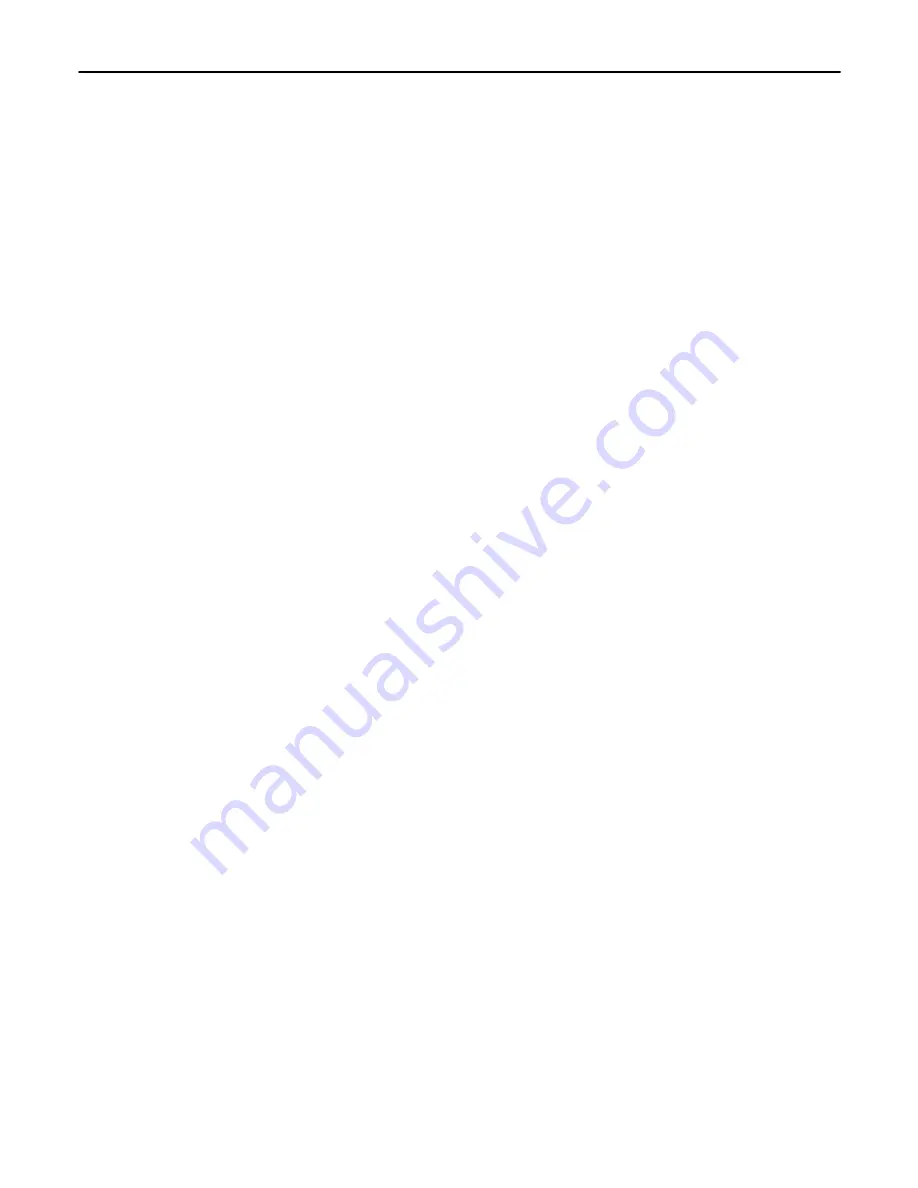
3-2 SECTION 3 – MAINTENANCE AND SERVICING
The regulator is readily disassembled from the front panel. All disassembly can be done
WITHOUT removing the regulator from the instrument.
Major Disassembly
1.
Ensure all pressure is released from the instrument.
2.
Rotate the regulator knob (Item 159) fully counterclockwise to remove tension from the
regulator assembly.
3.
Remove the hole plug (Item 155) from the regulator knob using the narrow (5/16” wide
screwdriver) to pry the hole plug free.
4.
Unscrew the nut (Item 153) from inside the regulator knob cavity using the 1/2” socket
wrench.
5.
Unscrew the bonnet (Item 151) using the 1-3/4” open end wrench. The bonnet will come
off as an assembly: Bonnet (Item 151), adjusting screw (Item 160), collar (Item 002),
limit screw (Item 158) and load spring (Item 006).
6.
Items 161 and 162 do not exist in the stainless steel design. The bonnet (Item 151) is a
closed end component as shown in detail (A).
7.
Remove the sensor assembly from the body (Item 001) using the needle nose pliers to grip
and pull the sensor from the regulator body. A rocking motion may be required to free the
sensor assembly.
8.
Unscrew the seat retainer (Item 004) from the body Item (001) and remove the seat (Item
003).
9.
Clean the seat retainer.
10.
Replace the seat (Item 003). Place the beveled (chamfered) side of the seat facing out
toward the sensor assembly stem. eg., The seat should have the chamfer facing into the
seat retainer thus the chamfer will face out when retained in the regulator body.
11.
Install the seat retainer with the seat back into the body. Use a small amount of anti-seize
lubricant on the seat retainer threads.
Bonnet Disassembly/Reassembly
1.
Remove the limit screw (Item 158) from the spring cap (Item 002)
2.
Remove all components from the bonnet.
3.
Clean and lubricate the bearing using a suitable lubricant.
4.
Clean the spring cap and adjusting screw threads. Place a small amount of anti-seize
lubricant on the threads.
5.
Clean the spring
6.
Reassemble the bonnet components. Install the limit screw.
7.
Set the bonnet assembly aside for later installation.
Sensor Disassembly / Reassembly
1.
Unscrew the spring pad (Item 105) from the sensor (Item 102) using the ½” open end
wrench and the large ½” wide screwdriver. You may wish to clamp the spring pad in a
vise to perform this step.
Caution: Small parts are present within the sensor assembly. Take care not to
lose the parts.
2.
Pull the spring pad away from the sensor. Retain the spacer (Item 106) for later use.
Summary of Contents for CHANDLER ENGINEERING Twin UCA 4262
Page 6: ...P 2 PREFACE This page is intentionally left blank...
Page 10: ...1 4 SECTION 1 INSTALLATION This page is intentionally left blank...
Page 20: ...2 10 SECTION 2 OPERATING INSTRUCTIONS This page is intentionally left blank...
Page 24: ...3 4 SECTION 3 MAINTENANCE AND SERVICING This page is intentionally left blank...
Page 28: ...4 4 SECTION 4 TROUBLESHOOTING GUIDE This page is intentionally left blank...
Page 32: ......
Page 33: ...CHANDLER ENGINEERING...
Page 34: ......
Page 37: ......
Page 38: ...CHANDLER ENGINEERING...
Page 39: ......
Page 40: ...CHANDLER ENGINEERING...