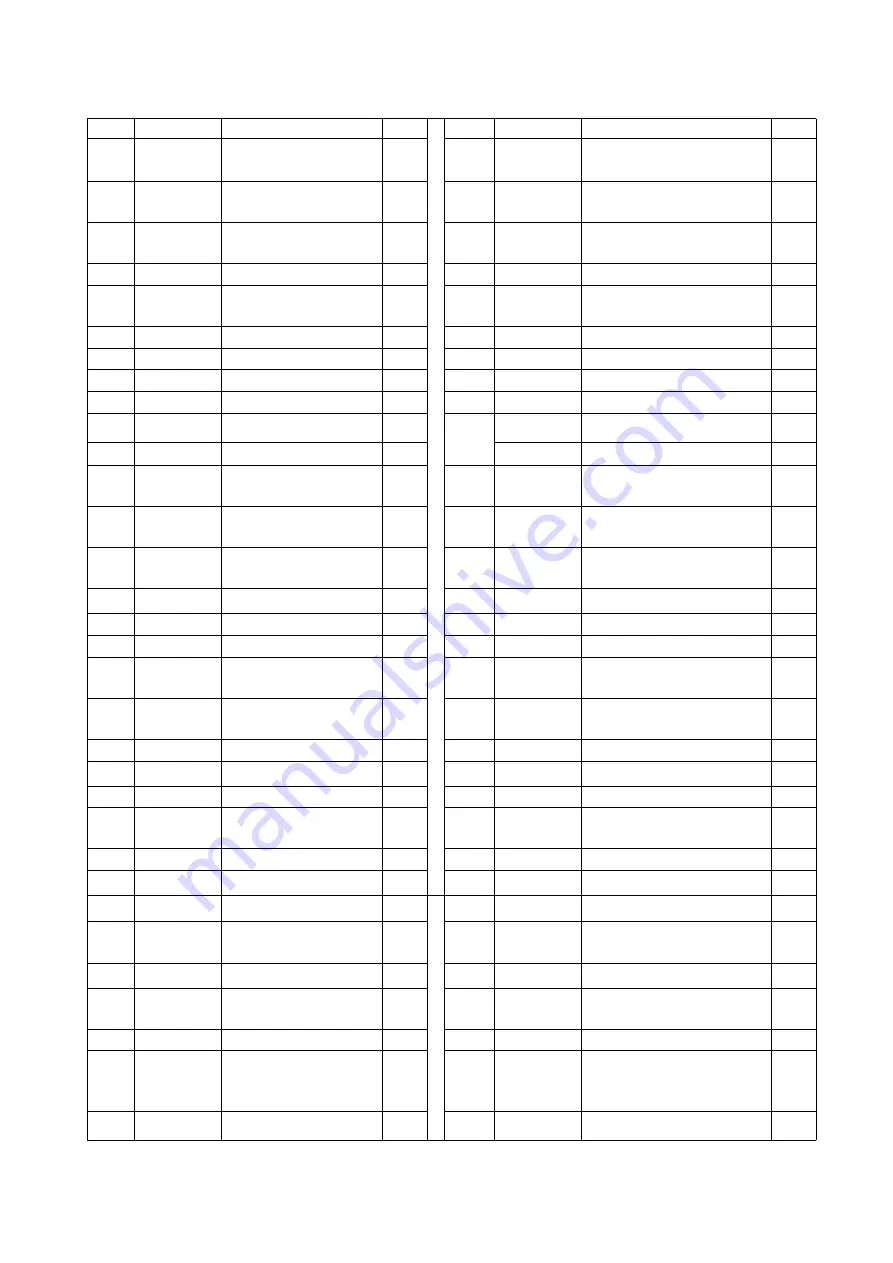
21
PARTS LIST FOR
Model BP-12
Item
Part#
Description
Qty
Item
Part#
Description
Qty
1
11207001
Protect Cover
1
40
11209052B
Stackable
Adapter(2.5
"
)
4
2
11207002
Cable Protect
Cover
2
41
11209053B
Stackable
Adapter(5
"
)
4
3
11207003
Cable Protect
Cover Assy
2
42
10206156
Tool Tray
(
short
)
2
4
11217019
Top Pulley
4
43
11206154
Toe guard (short)
4
5
10217020
Bronze Bush For
Pulley
6
44
10201140
Anchor bolt 3/4*5-1/2
12
6
10209012
Elastic Pin φ3.2
6
45
10207500A
Parts Box
1
7
10209005
Self locking Nut M8
8
46
10217069
Hex Bolt M12*30
8
8
10209033
Lock Washer φ8
10
47
10206006
Washer φ12
12
9
10209043
Hex Bolt M8*20
4
48
10206023
Self locking Nut M12
8
10
11207053
Power-side Column
1
49
10201090
Shim
(
1mm)
10
11
071101
Power Unit
1
10620065
Shim
(
2mm)
10
12
10209009
Cap Head Bolt
M6*8
12
50
11206002
Safety Block Pin
2
13
11207005
Main Safety Block
Cover
1
51
10209007A
Torsional spring
2
14
11207681
Chain pulley
support assy.
2
52
10209010
Snap Ring φ10
2
15
11207009A
Lifting carriage
2
53
10209011
Plastic Small Pulley
2
16
10207010
Cylinder φ75*870
2
54
11207019
Power-side Safety Lock
1
17
10217188
Slider Block
16
55
10206023A
Hex Nut M12
4
18
11207047
Carriage Plastic
Cover
2
56
10206003A
Handle Gun Cover
2
19
10217053
Rubber Protect
Block
2
57
11207020
Offside Safety Lock
1
20
10209019
Screw M6*16
12
58
10209056
Self locking Nut M10
3
21
11217047B
Lifting arms Pin
4
59
10420045
Lock washer φ6
14
21A
10520023
Snap Ring φ38
4
60
10209149
Spring Washer φ6
2
22
11217046C
Arm Lock bar
(Right)
2
61
10207021
Socket Bolt M6*12
1
23
10207062
Lifting Arm Assy.
4
62
11217029
Pulley Support
1
24
10217114A
Rubber Pad Assy
4
63
10206009
Plastic small Pulley
1
24A
10420138
Socket Bolt M6*16
4
64
10209046
Hex Bolt M10*35
1
24B
10420138
Rubber Pad
4
65
10207022
Cable Assy.
L=8400mm
2
24C
11680030C
Rubber Pad Frame
4
66
10209066
Cable Nut M16
8
25
10206032
Snap Ring φ25
4
67
10206065
Safety cable
Assy. L=7450mm
1
26
10206036
Elastic Pin φ6*40
4
68
10209049
Plastic black pulley
2
27
11217044
Rack
4
69
10207023
Oil hose
5/16*3210mm(straigh
t + 90°)
1
28
10217045A
Compressed spring
4
70
10209060
90° Fitting
1