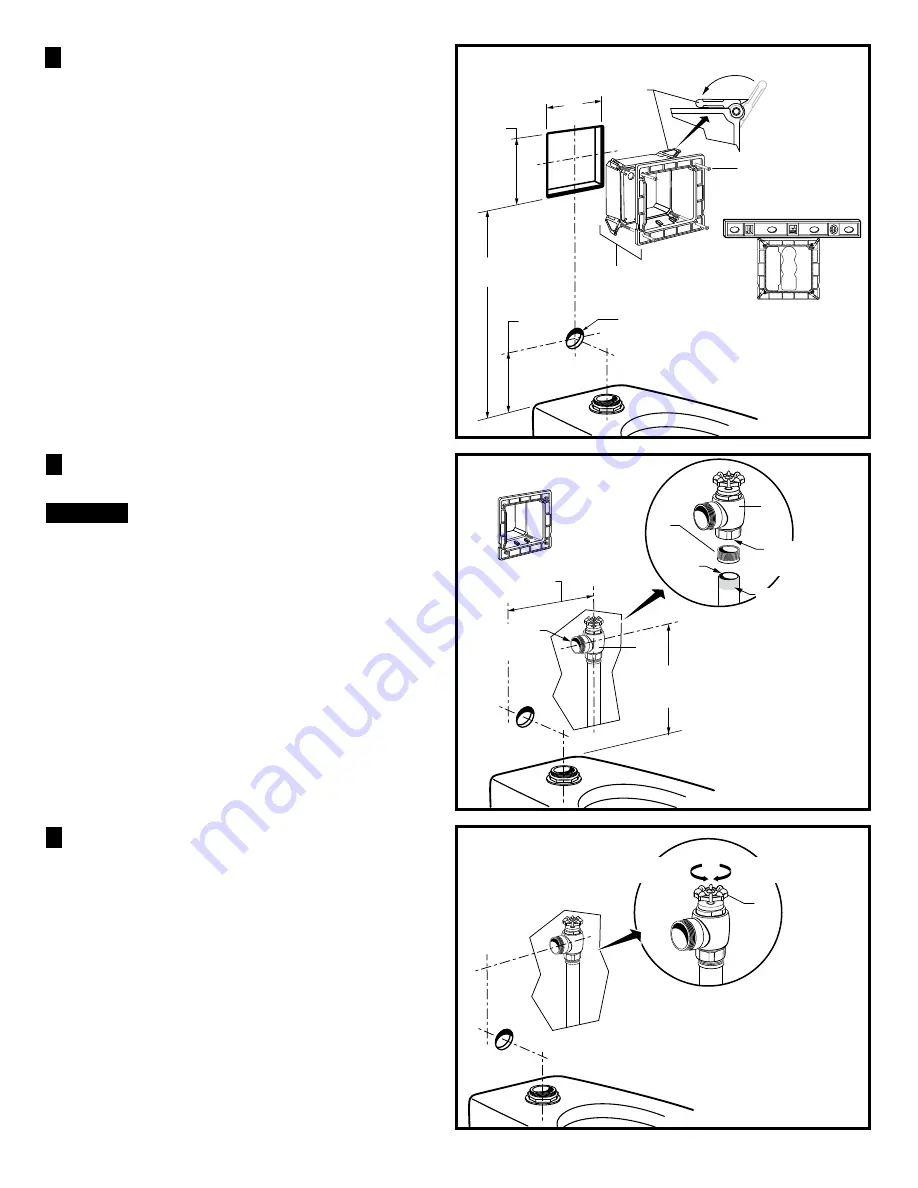
Fig. 4
Fig. 3a
Fig. 5
3
INSTALL ELECTRICAL BOX
ASSEMBLY; Fig. 3
1.
Cut a 127x127mm (5"x 5") opening in finished wall for
ELECTRICAL BOX
(1)
at the deminsion shown in
Fig.3.
2.
Rotate the 4 MOUNTING TABS
(2)
flat against the
electrical box. Holding the MOUNTING TABS
(2)
in
position install the ELECTRICAL BOX
(1)
into the opening.
Make sure the MOUNTING TABS
(2)
are behind the wall.
3.
Tighten the the 4 MOUNTING SCREWS
(3)
until the
ELECTRICAL BOX
(1)
is almost secure in the wall.
Before tighting fully rest a level at the top edge of the
ELECTRICAL BOX
(1)
and make sure the box is level,
then tighten fully.
Fig. 3a.
4.
*Cut a 2" hole for supply to fixture at deminsion shown.
1
Fig.3 (TOP SPUD FIXTURE ILLUSTRATED)
1
3
2
2
1
1
1.
Open SUPPLY STOP
(1)
.
3.
Turn on water supply to flush line of any debris or
sediment.
4.
Close SUPPLY STOP
(1)
and turn off water supply line.
FLUSH OUT SUPPLY LINES; Fig. 5
3
*FOR HOLE LOCATION OF
SUPPLY ON BACK INLET
FIXTURES, REFER TO FIXTURE
BEING INSTALLED FOR CORRECT
HEIGHT FROM FINISHED FLOOR
127mm
(5)
406mm
(16 REF.)
127mm
(5)
INSTALL SWEAT SOLDER
ADAPTER; Fig. 4
CAUTION
Turn water supplies off
before beginning
Note:
Control stop inlet is 1" IPS. For optional sweat
connection,
install Sweat Solder Adapter
(1)
(Supplied)
for 1
"
copper pipe supply line.
Fig. 4.
1.
Clean the end of the supply pipe. Push the threaded
ADAPTER
(1)
on until it is seated against the internal
stop. Sweat the ADAPTER
(1)
to the pipe.
2.
From behind the wall install the CONTROL STOP
(2)
to the water supply line with the outlet positioned as
required.
3.
Support piping as required.
2
T O P
FILE
EDGES
CLEAN & SOLDER
TO ADAPTER
(1)
115mm-134mm
(4-1/2 TO 5-1/4)
CONTROL STOP
DN 25mm
(1" I.P.S.)
CONTROL
STOP
OUTLET
CLOCKWISE
CLOSES
CONTROL STOP
COUNTER-CLOCKWISE
OPENS CONTROL STOP
T O P
T O P
2
403 TO 441mm
(15-7/8 MIN. TO
17-3/8 MAX.)
127mm
(5 MAX.)
M968550 REV. 1.5