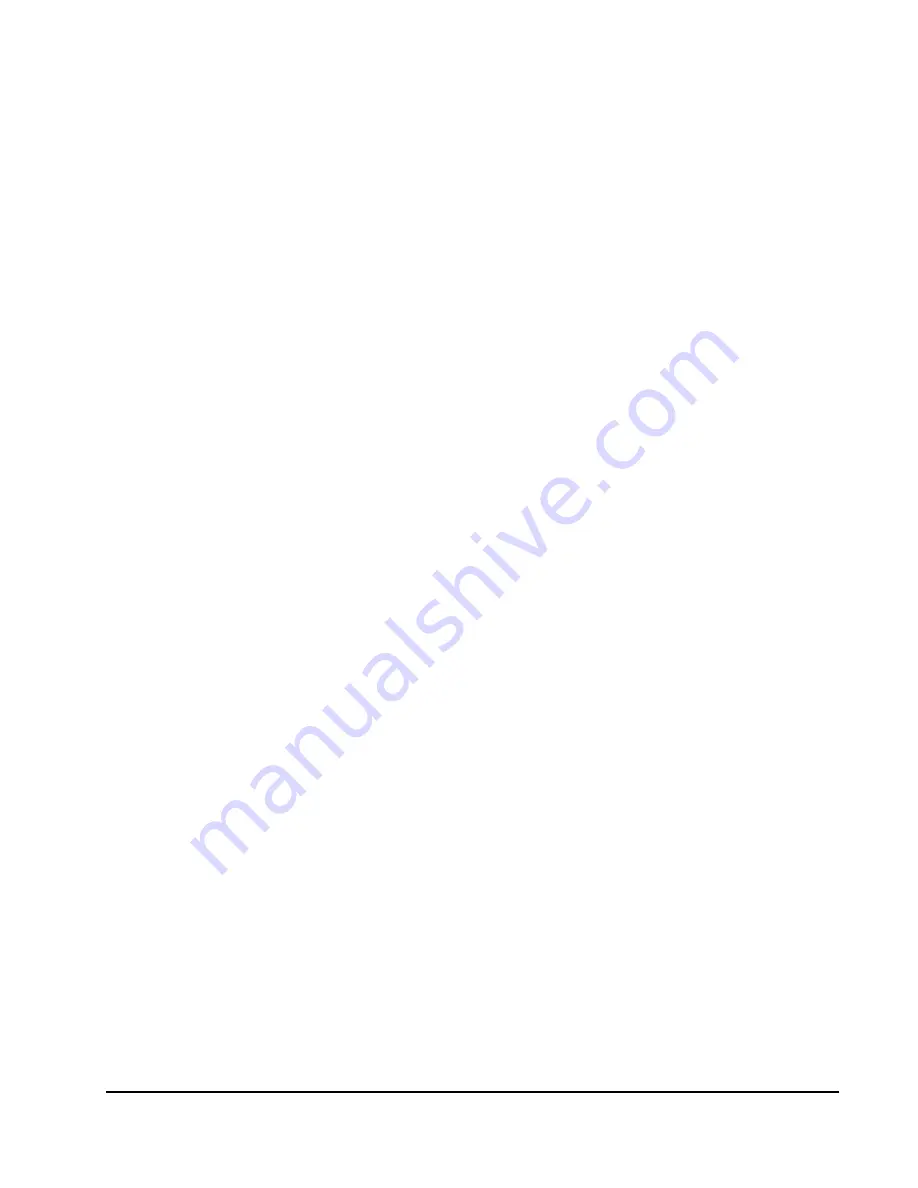
AMI Analyzer Manual
Short-form Installation Procedure
8
9. Connect vent line to outside, running slightly downhill all the way.
10. Turn the Sample/Span/Off valve to the Sample position.
11. Adjust the sample flow to approximately 1 SCFH.
12. Connect power, analog output and RS485 if desired. Run the power in one conduit, and the analog
output and RS485 in the other.
13. Power up analyzer.
14. Set up as desired with a laptop.
15. Turn the Sample/Span/Off valve to OFF.
16. Unscrew the cell cap, and install the oxygen sensor.
17. Remove the shorting tab on the sensor.
18. Optional: in the User Interface (version III) press the “NEW SENSOR” button, and record the sensor
serial number.
19. Stabilize for 45 seconds ONLY, adjust span to 20.9%.
20. IMMEDIATELY turn the Sample/Span/Off valve to SAMPLE and flow sample gas at about 1 SCFH.
21. Replace the Cell cap and tighten it down (hand tight).
22. Remove the USB connection cable.
23. Replace the access panel on the side of the analyzer.
24. Purge with sample gas for half an hour, or until the oxygen reading has fallen to low ppm levels.
25. If desired, span with known calibration gas.
Laptop set up procedure:
1. Make sure the laptop has the FTDI driver installed.
a. Windows 7 will probably find the driver by itself, but XP probably won’t.
b. Run the program called CDM20824_Setup.exe which is either in the AMI CD, or can be
downloaded from the FTDIchips.com site.
2. Install the AMI program if you haven’t done so already.
3. Run the program.
4. On the User Interface screen, at the top, click the “Port” button. Note the ports listed.
5.
Make sure the analyzer is powered up
, and connect the USB cable to it.
a.
If you connect the cable without power to the analyzer, the port won’t appear.
6. On the User Interface screen, at the top, click the “Port” button again, and you should see an
additional port. Select this port.
7. Let the program figure out how to talk to the analyzer, and watch it load up all the boxes with
numbers or words.