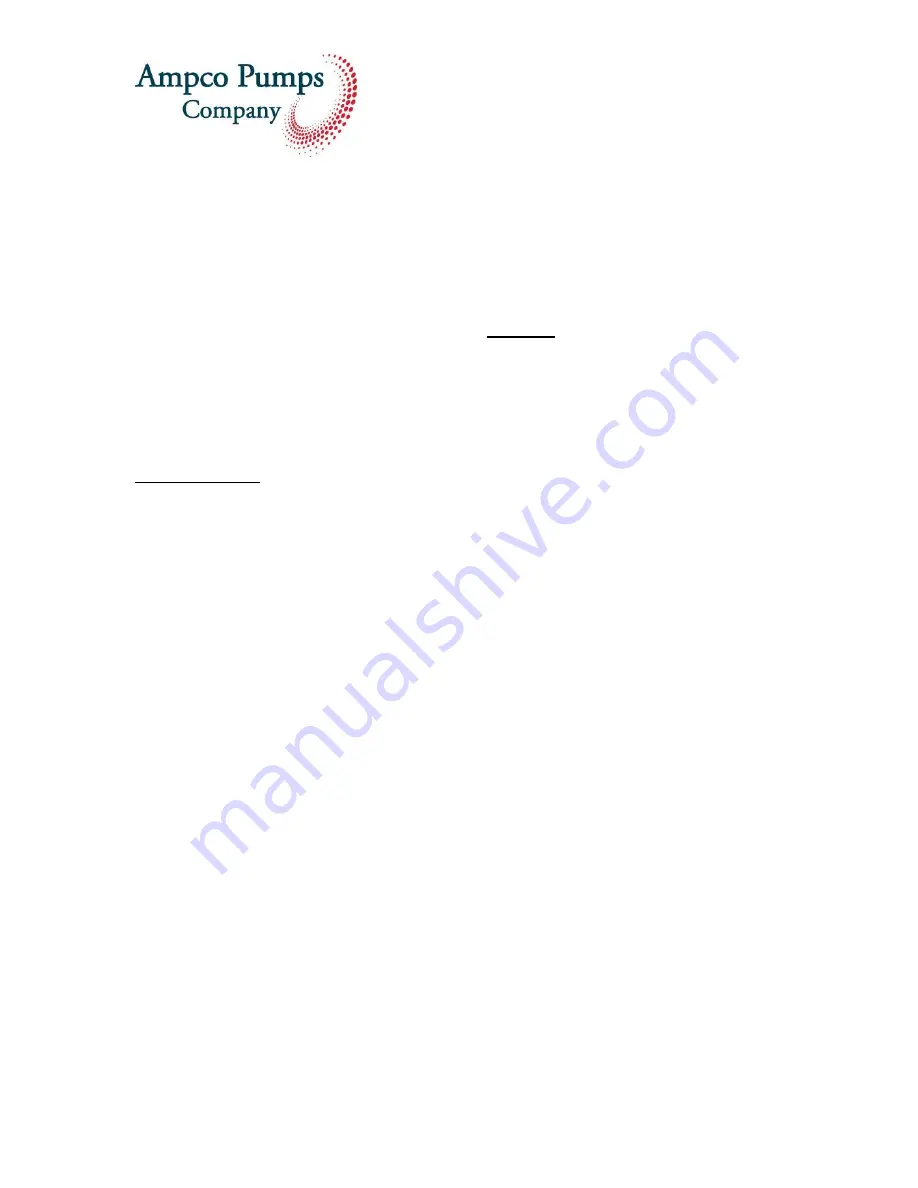
F-750-025-A / rev 12.20 – ZCM- ZCHM Series Metric Manual
3
High point such as loops or arcs must be avoided as they may create air pockets,
throttle the system, and produce erratic pumping.
A valve must be installed in the suction piping in order to isolate the pump during
shutdown and maintenance, and to facilitate pump removal. If two or more pumps are
connected to a single suction line, each pump should be isolated by a separate valve.
Gate valves need to be positioned so that air pockets are not produced. If NPSH is
critical, globe valves should not be used. (
Note: During operation all valves
installed on the suction line must be at full open
)
To enable the pump operator to monitor pump performance, properly sized pressure
gauges may be installed in gauge taps on pump suction and discharge nozzles.
Pressure gauges will also indicate the presence of cavitation, vapor binding, or other
unstable operation by showing wide fluctuations in suction and discharge pressures.
For these reasons Ampco highly recommends gauges.
Discharge Piping
To ensure proper pump performance the following precautions regarding discharge
piping should be followed:
If the discharge piping distance is short the piping can be the same diameter as the
pump discharge opening.
Long horizontal lengths of discharge piping should maintain an even gradient.
A valve needs to be installed near the pump’s discharge opening to prime and start the
pump, as well as to isolate the pump during shutdown, maintenance, and to facilitate
pump removal.
High points should be avoided in discharge piping as they can entrap air or gas and
retard pump operation.
If liquid hammer might exist, such as when check valves are used, the discharge gate
valve should be closed prior to pump shutdown.