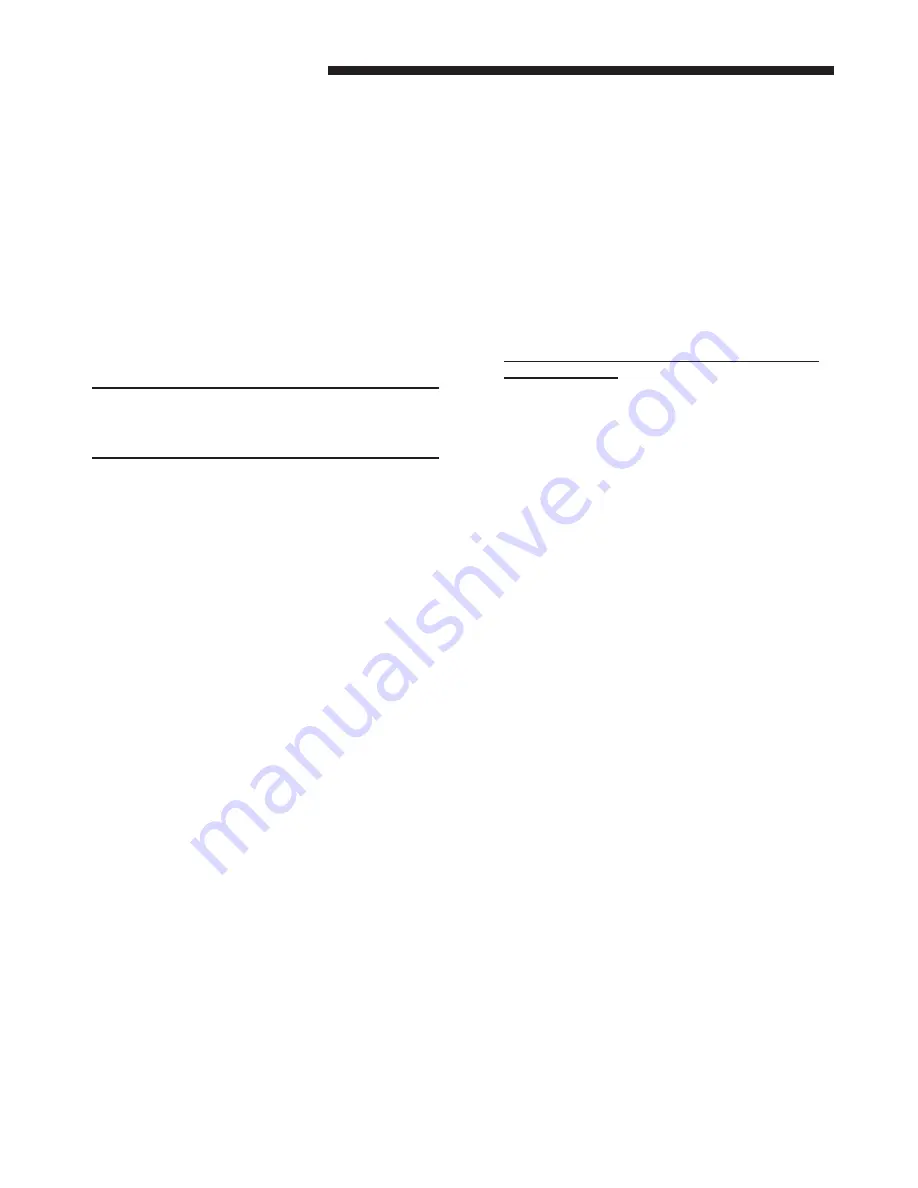
4
18-GE08D1-2
Installer’s Guide
e. Pedestal and unit should be isolated from the
foundation using a suitable isolating material.
DOWNFLOW
a.
For maximum efficiency
, the horizontal drip
tray should be removed. Tray removal requires
that the coil be removed by sliding the coil out on
the coil channel supports. The tray is detached
by removing the two screws at the drain pan
and the two screws holding the two brackets at
the top of the coil.
b. Remove the factory installed baffle assembly
from the apex of the coil by removing the 5/16"
hex head screws.
Replace this baffle with the factory supplied
narrow coil baffle using the screws removed
previously (See Figure 3).
NOTE:
INSTALLATION OF THE DOWNFLOW BAFFLE KIT
INCLUDED WITH UNIT IS REQUIRED ON
DOWNFLOW APPLICATIONS. SEE FIGURE 4.
c. Detach the coil from the drain pan by removing
4 screws as shown in Figure 4.
d. Remove the front triangular baffle from the coil and
install the 1/2" wide gasket provided per Figure 4.
Trim the gasket length to fit the baffle. Reinstall
the baffle to coil, with gasket material compressed
against the coil.
e. Install the water blow-off baffles provided on each
side of the coil with the flange at the top as shown
in Figure 4. The bottom of the baffle is to be as
close to the bottom of the coil as possible.
f. Install the 7/8" wide gasket in each side of the
drain pan as shown in Figure 4 (sect. X-X).
g. Place the 2 water diverter baffles (
5 ton model
only
) underneath the coil on the inside edge of
the drain pan, Figure 4. Fill the bend in the
baffle which fits the inner edge of the drain pan
with RTV type adhesive/sealant before install-
ing the baffle.
h. The unit is then placed with the blower side
down and the coil is replaced on the coil channel
supports with the drain connections at the
bottom. The unit is now in downflow position
with front access.
i. When air handler with supplementary heater is
to be installed in the downflow position on
combustible flooring an accessory subbase
(TAYBASE101 for 2TEC3F18A-36A,TAYBASE101
for 2TEC3F18A and TAYBASE100 for
2TEC3F42A-60A) must be used. See Figure 1.
HORIZONTAL LEFT
a.
For maximum efficiency
and Customer ease of
filter maintenance, it is recommended that a
properly sized
remote filter
and grille be installed
for horizontal applications. Airflow should not
exceed the face velocity of the filter being used.
The
factory installed filter should then be
removed from the unit
.
b. To convert the unit to horizontal left, front access,
slide the coil out on the coil channel supports and
rotate the complete coil 180 degrees.
c. Remove the factory installed baffle assembly
from the apex of the coil by removing the 5/16"
hex head screws. Replace this baffle with the
factory supplied narrow coil baffle using the
screws removed previously (See Figure 3).
d. The coil is then inserted back into the cabinet on
the opposite side coil channel supports. The unit is
now horizontal left with front access.
e.
Openings where field wiring enters the
cabinet must be completely sealed.
Location of
power entry is shown on the Outline Drawing.
f.
Cage nuts are not provided for horizontal
left suspension.
However, if the unit is sus-
pended, it
must be supported from the
bottom near both ends as well as the middle to
prevent sagging. The service access must remain
unobstructed.
If the unit is not suspended it must be supported
as mentioned above and isolated carefully to
prevent sound transmission. Vibration isolators
(purchased locally) must be placed under the unit.
g. It is always recommended that an auxiliary drain
pan be installed under a horizontal air handler (See
Condensate Piping) to prevent possible damage to
ceilings.
h. Isolate the auxiliary drain pan from the unit or
from the structure.
i. Connect the auxiliary drain pan to a separate
drain line (no trap is needed in this line) or route
outside the structure to a conspicuous location in
accordance with national and local codes.
HORIZONTAL RIGHT
a.
For maximum efficiency
and Customer ease of
filter maintenance, it is recommended that a
properly sized
remote filter
grille be installed for
horizontal applications. Airflow should not exceed
the face velocity of the filter being used.
The
factory installed filter should then be re-
moved from the unit.
b. Unit is shipped from the factory in the upflow or
horizontal right configuration. Unit conversion is
not required.
c. The air handler is designed to be suspended by
using the cage nuts provided in the unit. Six 1/4"
– 20 threaded rods are required for the
2TEC3F18-42A models and Eight threaded rods
are required for the 2TEC3F48-60A models.
Other means of suspension are allowed as long
as the unit is supported from both ends as well as
the middle to prevent sagging and service access
is not obstructed.
d. If the unit is not suspended it must be isolated
carefully to prevent sound transmission. Vibration
isolators (purchased locally) must be placed
under the unit.