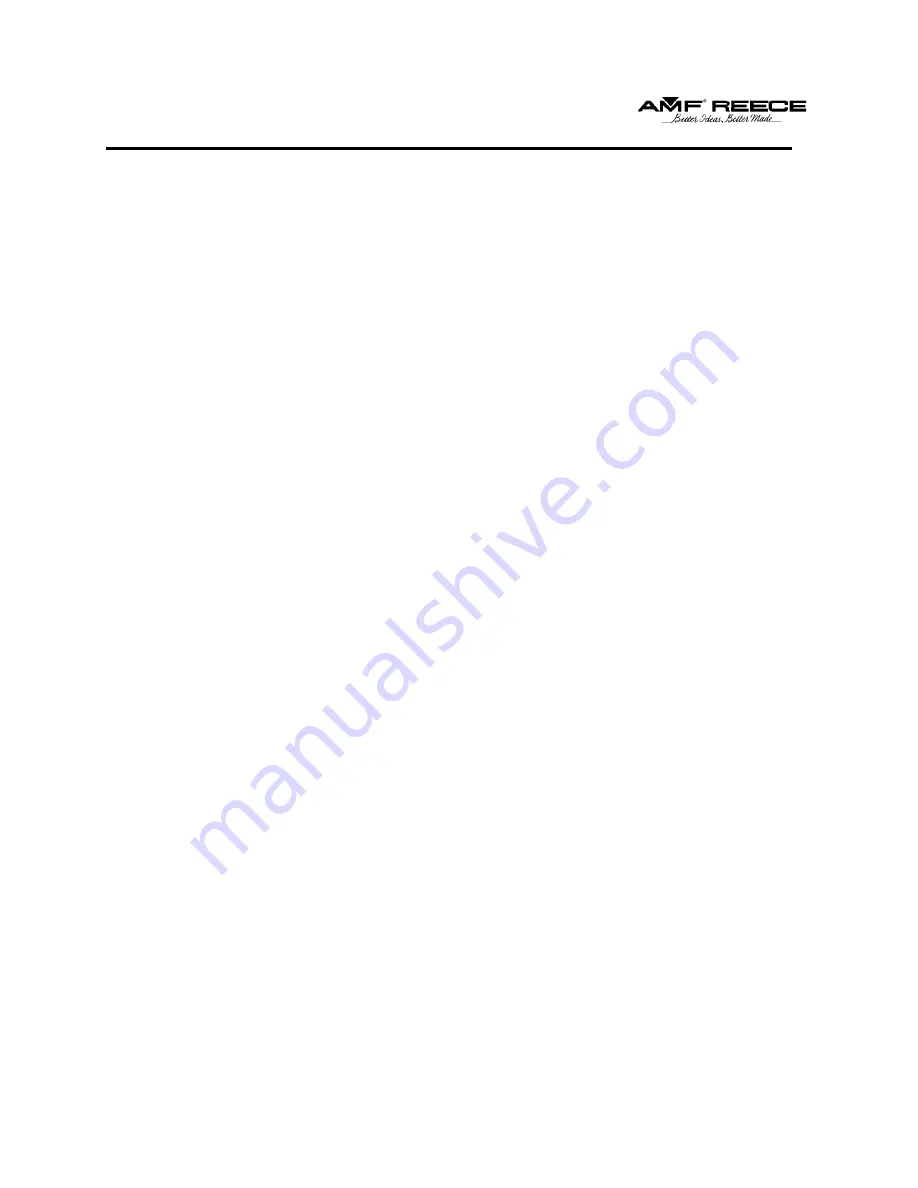
2-2
S-101
TROUBLESHOOTING
Revised 09/2004
e-mail: [email protected]; [email protected]; website: www.amfreece.com
Phones: +420 582 309 146 (Service), +420 582 309 286 (Spare Parts); Fax: +420 360 606
The headings indicate the type of trouble. Below them will be found the probable cause for the trouble and
its remedy. Machine failure as indicated by the heading can be traced to one or more of the causes beneath
it.
1. MACHINE FAILS TO START:
A) See that the Belts are on properly and power
is applied.
B) If Belts and Pulleys leading from Transmitter
are not turning over, but the Center Pulley
of the Transmitter is, there may be slipping
in the Clutch. Adjust two Screws 01.2065
on Clutch Shoe 02.0526.0.050 inward
an equal amount.
C) If the Belts are turning and Left Wheel Dog
10.3042.2 will not engage Striker 10.3038.1
on Crank. Spring on Shifting Lever 10.3029.1
may be weak off or broken. REPLACE.
D) Lock Nuts 10.3041 on Left Hand Wheel
may have loosened. Screw in and adjust so
that Dog 10.3038 has no side play and works
freely.
E) Striker 10.3038 may be broken. REPLACE
F) Clamp Screw 01.2035 on Shifter Spool
10.3045 may be loose. Adjust and tighten
according to instructions under machine
adjustments, Sheet 18, Figure 4-5.
2. MACHINE STARTED, RAN A
SHORT DISTANCE AND STOPPED:
A) It would be advisable to first check all items
under No. 1.
B) Left Hand Wheel Belt too loose. TIGHTEN.
C) On Cut Before machines, the pressure on the
Cutting Lever is too great. Adjust according
to instructions on Sheet 14, Figure 3.
D) The line-up may be out of adjustment. Follow
instructions on Sheet 3, Figure 2-3.
E) Rocker Arm may be out of adjustment. Follow
instructions on Sheet 16, Fig. 5-6, Sheet
17, Figure 1a, 2a, 3a and Sheet 18, Figure
4-5.
F) Spring 01.5450 on Clutch 10.1089 may be
broken. REPLACE.
G) Pin in Drive Cam 10.1095.3 may be broken.
REPLACE Drive Cam 10.1095.3
H) Sector teeth may be clogged with dirt. Take
out Stud 10.3026 and test by rotating the
whole assembly back and forth.
3. MACHINE STUCK TIGHT
THROUGH INTERFERENCE
A) Separate the stitching mechanism from the
feeding mechanism by removing Shoulder
Screw 01.1132. If the interference is in the
stitching mechanism the Stop Wheel
10.1088.0.050 on the right hand side will not
turn after it is unlocked. Trace for the
cause in the stitching mechanism by taking
out Screw 10.3008, which disconnects
Looper Drag Link 10.1067 from Looper
Rocker 10.3006.0.165 or 10.3006.0.200.
This will definitely place where the sticking
occurs, either in the race assembly or in
the Head.
B) If the Stop Wheel 10.1088.0.050 does turn
after the Shoulder Screw 10.1111 is removed,
crank the machine with the Left Hand Handle
and, if it still will not move, eliminate
the probable possibilities for the sticking
by disconnecting the units depending on
movement from the Main Cam. If the Main
Cam will not move after working the Handle
back and forth, it will be necessary to take
out the Main Cam to remove the interference:
unless, it may be removed through one
of the various openings in the Cam Case.