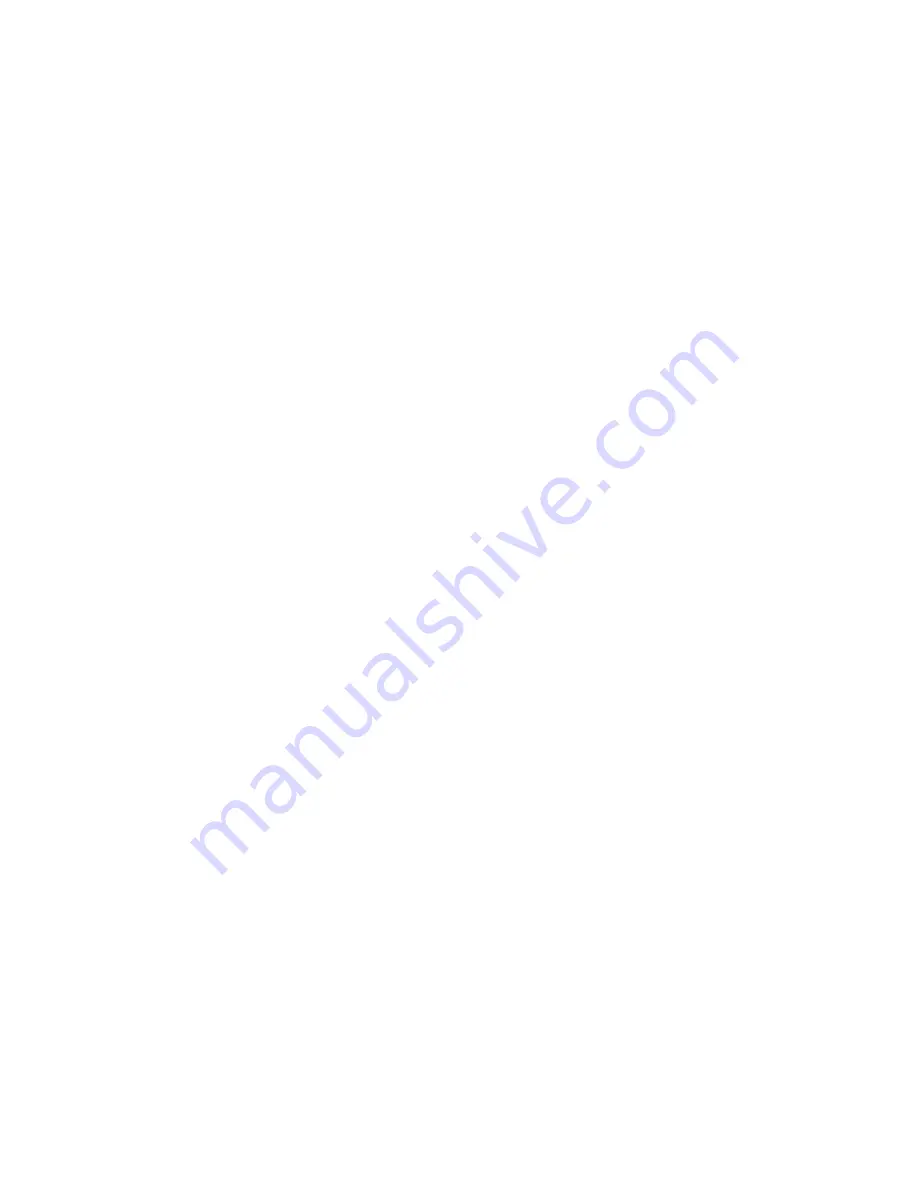
August 2013
L011088
5
Speed Adjust Setting
The maximum speed of the motor is set by adjusting R17. The minimum speed of the motor is
set by adjusting R25. The speed potentiometer is used to adjust the motor speed between the
set minimum and maximum speed.
Motor Run/Brake
The motor run/brake switch allows the stopping or braking of a motor by shorting out the bottom
drives of the three phases.
Motor Direction
The motor direction switch allows the changing of the rotation of the motor. This switch should
not be changed while motion is in progress.
Note: Avoid changing the direction of rotation when the motor is already running in any one direction.
The following instructions must be followed to prevent permanent drive failure due to over-current conditions that exist is dynamic
direction reversals of the motor:
1. Stop the motor by releasing the short on the Run/Stop input
2. Wait for at least 500mS
3. Change the direction with the DIRECTION input
4. Run the motor by shorting the Run/Stop input
Note: Avoid changing the direction of rotation when the motor is already run-
ning in any one direction.
The following instructions must be followed to prevent permanent drive failure due
to over-current conditions that exist in dynamic direction reversals of the motor:
1. Stop the motor with the Run/Brake switch
2. Wait for a least 500mS
3. Change the direction with the DIRECTION switch
4. Run the motor with the Run/Brake switch
Heating Considerations
The temperature of the heat sink should never be allowed to rise above 70 degrees Celsius. This
may occur with motor currents higher than 6A. If necessary, mount the unit to an additional heat
sink or air should be blown across the unit to maintain suitable temperatures.