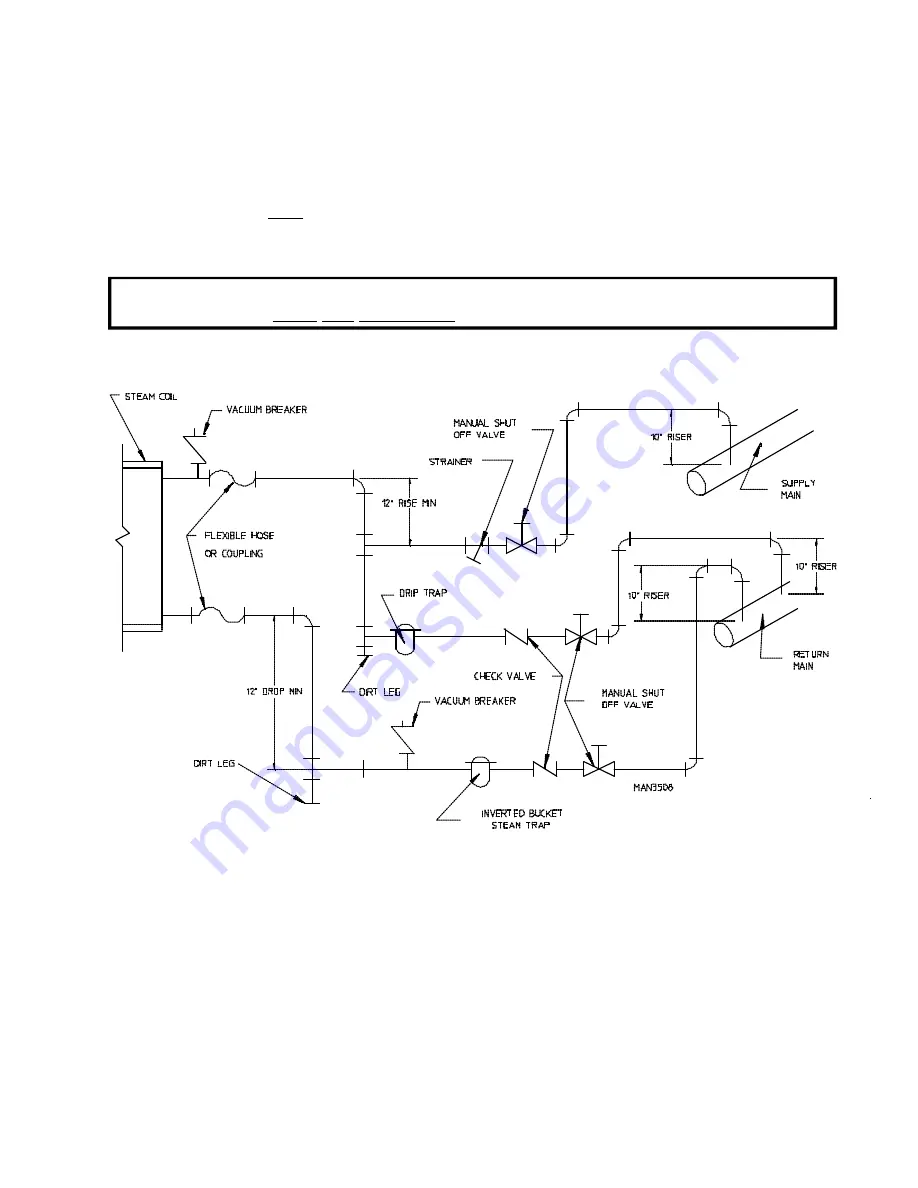
29
Install an inverted bucket steam trap and check valve at least 12-inches below the steam coil as near to the
coil as possible. A vacuum breaker
should be
installed in the piping. This will prevent the condensing steam
from causing a vacuum inside the coil, and possibly damaging the coil. The supply and return lines
should be
insulated. This will save energy and provide for the safety of the operator and maintenance personnel.
Water pockets in the supply line, caused by low points, will provide wet steam to the coil possibly causing
steam coil damage.
ALL
horizontal runs of steam supply piping
should be
pitched 1/4-inch for every one
(1) foot back towards the steam supply header causing the condensate in the line to drain to the header.
Install a bypass trap in any low point to eliminate wet steam.
IMPORTANT
: Flexible hose/coupling
must be
used. Coil failure due to hard plumbing connections
will VOID THE WARRANTY.
Summary of Contents for AD-30 (Export)
Page 30: ...26...