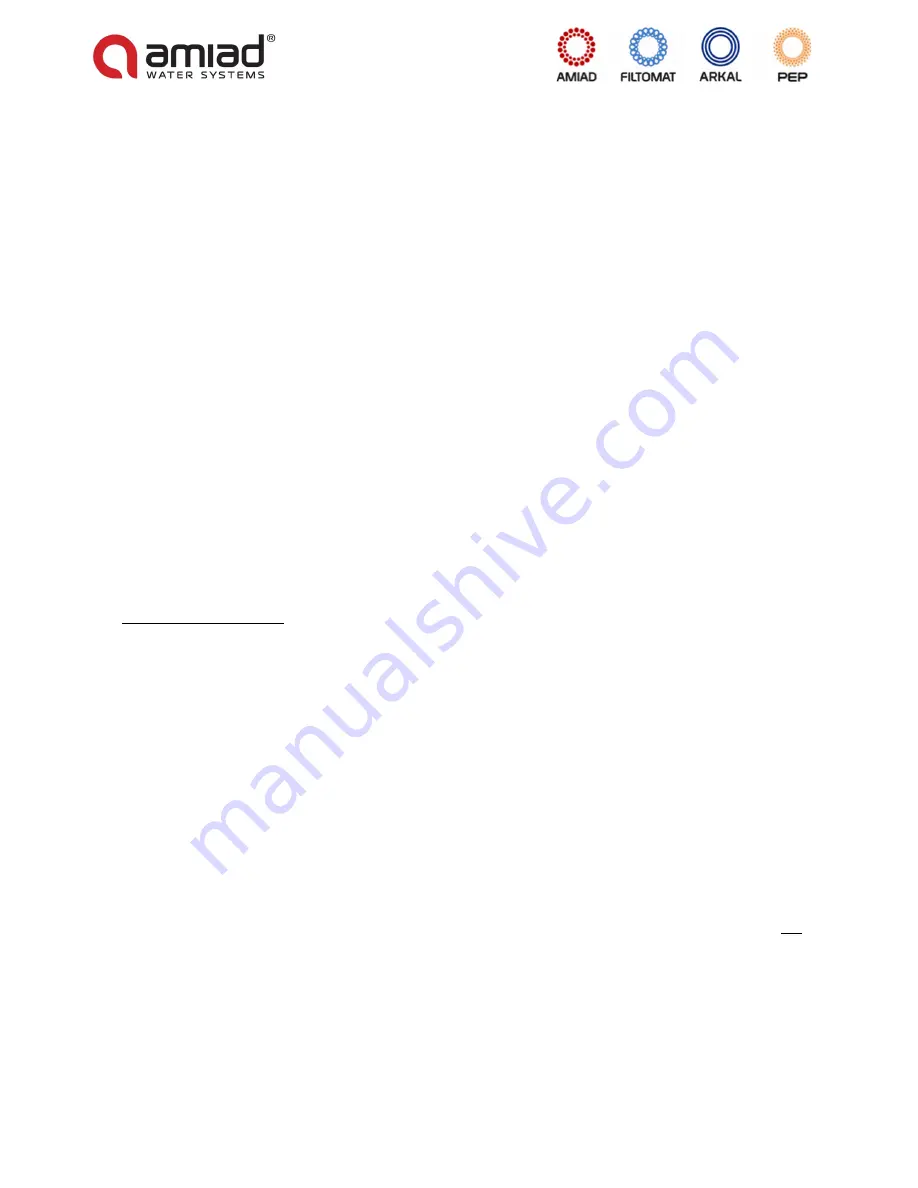
Rev: 10.2017
BMF Pre-Engineered Skid IOM
4
Rigging
Amiad BMF filters should be lifted with a forklift or overhead crane. If these units are lifted with an
overhead crane, lifting straps must be located below the filter skid and should not come in contact
with the filter components. If no skid is supplied, lift from the lifting lugs located on the filter vessel
top.
All Amiad BMF filters should be rigidly anchored to the floor or support steel by means of anchor bolts.
All filters have an anchoring provision.
Once the filter in installed in its permanent location, the
pressure gauge and air relief valves should be installed on the top of the filter
tank (some units will
have these items already installed). The sand media is loaded into the filter next. Refer to the section
in this manual
“Loading the Media” for the proper loading procedure and the appropriate quantity of
media necessary for each size filter vessel.
Piping
The Amiad BMF should be installed using the pipe size indicated in
Table 2
.
Connect the unfiltered source water from the system sump or piping to the connection labeled “Inlet”.
NOTE
: All Amiad BMF systems have end suction centrifugal style pumps that require flooded suction
for proper operation. Piping to the pump suction inlet should be plumbed
to ensure the pipe is full of
water at all times.
Connect the return line from the connection labeled “Outlet” to the system sump or filtered water
return piping.
A service or isolation valve should be installed on the inlet, outlet and city water line (if city water is
used) to allow filter servicing. For units using a backwash source other than the system sump, refer
to Table 3 for the required backwash flow rate. The maximum city water backwash supply pressure to
the filter vessel should never exceed the vessel pressure rating (100 PSI as standard). If public or
municipal water is used for backwash, a back/low prevention device or check valve is required on the
city water line (in accordance with local or other governing codes).
A backwash throttle valve
should be placed on the backwash discharge manifold to control the volume
of water that can escape during backwash. Obtaining the proper flow rate of the backwash water is
essential for effective flushing of the media. Too high of a flow will flush all of the media out of the
tank. Too low of a flow will not allow the media to gently lift, fluidize and flush filtered particulates
from the media in the system. The proper flow rate is dependent on the size of the tank being
flushed. The most common way to adjust the backwash throttle valve is to manually set the filter(s) to
backwash with the throttle valve fully closed. Slowly open the throttle valve until small amounts of
media are evident in the backwash discharge. It is desirable to have a slight amount of media
discharge during backwash. You should expect to lose several inches of sand per year with proper
backwashing. Although the media fills 2/3 of the tank, it makes most sense to try to keep the
contamination in the top two inches of the media bed. This will allow you to quickly rinse the media
during the backwash sequence. If the media contamination reaches depths below two inches, it will
take a much longer backwash to rinse the media. This can also cause contamination of the under drain
of your filter system. Proper backwash frequency must be determined to minimize contamination and
clogged under drains.
Refer to
Table 3
for the minimum and maximum backwash flow rates. Note: if the drain is not large
enough to handle the volume of water during backwash, it may be necessary to use a backwash water
holding tank to buffer the backwash flow rate from the filter to the waste drain. A valve can be used
to regulate the flow from the holding tank at a reduced flow rate that is suitable for the drain. Do not
reduce the waste line pipe to regulate backwash flow rate as this will adversely affect the backwash
cycle and cause accumulated waste in the filter vessel.
All inter-connecting piping, fitting, valves, or other accessories connected to the filter system (whether
supplied by Amiad or others)
must be independently supported to eliminate stress on piping. Check
with local or other governmental authority to ensure compliance with applicable codes.
All Amiad BMF filter vessels have a drain plug located on the bottom.
Summary of Contents for BMF Series
Page 17: ...Rev 10 2017 BMF Pre Engineered Skid IOM 17 PUMP CURVES ...
Page 18: ...Rev 10 2017 BMF Pre Engineered Skid IOM 18 ...
Page 19: ...Rev 10 2017 BMF Pre Engineered Skid IOM 19 ...
Page 20: ...Rev 10 2017 BMF Pre Engineered Skid IOM 20 ...
Page 21: ...Rev 10 2017 BMF Pre Engineered Skid IOM 21 ...
Page 22: ...Rev 10 2017 BMF Pre Engineered Skid IOM 22 ...
Page 23: ...Rev 10 2017 BMF Pre Engineered Skid IOM 23 ...
Page 24: ...Rev 10 2017 BMF Pre Engineered Skid IOM 24 ...
Page 34: ...Rev 10 2017 BMF Pre Engineered Skid IOM 34 Appendix 1 Pump IOM ...
Page 35: ...INSTALLATION AND MAINTENANCE INSTRUCTIONS FOR ELECTRIC MOTORS Frames 143 5T 586 7T ...