analog voltage
between 0 and +5VDC. Since this input does not have a pull-up resistor, biasing of this input is needed
if it is not used as an analog input. Inputs 5 and 6 are used together with the thumbwheel switch. To
use inputs 5 and 6, SW2 must be in the IN5/6 position. If SW2 is in the TWS position, then these two
inputs are not connected to the processor.
Analog Input:
Analog Input:
Analog Input:
Analog Input:
Analog Input: Input 1 can be configured to read an analog voltage to either set the absolute position of
the motor or to set the maximum speed of the motor.
To set the position
To set the position
To set the position
To set the position
To set the position, when told via the
goto analog position command, the input will read a voltage
between 0 and +5VDC and based on the” upper and lower” limits of the function, a move will occur to a
calculated position between the two limits. The motor must finish the move before it can be told to read
the input again for the next position. For example, if the lower limit is set to 0 and the upper limit is set
to 5000 and the analog position is set at +2.0VDC, then the motor will move to position 2000. Changing
the lower limit to 1000 and the voltage to +3.2VDC, the motor will move to position 3560. See examples
below for calculations of the analog inputs. (Range of limits: 0 to 65535 and the lower limit < upper limit)
To set the max speed
To set the max speed
To set the max speed
To set the max speed
To set the max speed, when told via the
set analog speed command the input will read a voltage
between 0 and +5VDC, and based on the “upper and lower” limits of the function, a max speed can be
obtained based on a calculated frequency between the two points. The speed however can not be
changed when the DPD75601 is busy (moving). See examples below for calculations of the analog
inputs. (Range of limits: 0 to 50000 and the lower limit < upper limit)
Analog calculations.
Analog calculations.
Analog calculations.
Analog calculations.
Analog calculations.
Example1:
Example1:
Example1:
Example1:
Example1:
Example2:
Example2:
Example2:
Example2:
Example2:
(Upper-Lower) * (Voltage/5) = X
(5000 - 0) * (2 / 5) = 2000
(5000 - 1000) * (3.2 / 5) = 2560
Lower + X = Position or Frequency
0 + 2000 = 2000
1000 + 2560 = 3560
Outputs:
Outputs:
Outputs:
Outputs:
Outputs: Eight outputs are provided per axis. Outputs may be used to operate relays, coolant valves,
air cylinders, or, with the correct interfacing, any electronically controlled device. The outputs can drive
all types of common peripheral power loads, including lamps, relays, solenoids, LED’s, printer heads,
and heaters. For inductive loads, it will be necessary to connect a clamping diode (refer to specification
section) from the output to the power source in order to provide adequate fly-back protection. The
outputs are current sinking, open collector darlingtons. They are capable of sinking up to 100mA per
output with voltages up to 40VDC. Turning an output on will pull the output pin to ground and turning an
output off will make the output pin open. Output 1 has a special function
(output on the fly) that will
enable it to be triggered at a certain absolute position during a move.