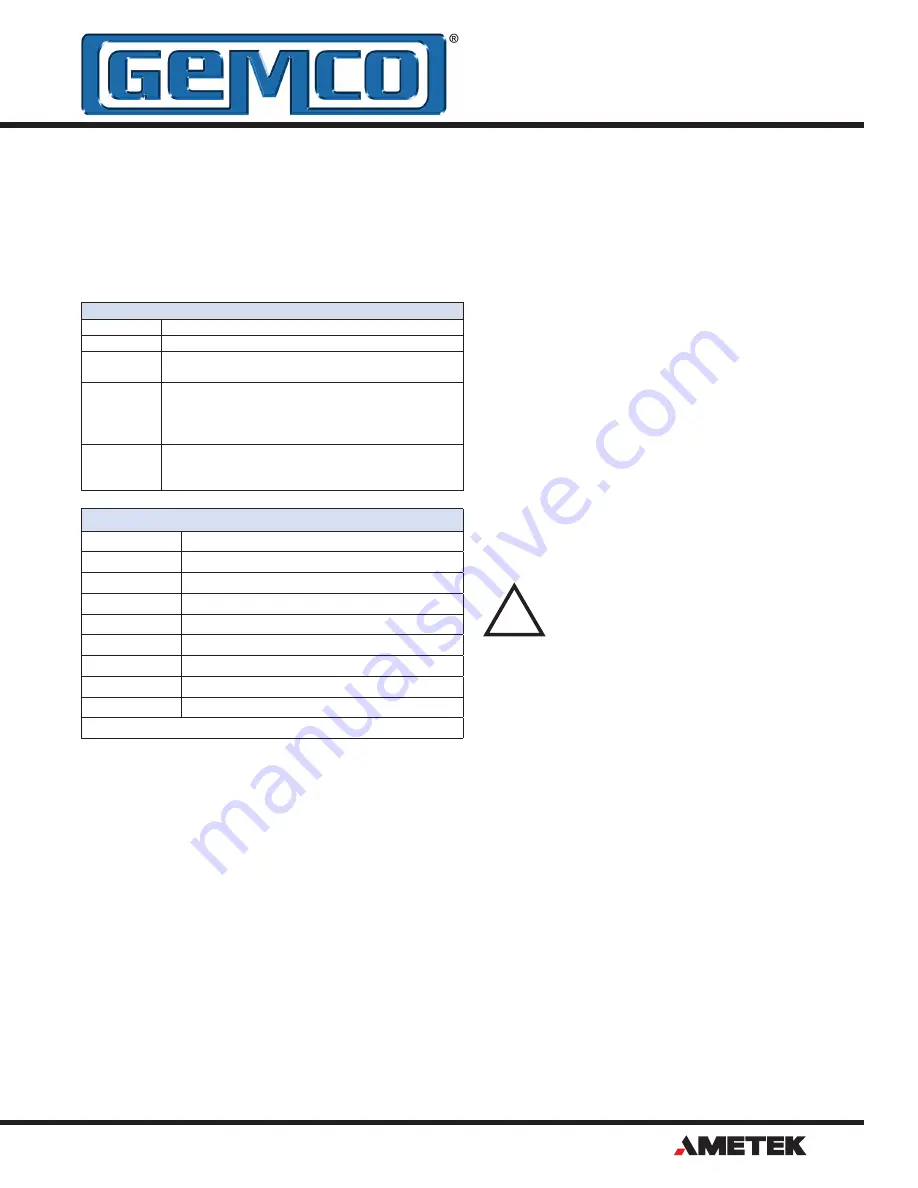
13
1080 N. Crooks Road • Clawson, MI 48017 • 800.635.0289 • Phone 248.435.0700 • Fax 248.435.8120 • www.ametekapt.com
AUTOMATION & PROCESS TECHNOLOGIES
®
Before programming the Zero or Span, the program
input must be connected to the Power Supply
Common for a minimum of 2 seconds and no more
than 6 seconds, then released for 1 second. The
LTD programming sequence is now unlocked and
will remain an unlocked unit until either the Zero or
Span is programmed or the 10 second programming
sequence times out. During the unlock mode either
the Zero or Span can be programmed by momentarily
connecting the Program Input to either the Power
Supply Common or Power .
NOTE:
The LDT must be unlocked to program the
Zero and unlocked again to program the Span. Once
either the Zero or Span is programmed the LDT will go
back into the locked mode.
To program the Zero or Span, the program input must
be connected to the Power Supply Common for 4
seconds, then released for 1 second. Within the next 5
seconds, you can program either the Zero or the Span
by momentarily connecting the Program Input to either
the Power Supply Common or Power VDC.
WARNING: During normal operation,
electrically insulate the White
Program wire to prevent accidental
setting of Span.
Manual Setting of Zero & Span
To set the Zero and Span position, follow these steps:
1. Apply power to the LDT.
2. Place magnet assembly where Zero is to be
located, but within the active region of the probe.
3. Short the Program Input pin to the Power Supply
Common for 4 seconds. Remove the short for 1
second. Within 5 seconds, short the Programming
Input pin to the Power Supply Common. This
completes the Zero programming process.
4. Place magnet assembly where Span is to be
located, but within the active region of the probe.
5. Short the Program Input pin to the Power Supply
Common for 4 seconds. Remove the short for 1
second. Within 5 seconds, short the Programming
Input pin to the Power VDC.
This completes the programming process.
!
3.3: Features
Automatic Gain Control
The Automatic Gain Control feature will automatically
search and find the magnet on power up, if power is
applied without a magnet on the LDT, the LED will turn
RED indicating no magnet signal is detected. Turn
power off and place magnet within the active stroke
area. Re-apply power.
Diagnostic LED
LED Color Description
None
No power to LDT
Green
Magnet signal detected and within programmed
range.
Yellow
Magnet signal detected, but magnet is outside of
programmed range.
NOTE
: Magnet can be programmed in this range
if desired.
Red
No magnet signal detected. Make sure magnet
is on the rod and within the active area. Move
magnet back into the range and cycle power.
Accessories
P/N
Description
949011L6
6 Foot, 5 Pin, Straight, 12mm, Euro Connector
949012L6
6 Foot, 5 Pin, Right Angle, 12mm, Euro Connector
SD0439700LXX 10 Pin, Straight Connector, 6 Foot Standard
SD0439700LXX 10 Pin, Right Angle Connector, 6 Foot Standard
SD0553200LXX MTS-6 Pin, "M" Option, (Voltage or Current Outputs)
SD0553300LXX Balluff-8 Pin, "B" Option, (Voltage Outputs Only)
SD0553400LXX Balluff-8 Pin, "B" Option, (Current Outputs Only)
SD0400800 Standard 4 Hole Magnet
Consult factory for complete accessory offerings.
3.4: Setting Zero & Span Position
The units come fully programmed from the factory and
do not require re-programming unless desired. The
units are 100% absolute and will not lose programmed
parameters on power loss. The Zero and Span points
can be programmed in any order and anywhere within
the LDT's active sensor area.
NOTE 1:
Zero or Span can be adjusted individually
without setting the other.
NOTE 2:
Zero = 0V on 0-10 VDC units and 4mA
on 4-20mA units.
There is a timing sequence that is used to unlock the
probe for programming. This is to insure that the Span
cannot be accidentally re-programmed by someone in
the field.