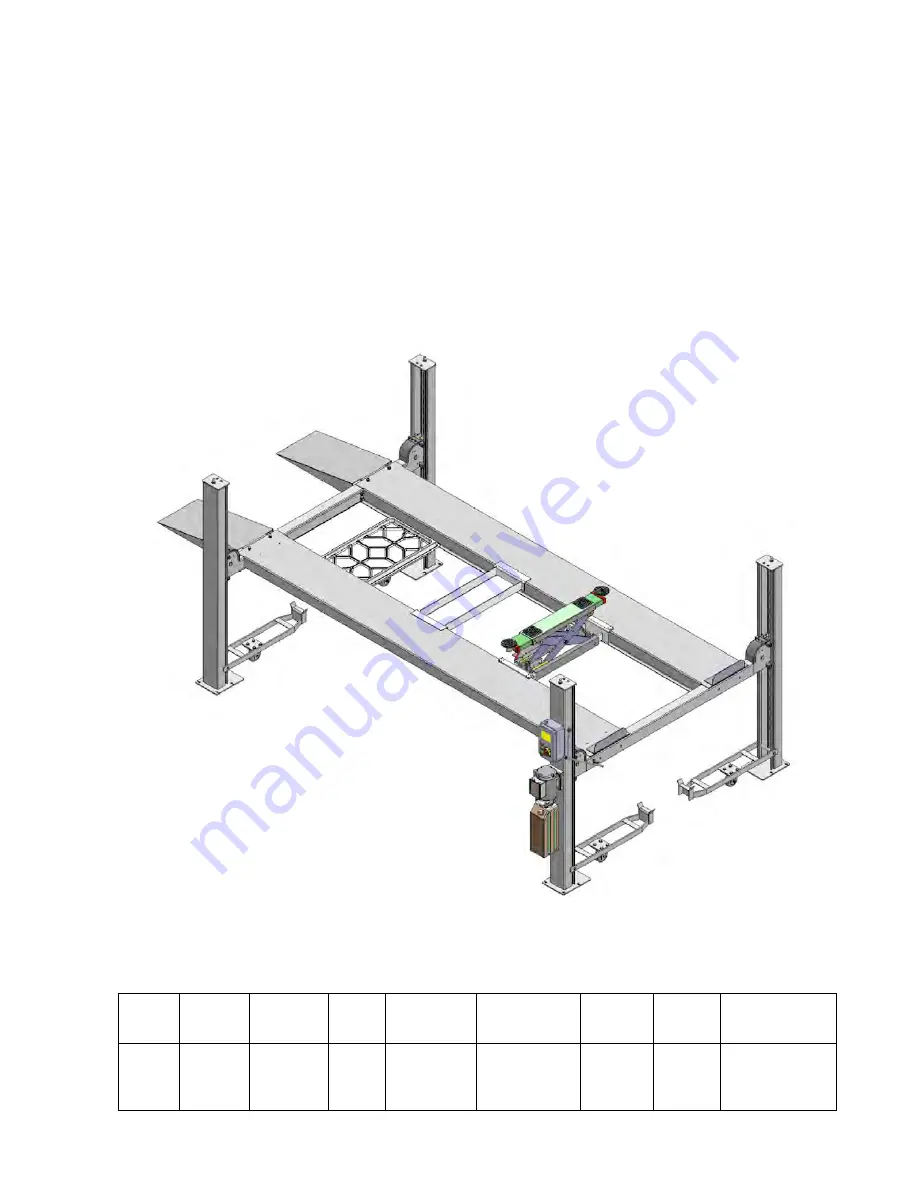
1
I. PRODUCT FEATURES AND SPECIFICATIONS
4-POST MODEL A435-P FEATURES
●
S
ingle point manual safety release.
●
Four mechanical locking devices, each equipped with both primary
and secondly safety locks.
●
Powerside column can be installed at both side, front or rear.
●
Non-skid diamond platforms and adjustable safety lock ladders.
●
Optional kits
:
Sliding jack with hand pump, caster kits
,
Jack tray, Plastic oil tray.
MODEL A435-P SPECIFICATIONS
Model
Lifting
Capacity
Lifting
Height
Lifting
Time
Overall
Length (Inc.
Ramps)
Overall Width
Width
Between
Columns
Gross
Weight
Motor
A435-P
3.5T
1864mm
(73 3/8”)
83S/
40S
5257mm
(
207”
)
2784mm
(109 1/2”)
2438mm
(96”)
820kg
110V
:
1.5HP/220V
:
2.0HP
Fig.1