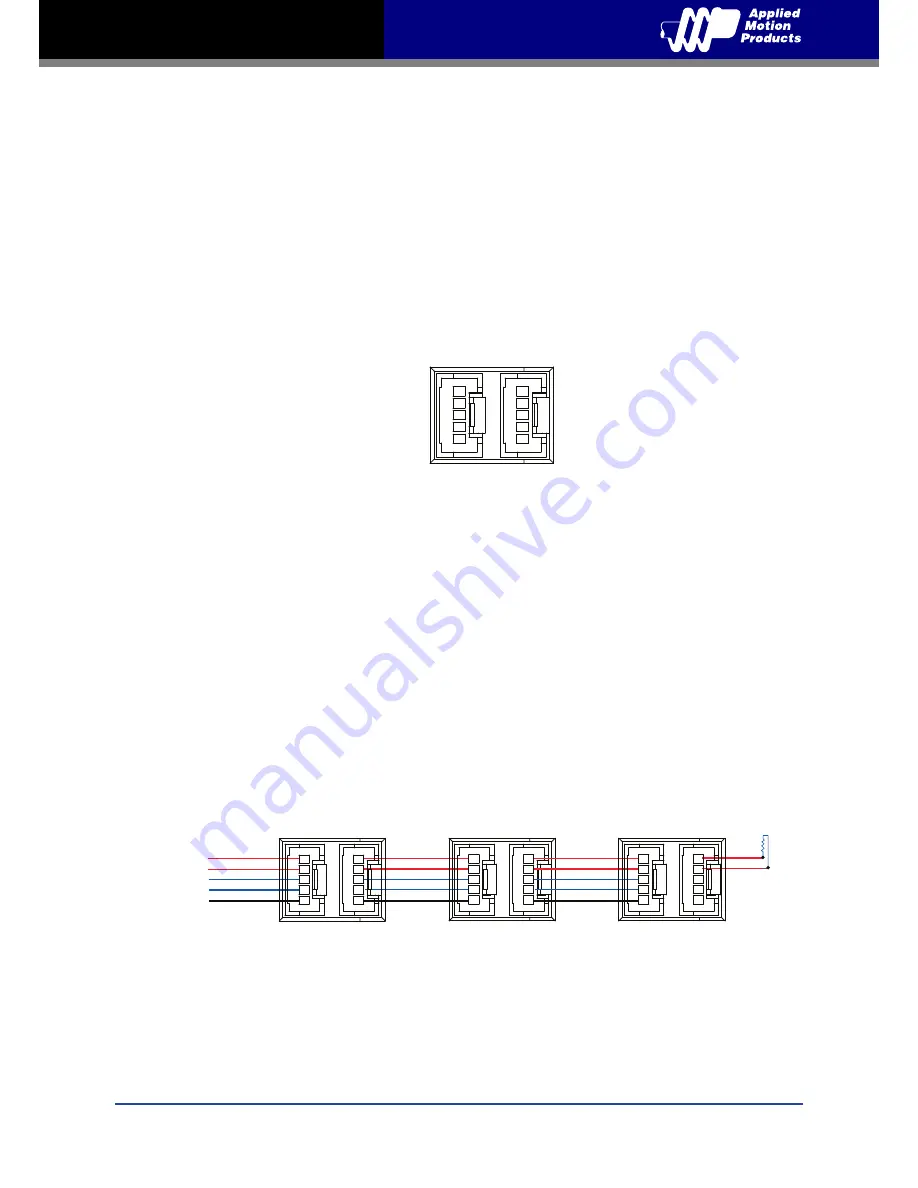
15
Rev. A
920-0081
TSM23S/Q Hardware Manual
3.2.2 Connecting to a Host using RS-485
RS-485 communication allows connection of more than one drive to a single host PC, PLC, HMI
or other computer. It also allows the communication cable to be long (more than 300 meters
or 1000 feet). The use of Category 5 cable is recommended as it is widely used for computer
networks, inexpensive, easily obtained and certified for quality and data integrity.
The TSM23S/Q can be used with either Two-Wire or Four-Wire RS-485 implementation. The
connection can be point-to-point (i.e. one drive and one host) or a multi-drop network (one host
and up to 32 drives).
NOTE: To use the TSM23S/Q RS-485 version with the Step-Servo Quick Tuner software, it
must be connected in the Four-Wire configuration (see below)
RS-485 Connector Diagram
Four-Wire Configuration
Four-Wire Systems utilize separate transmit and receive wires. One pair of wires must connect the
host’s transmit signals to each drive’s RX+ and RX- terminals. The other pair connects the drive’s
TX+ and TX- terminals to the host’s receive signals. A logic ground terminal is provided on each
drive and can be used to keep all drives at the same ground potential. This terminal connects
internally to the DC power supply return (V-), so
if all the drives on the RS-485 network are
powered from the same supply, only one drive’s GND terminal should be connected to the
host computer ground, others’ GND terminal must not connect the logic grounds
.
Because the host in a four-wire system never needs to disable its transmitter, software is
simplified. Some converters make this process very difficult to implement and can delay
communications.
NOTE: If the PC does not have an RS-485 serial port, a converter is required.
You can contact Applied Motion Products to buy a USB to RS-485 converter.
RX+
RX-
TX+
TX-
GND
to PC GND
to PC RX-
to PC RX+
to PC TX-
to PC TX+
Drive #1
Drive #2
Drive #N
RX+
RX-
TX+
TX-
GND
RX+
RX-
TX+
TX-
GND
RX+
RX-
TX+
TX-
GND
120Ω
RX+
RX-