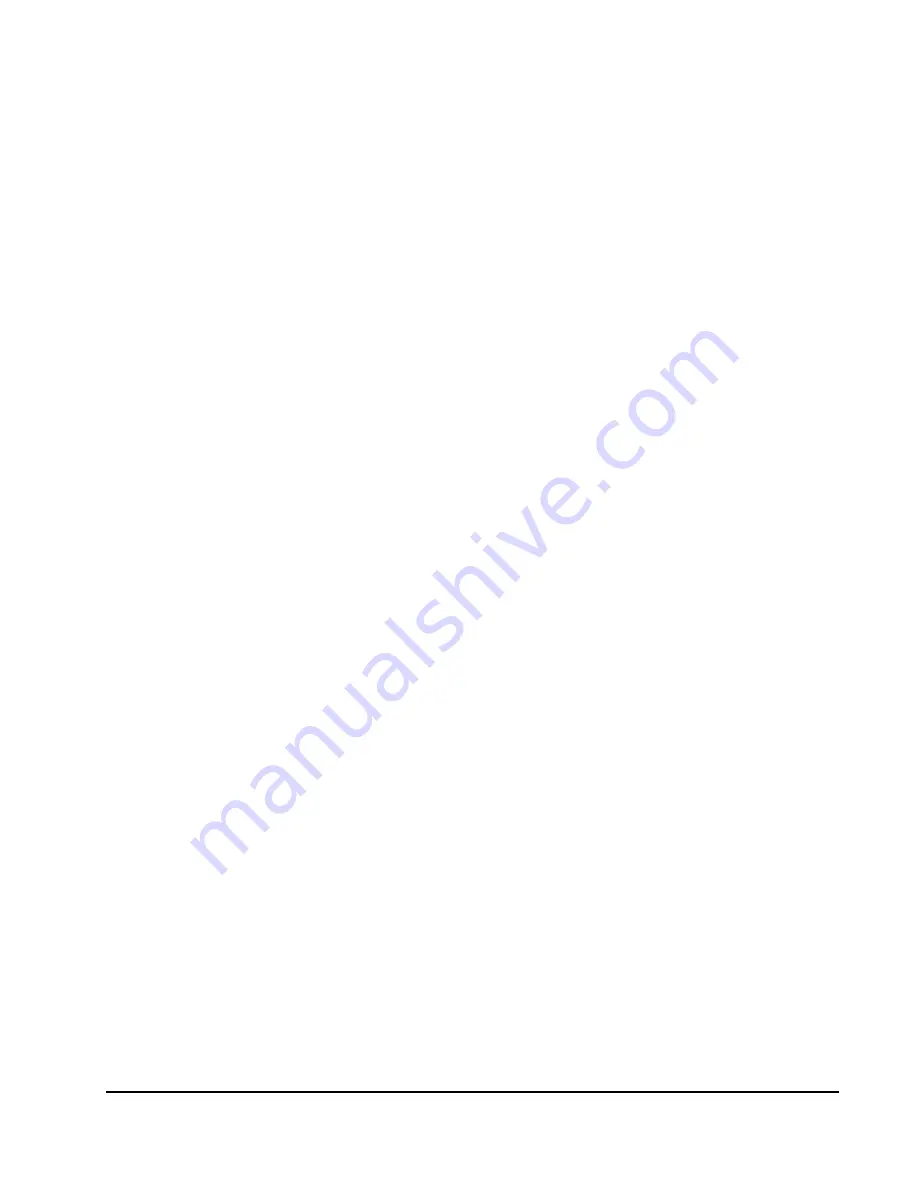
AMI Analyzer Manual
Expanded Installation Procedure
11
If the analyzer is mounted in a building with other equipment, make sure it won’t get too hot during the
summer. The sensor will rapidly die in temperatures higher than 115
º
F. You may need to install ventilation
or even air conditioning.
Remove the access panel on the left side of the analyzer so you can make the electrical connections.
2. Connect the analyzer ground to an 8 ft. ground rod (or similar high quality ground) using at least
16AWG wire.
It is
essential
for safety that the analyzer has a good ground. Normally an 8ft rod pounded into the ground
will suffice, but in very dry or sandy areas something better may have to be done. Sometimes gas running
in pipelines can develop serious static charges on the lines, causing the pipeline to be at a high voltage
compared with the local ground. Be aware of this and make sure the pipeline is well grounded itself.
3. Confirm sample pressure is less than the analyzer specification (150psig). If it is higher, use a
suitable regulator such as the high pressure AMI Liquid Rejection Probe. Such a regulator must
have a stainless steel diaphragm.
The analyzer needs a minimum of about 1 PSIG, and a maximum of 150psig sample pressure. If the
pressure is too low, the gas flow will be low and the response time long, and if the flow is very low the
effect of minor leaks will become significant. If the pressure is too high the analyzer will be damaged, and
you may get a hazardous situation if the sample is flammable.
The response time will depend on the length of tubing, the diameter and the flow rate of gas through it.
You can roughly calculate it by assuming that the volume of tubing – the length multiplied by its internal
area – has to be completely replaced by the gas flowing before you get a representative reading. If the
sample pressure is high, the volume is effectively increased because more gas is packed into the tubing.
AMI can provide a version of the Liquid Rejection Probe with a built-in regulator that can handle pressures
up to 1500psig.
4. Deal with any potential condensation or liquid contamination issues.
If the sample may contain condensable liquids, they must be prevented from entering the analyzer. Natural
gas, for example, often contains water in vapor or liquid form, and other liquids such as oils, glycols or
methanol. Such liquids tend to collect in dips in the sample line, and come through the line as slugs,
particularly if the line is cleaned by “pigging” it (sending a cleaning device through it, preceded by a tidal
wave of sludge). Compressors heat the gas and also cause liquids to condense, particularly when the gas
cools off, so that even apparently dry gas going into a compressor may contain liquids coming out. AMI can
provide a “Demister” and Liquid Rejection Probe” that together work to prevent problems from hot wet
gases. The demister acts to coalesce droplets and cool the gas, while the Liquid Rejection Probe stops any
liquids from getting to the analyzer. Any liquids fall back into the pipeline, thus minimizing maintenance
issues. Also, the Liquid Rejection Probe acts to prevent the problems that arise when the source of the gas
is shut off while the downstream compressor continues to run, thus pulling a vacuum on the line. Normally
this would cause air to be drawn into the line through the analyzer vent, but the Liquid Rejection Probe
contains a very sensitive check valve that prevents this.