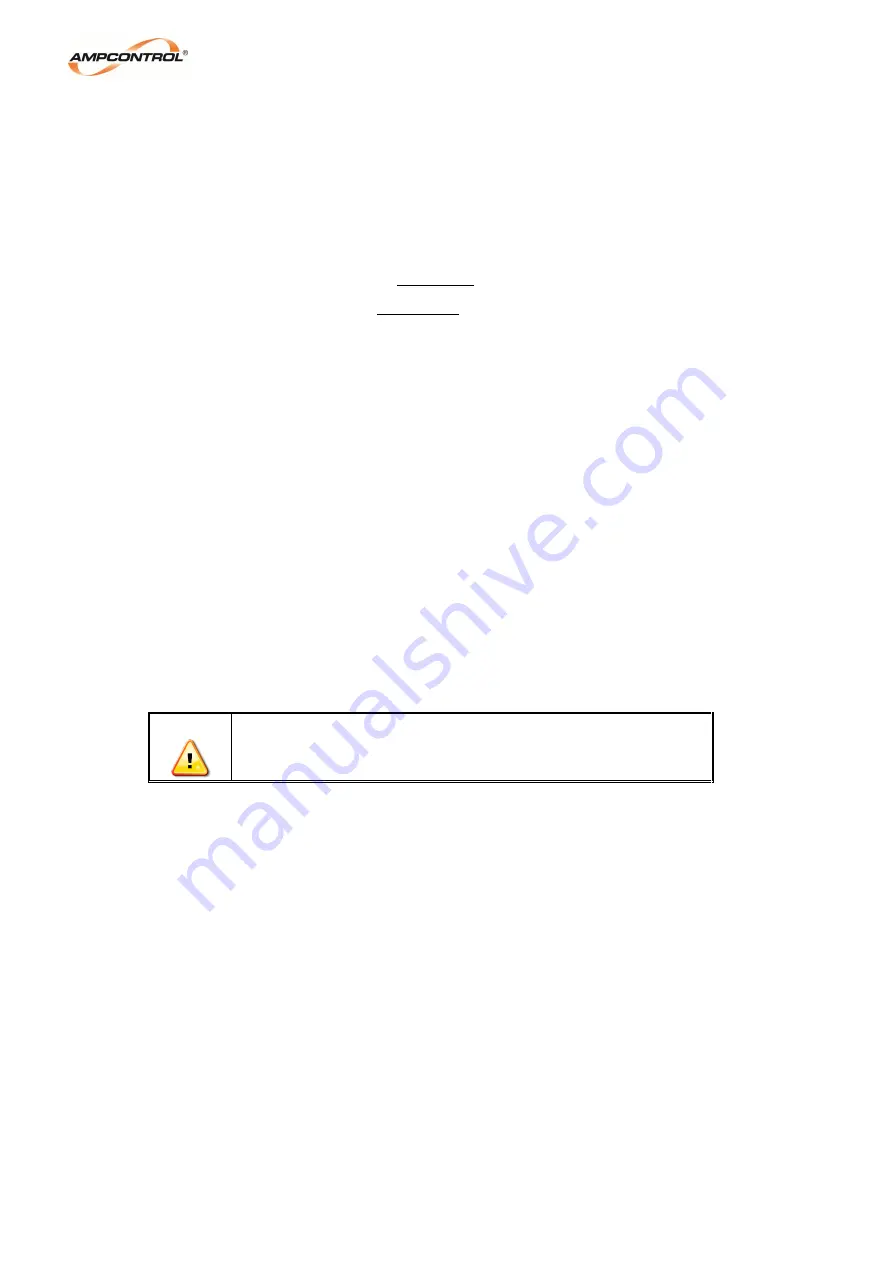
MPA3 V6.3 MOTOR PROTECTION RELAY MANUAL
Issue: R0, Date: 11/2010, CRN: 8168
MPAB010 Rev0
MPA3 V6.2 Motor Protection Relay Manual
Page 12
The trip time is selected via the ‘
6xI Trip t
’ setting (Level 7, Position 2). It is a function of the current and the selected
trip time curve. The drawing ‘MPA Motor Overload and Short Circuit Trip Times’,
, in Appendix A –
Drawings shows the trip time curves.
The fifteen motor overload curves allow trip settings from 3 to 40 seconds at six times FLC and are shown for both
cold and hot conditions. The hot curve corresponds to the trip time after the motor has been running at the selected
full load current indefinitely.
The trip time can be calculated as follows:
1238
.
1
100
%
1238
.
1
ln
53
.
31
2
2
I
A
I
C
Time
Trip
Where:
C
= Curve Selected
I
= Current (FLC = 1)
A% = Initial Thermal Accumulator Value
The motor manufacturer's data should always be consulted to select the appropriate settings for the motor being
protected. Typically, the capacity of a cold motor is given at six times its rated current.
The MPA Relay's trip curves can then be used to select the trip time curve, which best suits the motors overload
capacity.
The motor overload trip latches once the thermal accumulator reaches 100% and can only be reset once the thermal
accumulator falls below a preset value. The pre-set value is selected via the ‘
O/L Reset
’ setting (Level 7, Position 3)
and can be set to 30%, 40%, 50%, 60%, 70%, 80%, 90%, A-30%, A-40%, A-50%, A-60%, A-70%, A-80%, A-90%.
The A- settings automatically reset a motor overload trip once the thermal accumulator falls below the set value.
Otherwise the trip has to be reset manually by pressing the keypad ‘RESET’ button or activating the ‘RESET’ digital
input once the thermal accumulator has fallen below the set value.
An emergency restart on a hot motor can be achieved by zeroing the thermal accumulator memory. This is done by
closing the
E/start
input and
reset
key/digital input simultaneously for 1.5 seconds.
CAUTION!
Repeated attempts to restart the motor in this condition may damage
the motor.
The ‘Stopped Cooling Ratio’ modifies the cooling output of the thermal model when the motor is stopped. This can be
used to account for reduced cooling capacity of the motor when it is not running (motor run status monitored via MCI
digital input).
The ratio is selected via the ‘
S-Cool Ratio
’ setting (Level 7, Position 4) and is adjustable from 1.0 to 5.0. A cooling
multiplier of 1 means the cooling is independent of whether the motor is running or not - e.g. a water-cooled motor.
Protection for a fan-cooled motor is based on a setting of 2.5, however, for the best protection consult the motor
manufacturer.