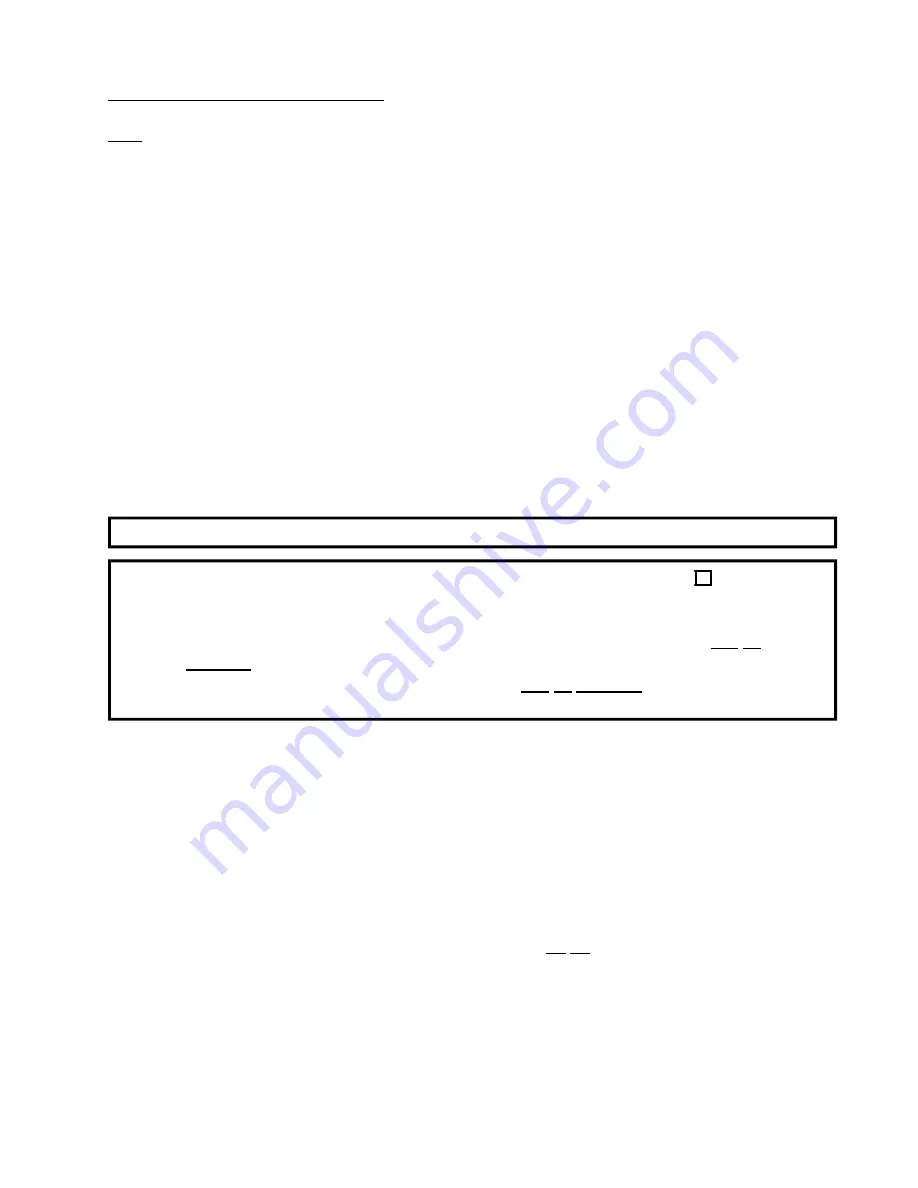
19
G. PREOPERATIONAL TESTS
ALL
dryers are thoroughly tested and inspected before leaving the factory. However, a preoperational test
should be
performed before the dryer is publicly used. It is possible that adjustments have changed in transit or
due to marginal location (installation) conditions.
1. Turn on electric power to the dryer.
2. Make sure the loading doors are closed and the lint drawers are closed.
3. Make sure “green” power button is in and illuminated.
4. Microprocessor controller (computer) system operational test - to start the dryer...
a. Display will read “READY.”
b. Press “D” (preprogrammed) cycle key on the keyboard (touch pad).
5. The dryer will then start. (i.e., blower, basket [tumbler] and heat.)
6. The light emitting diode (L.E.D.) display will read MANUAL DRYING CYCLE D, 40:00 MIN REMAIN.
NOTE:
Press the “UP ARROW” to view the basket (tumbler) temperature at any time.
NOTE:
The dryer can be stopped at any time by pressing the “STOP/CLEAR”
O
key. If the
temperature is above the Cool Down set point when the “STOP/CLEAR” is pressed, the
dryer will go into a Cool Down cycle followed by a Wrinkle Guard cycle. If the “STOP/
CLEAR” key is pressed again at this point the cycle that was in progress
will
be
canceled
and returned to the “READY” state. If the temperature is below the Cool
Down set point, the cycle that was in progress
will
be
canceled
, and go to Wrinkle
Guard.
7. When the programmed drying time has expired, the Phase 7 OPL microprocessor controller (computer)
will proceed into the Cool Down Cycle (Mode).
8. Once the Cool Down cycle begins at the end of the heat cycle the L.E.D. display will read COOL DOWN
TEMP ___/___MINUTE REMAINING. At the end of the heat cycle the dryer will shut off the heat, and
continue the fan and basket (tumbler) until the Cool Down Time, or temperature is reached.
9. Once the Cool Down cycle is completed the Phase 7 OPL microprocessor controller (computer) will
proceed into the Wrinkle Guard cycle. The Audio Alert tone will sound for (the amount set in Audio Alert
ON Time). The L.E.D. display will read “WRINKLE GUARD.” The times are fixed at 2 minutes OFF, 2
minutes ON for a maximum time of 99 minutes. These times are not programmable. During the ON time,
the blower (fan) and the basket (tumbler) will start to rotate (without heat for 2 minutes). The Phase 7 OPL
microprocessor controller (computer) will repeat this process until the Maximum Wrinkle Guard On Time
has expired (99 minutes). The L.E.D. display will then read “CYCLE DONE” and lockout the dryer
functions until the doors are opened. It will then return to “READY.”
Summary of Contents for AD-670 Phase 7
Page 16: ...12 ...
Page 44: ...40 B I O BOARD INPUT AND OUTPUT L E D INDICATORS ...
Page 59: ...55 ...
Page 60: ...ADC113049 5 09 03 04 0 ...