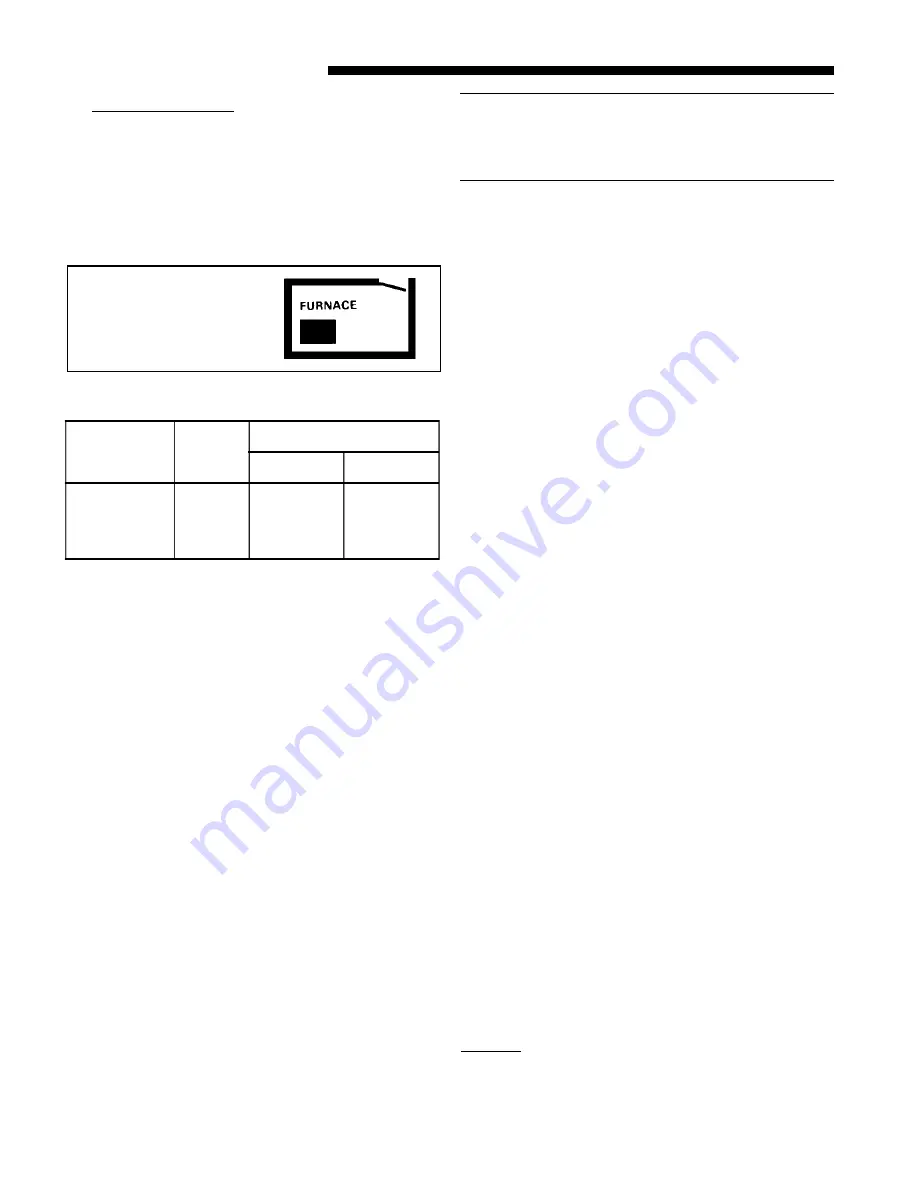
10
18-CD24D1-2
Installer’s Guide
DUCT CONNECTIONS
Air duct systems should be installed in accordance with
standards for air conditioning systems, National Fire
Protection Association Pamphlet No. 90. They should
be sized in accordance with ACCA Manual D or which-
ever is applicable.
Central Furnaces, when used in connection with cooling
units, shall be installed in parallel or on the upstream
side of the cooling coil to avoid condensation in the heat
exchanger. With a parallel flow arrangement, the damp-
ers or other means used to control flow of air shall be ad-
equate to prevent chilled air from entering the Furnace,
and if manually operated, must be equipped with means
to prevent operation of either unit unless the damper is
in full heat or cool position.
On any job, flexible connections of nonflammable material
may be used for return air and discharge connections to
prevent transmission of vibration. Though these units
have been specifically designed for quiet, vibration free op-
eration, air ducts can act as sounding boards and could, if
poorly installed, result in vibration to the annoyance
level.
When the Furnace is located in a utility room adjacent
to the living area, the system should be carefully de-
signed with returns to minimize noise transmission
through the return air grille. Although these Furnaces
are designed with large blowers operating at moderate
speeds, any blower moving a high volume of air will
produce audible noise which could be objectionable
when the unit is located very close to a living area. It is
often advisable to route the return air ducts under the
floor or through the attic. Such design permits the in-
stallation of air return remote from the living area (i.e.
central hall).
When the Furnace is installed so that the supply ducts
carry air circulated by the Furnace to areas outside the
space containing the Furnace, the return air shall also
be handled by a duct(s) sealed to the Furnace and termi-
nating outside the space containing the Furnace.
Where there is no complete return duct system,
the return connection must be run full size from
the Furnace to a location outside the utility
room, basement, attic, or crawl space.
Do NOT
install return air through the back of the Fur-
nace cabinet.
Confined spaces are installations with less than 50 cu.
ft. of space per 1000 BTU/ hr input from all equipment
installed. Confined space is defined in Figure 9. Air for
combustion and ventilation requirements can be sup-
plied from inside the building as in Figure 10 or from
the outdoors, as in Figure 11.
3. The following types of installations will
require
use
of OUTDOOR AIR for combustion, due to chemical
exposures:
* Commercial buildings
* Buildings with indoor pools
* Furnaces installed in commercial laundry rooms
* Furnaces installed in hobby or craft rooms
* Furnaces installed near chemical storage areas.
Exposure to the following substances in the com-
bustion air supply will also require OUTDOOR
AIR for combustion:
* Permanent wave solutions
* Chlorinated waxes and cleaners
* Chlorine based swimming pool chemicals
* Water softening chemicals
* Deicing salts or chemicals
* Carbon Tetrachloride
* Halogen type refrigerants
* Cleaning solvents (such as perchloroethylene)
* Printing inks, paint removers, varnish, etc.
* Hydrochloric acid
* Cements and glues
* Antistatic fabric softeners for clothes dryers
* Masonry acid washing materials
TABLE 3
MINIMUM FREE AREA IN SQUARE INCHES
EACH OPENING (FURNACE ONLY)
Furnace
Maximum
BTUH/INPUT
Rating
Air
From
Inside
Air From Outside
Vertical
Duct
Horizontal
Duct
60,000
80,000
100,000
120,000
140,000
100
100
100
120
140
15
20
25
30
35
30
40
50
60
70
2. All air from outdoors as in Figure 11: The confined
space shall be provided with two permanent open-
ings, one commencing within 12 inches of the top
and one commencing within 12 inches of the bot-
tom of the enclosure.
The openings shall communicate directly, or by
ducts, with the outdoors or spaces (crawl or attic)
that freely communicate with the outdoors. Refer
to Table 3, for minimum open areas required.
CONFINED
LESS THAN 50 CU. FT.
PER 1000 BTU/HR. INPUT
ALL EQUIP INSTALLED
Figure 9
NOTE: Extended warranties are NOT available in some
instances. Extended warranty does NOT cover repairs
to equipment installed in establishments with corro-
sive atmospheres, including but limited to, dry clean-
ers, beauty shops, and printing facilities.