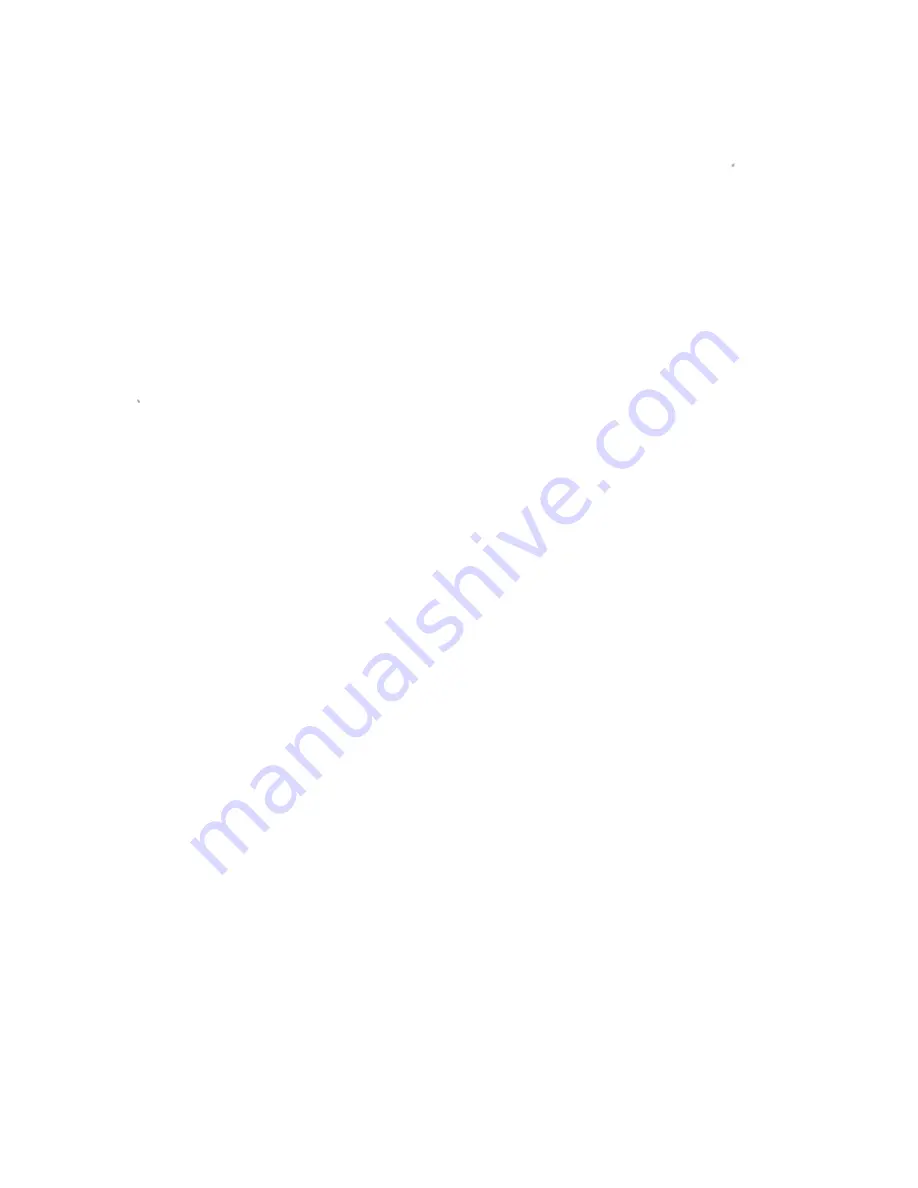
21
Attention: come into eye carelessly: use water in the
container to wash at least 15 minutes. (water with pressure
will let eye injured), then have medical treatment; Contact
with skin carelessly: take off cloth and wash skin with much
water, then have medical treatment; Come into body
carelessly: drink a lot of water or milk, then have medical
treatment.
8.5 Fuel
8.5.1 Ethanol in the fuel we purchase can have damaging
effects to the fuel system. It is important that you never let
fuel sit in the carburetor of the unit for longer than 30 days.
If you will not be running the unit for 30 days or longer we
strongly urge you turn the fuel petcock off and run the unit
until the remaining fuel is burned off.
8.5.2 Metamorphic fuel will cause difficulty starting your 3
in
1 . It will cause colloid sediment to block the fuel system. If
you find your fuel to be metamorphic, you should maintain
or replace the carburetor immediately.
8.5.3 You must never let fuel sit or be stored for more than
30 days in your AMP Triplex 3 in 1 .
8.6 Taking off fuel tank and carburetor
Fuel is highly combustible and explosive. It is important to
remember when handling fuel you can easily be burned or
hurt. Make sure the engine is shut down away from heat,
sparks and flames. Only deal with fuel issues outdoors.