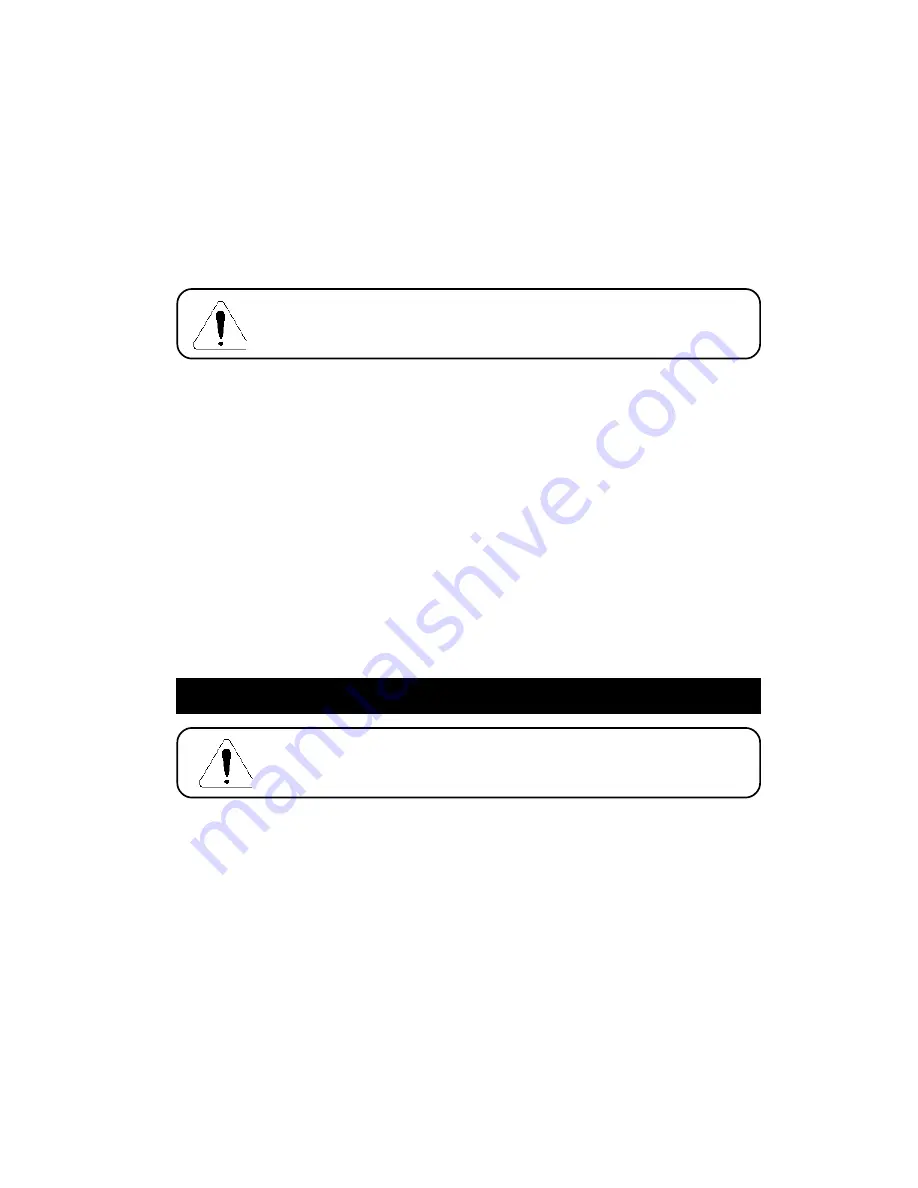
When the motor is supplied with protective or monitor
temperature device such as thermostats, thermistors, thermal
protector, etc, connect their terminals to the corresponding
devices on the control panel.
10- Start-Up
THE KEY MUST BE FASTENED OR REMOVED
BEFORE STARTING THE MOTOR.
a) The motor must start and operate smoothly. In case this
does not occur, turn it off and check the connections and the
mounting before starting it again.
b) If there is excessive vibration, check if the fastening
screws are correctly fastened. Check also if the vibration comes
from a neighbour machine. Periodical vibration checks must
be done.
c) Run the motor under rated load for a short period of
time and compare if the running current is equal to that
stamped on the nameplate.
1 - General Inspection
9
Check the motor periodically.
9
Keep the motor clean and assure free air flow.
9
Check the seals or V Ring and replace them, if required.
9
Check the connections as well as supporting screws.
9
Check the bearings and observe:
Any excessive noise, bearing temperature and grease
condition.
9
When a changing, under normal conditions, is detected,
check the motor and replace the required parts.
The frequency of the inspections depends on the motor
type and on the application conditions.
MAINTENANCE
WARNING:
SAFETY CHECK LIST.
Summary of Contents for BMF Series
Page 17: ...Rev 10 2017 BMF Pre Engineered Skid IOM 17 PUMP CURVES ...
Page 18: ...Rev 10 2017 BMF Pre Engineered Skid IOM 18 ...
Page 19: ...Rev 10 2017 BMF Pre Engineered Skid IOM 19 ...
Page 20: ...Rev 10 2017 BMF Pre Engineered Skid IOM 20 ...
Page 21: ...Rev 10 2017 BMF Pre Engineered Skid IOM 21 ...
Page 22: ...Rev 10 2017 BMF Pre Engineered Skid IOM 22 ...
Page 23: ...Rev 10 2017 BMF Pre Engineered Skid IOM 23 ...
Page 24: ...Rev 10 2017 BMF Pre Engineered Skid IOM 24 ...
Page 34: ...Rev 10 2017 BMF Pre Engineered Skid IOM 34 Appendix 1 Pump IOM ...
Page 35: ...INSTALLATION AND MAINTENANCE INSTRUCTIONS FOR ELECTRIC MOTORS Frames 143 5T 586 7T ...