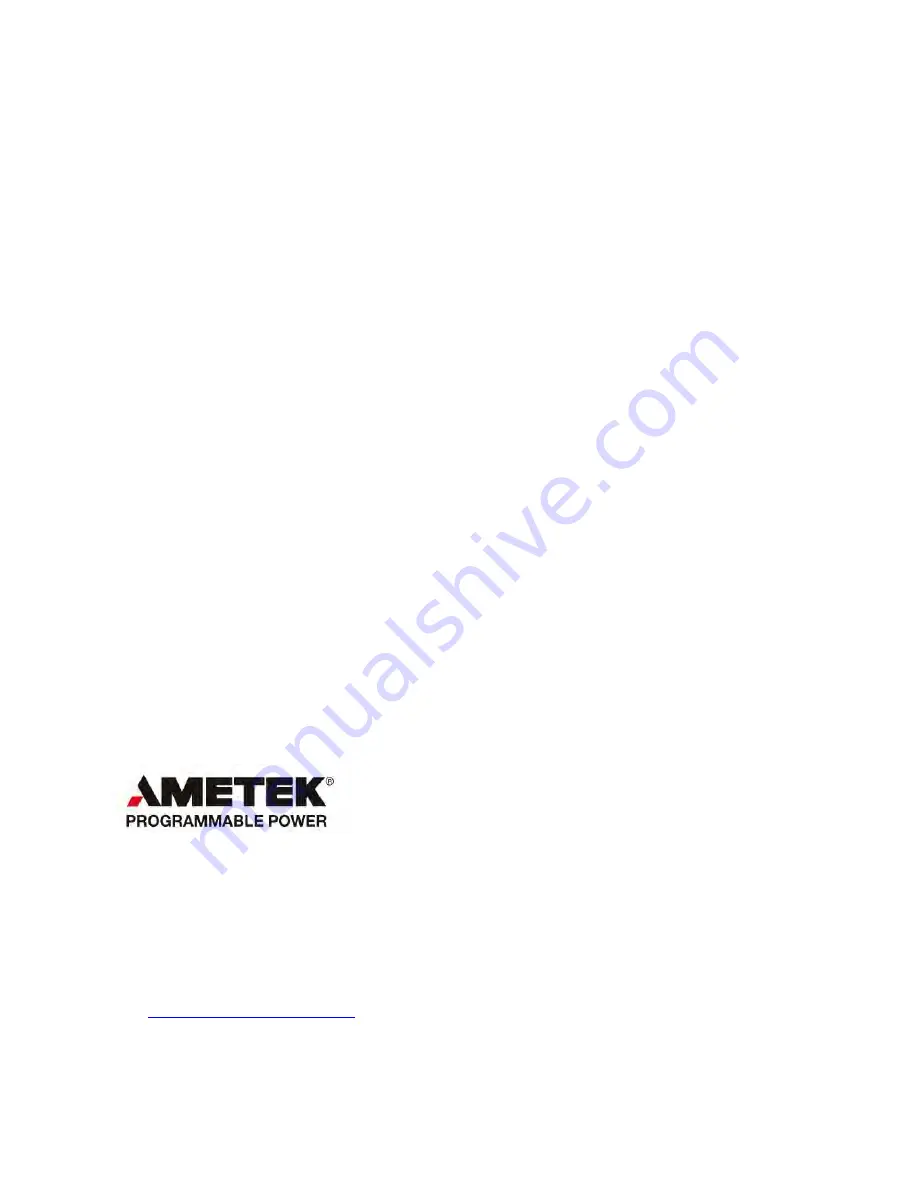
Contact Information
Telephone: 800 733 5427 (toll free in North America)
858 450 0085 (direct)
Fax: 858 458 0267
Email:
Domestic Sales: [email protected]
International Sales: [email protected]
Customer Service:
.
SmartWave™
Switching
Amplifier
Operation Manual
March 2011
Document No. M161924-01 Rev D
This manual covers models:
SW5550A
SW3700A
SW1850A