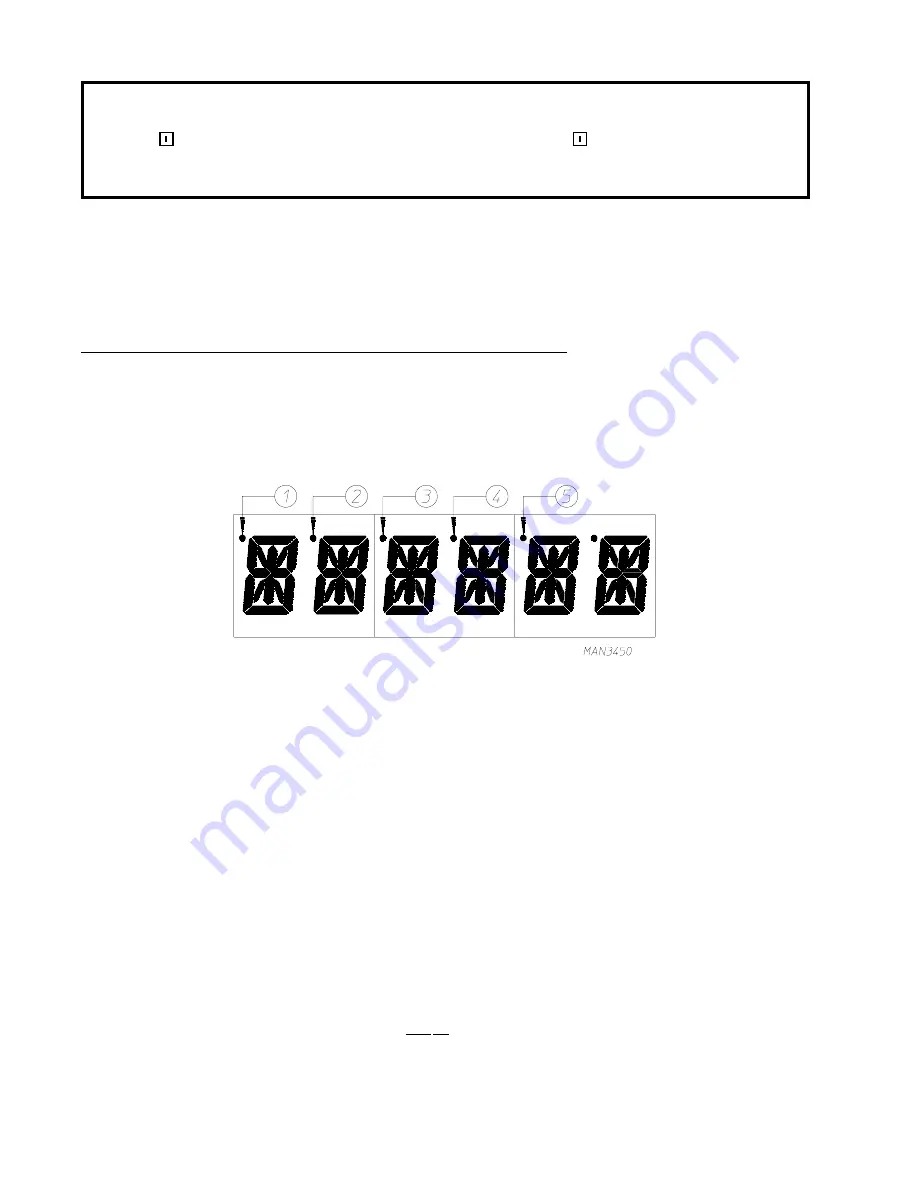
44
NOTE: RPM
- This routine monitors the timing response from the existing rotational sensor input and
derives a RPM measurement. To display this RPM measurement (press the ENTER/START
Key once and release, then press the ENTER/START Key a second time and hold
...this will display the RPM measurement). The rotational sensor
must be
active for operation
of this feature.
12.
CHECK MAIN FUSE
- indicates that the circuit fuse protection which is located on the back side of the
Phase 6 microprocessor controller (computer) the display would read CHECK MAIN FUSE. If the
display continues after the fuse has been replaced then it is the fault of the Phase 6 microprocessor
controller (computer).
B. L.E.D. (light emitting diode) DISPLAY INDICATORS
The L.E.D. (light emitting diode) indicator dots located on the top portion of the display indicate the various Phase
6 OPL computer output functions while a cycle is in progress. These indicator dots (as shown in the illustration
below)
DO NOT
necessarily mean that the outputs are functioning. They are only indicating that the function
output
should be
active (on).
1.
L.E.D. DISPLAY INDICATOR NUMBER 1
a. For Optional Reversing Models:
1) This indicator dot is on when the drive (tumbler [basket]) motor is operating in the forward mode
(clockwise [CW] direction).
2.
L.E.D. DISPLAY INDICATOR NUMBER 2
a. For Optional Reversing Models:
1) This indicator dot is on when the drive (tumbler [basket]) motor is operating in the reverse mode
(counterclockwise [CCW] direction).
3.
L.E.D. DISPLAY INDICATOR NUMBER 3
a. Heat Circuit Indicator:
1) This indicator dot is on whenever the Phase 6 OPL microprocessor controller (computer) is
calling for the heating circuit to be active (on).
4.
L.E.D. DISPLAY INDICATOR NUMBER 4
a. On Indicator
1) This indicator dot is on whenever a cycle is in progress. Additionally, when the Anti-Wrinkle
program is active, the indicator dot will be on whenever the Phase 6 OPL microprocessor controller
(computer) is in the Guard On Time program.
5.
L.E.D. DISPLAY INDICATOR NUMBER 5
a. Air Jet Circuit Indicator -
OPTIONAL
1) This indicator dot is on at the end of the dryer cycle for approximately 60 seconds.