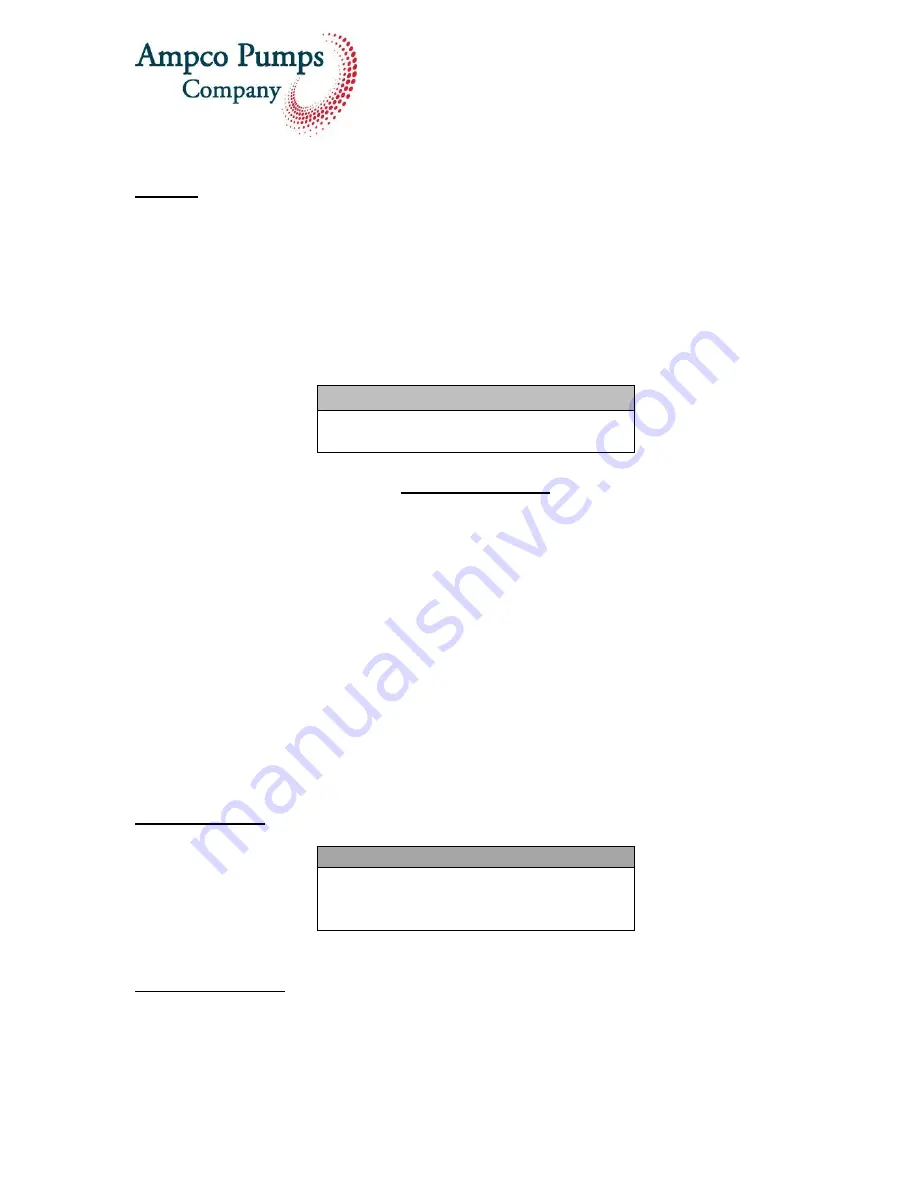
F-750-025-A / rev 12.20 – ZCM- ZCHM Series Metric Manual
4
Priming
The Z-Series pump is not a self-priming pump and must be completely filled
with the pumping liquid before operation. If the system has a positive suction head priming
can be done by opening the valve in the suction piping as well as the pump’s air vents to allow
the liquid to enter the pump casing. Rotate the shaft by hand to free entrapped air from the
impeller and then ensure that all air has been forced out by the liquid before closing the air
vents. If the pump has a suction lift, priming must be done by using foot valves, ejectors or
manual filling of the pump casing.
CAUTION!
Running the pump dry will result in
serious damage to the mechanical seal.
Pre-Start Checklist
Before operating the Z-Series pump ensure that all of the following requirements are met
o
Check that all motor and starting device wirings match the wiring diagram.
o
Make sure the shaft rotates clockwise when viewed from behind the motor.
o
Refer to motor instructions before starting if the motor has not been operated over an
extended period of time.
o
Make sure that that voltage, phase, and line circuit frequency match what is specified
on the motor data plate.
o
Turn shaft by hand to make sure it rotates freely.
o
Tighten all gauge and drain tap plugs. When not in use, close the gauge cocks on
pumps fitted with pressure gauges.
o
Check that all flange bolts are tightened and the suction and discharge piping is not
leaking.
Pump Operation
WARNING
Operating the pump without an approved
coupling guard installed could result in
operating personnel injury.
Start Up Instructions
1. Set the suction line gate valve to full open and close the discharge line gate valve.
2. Fill the suction line and prime the pump.
3. Start the motor and immediately check the pump and suction piping for leaks.