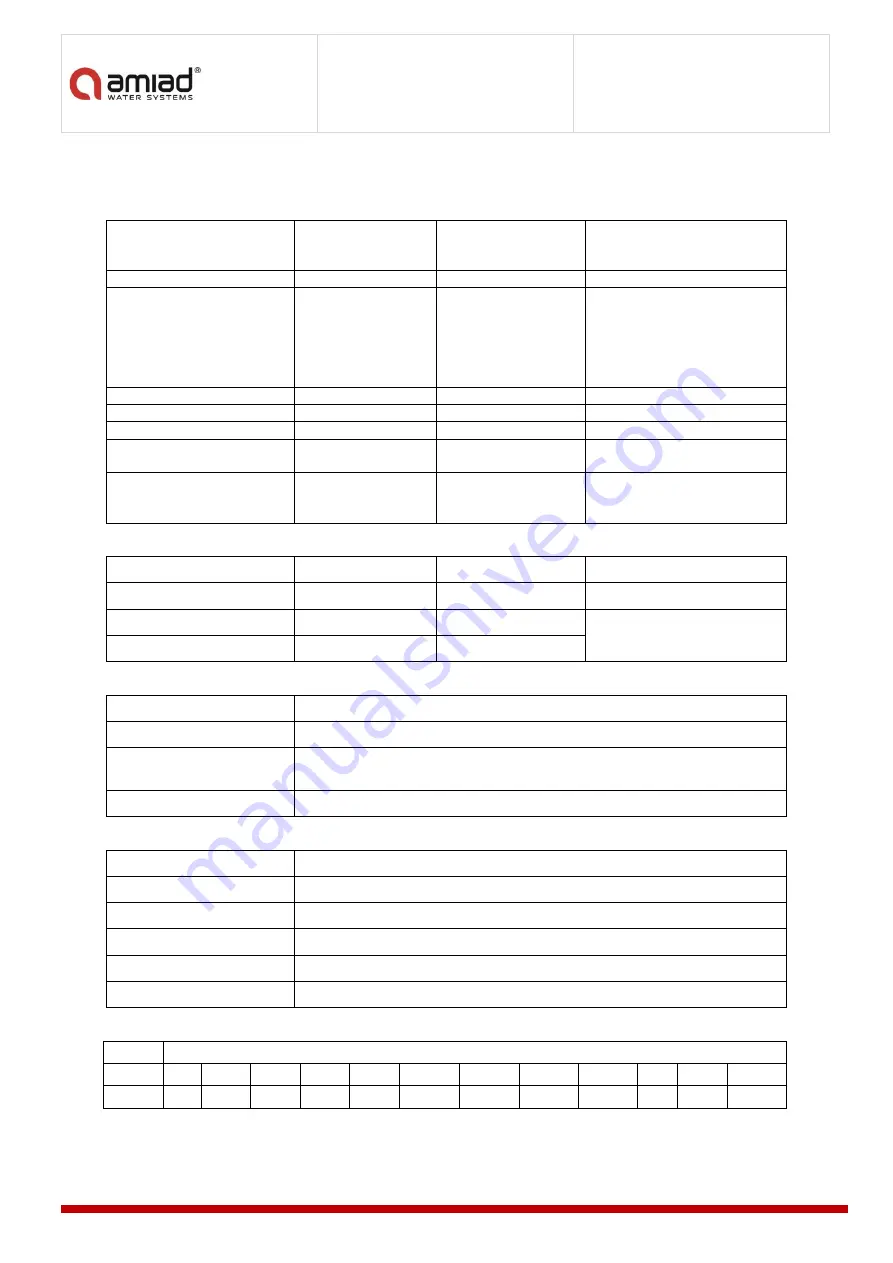
Installation & Operation Manual
SAF-X
01.2022
/
001301
-
910101
9
5.
Technical Specifications SAF-X 3000
General
Maximum flow rate
160 m
3
/hr
700 gpm
Consult manufacturer for
optimum flow depending on
filtration degree & water quality.
Design Pressure
10 bar(g)
150 psi
Min. Operating pressure
2.0 bar(g)
30 psi
Pressure is critical during the
flushing cycle.
Consult manufacturer for the
required values according to
filtration degree and operation
conditions.
Temperature Min / Max
4
0
/ 50
0
C
39.2
0
/ 122
0
F
Filtration area
3000 cm
2
465 in
2
Inlet/Outlet diameter
80,100,150 mm
3", 4", 6"
Flange standards as per request.
Filter housing
250 mm
10"
Epoxy-coated steel, or other on
request.
Weight: empty / Operation
80 mm = 118/188 Kg
100 mm = 121/191 Kg
150 mm = 126/196 Kg
3" = 260/414 lb.
4" = 266/420 lb.
6" = 277/431 lb.
Flushing Data
Exhaust valve
50 mm
2"
Flushing cycle time
20 seconds
20 seconds
Reject volume per cycle
78 liter
20 gallon
STD Nozzle
at 2.5 bar/35 psi
Minimum flow for flushing
14 m3/h
62 gpm
Control and Electricity
Control voltage
120 & 24 VAC or 24VDC
Electric motor
1/4 HP (0.18 kW) 50/60 Hz,
Rated operation Voltage
3 phase 208/230/380/400/415/460/575 Volt 50/60 Hz
Single phase, 120/240 Volt 50/60 Hz
Current consumption
0.6 Amp. (see electrical diagram for specific values)
Construction Materials
Filter Housing and Lid
Epoxy-coated carbon steel 37-2 (Stainless Steel 316 available on request).
Screens
Stainless Steel 316
Cleaning mechanism
Stainless Steel 316, POM, PVC
Exhaust valve
Epoxy-coated cast iron, Natural Rubber
Seals
Synthetic Rubber
Control
Aluminum, Brass, Stainless Steel, PVC
Standard Filtration Degrees
Stainless Steel Weave-wire Screen
micron
800
500
300
200
130
100
80
50
40
30
20
10
mm
0.8
0.5
0.3
0.2
0.13
0.1
0.08
0.05
0.04
0.0
3
0.02
0.01