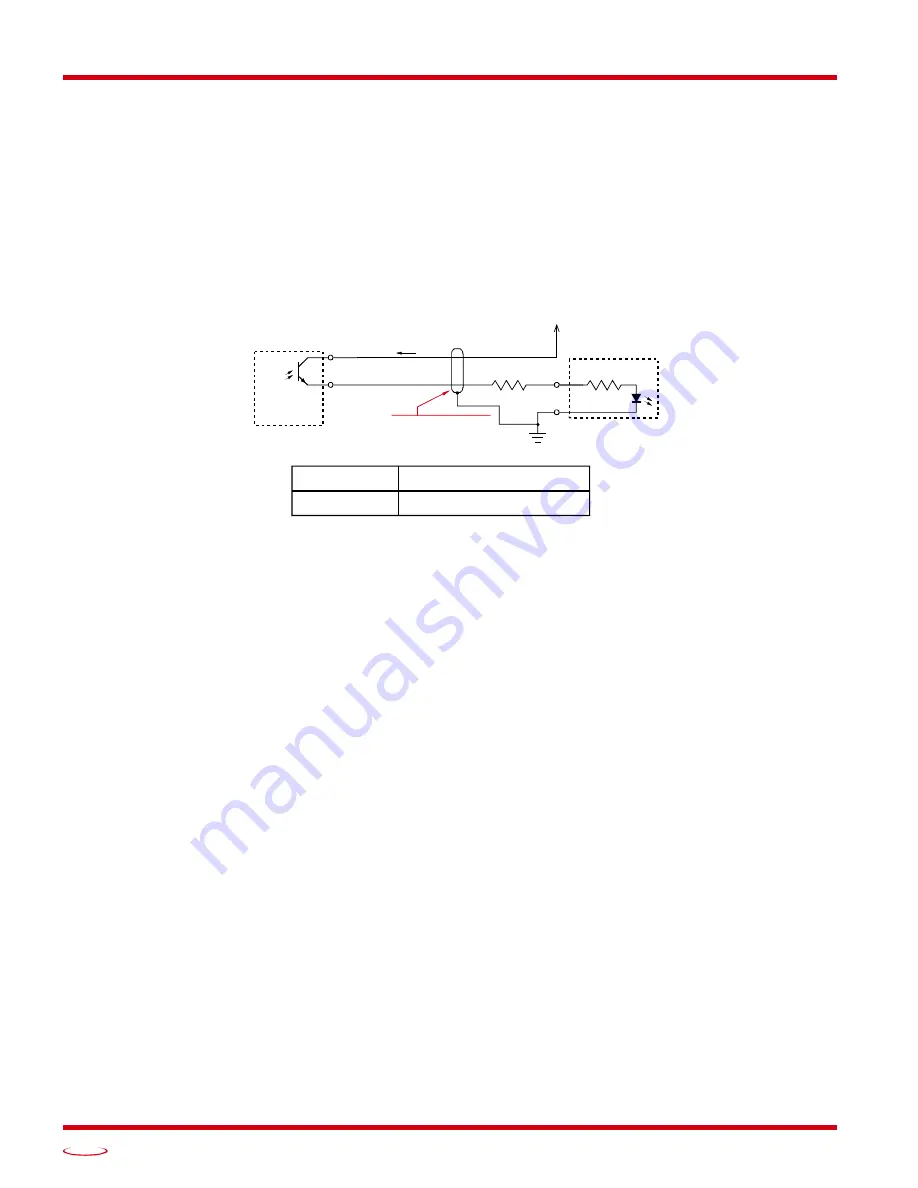
CONNECTING YOUR CONTROLLER
ADVANCED MICRO CONTROLS INC.
8
Output Wiring
The ±Fault Output is an optically isolated transistor capable of driving a typical PLC input. The Fault Output
is normally on (conducts current) and turns off under the following conditions:
!
The Interlock jumper is missing on the motor connector
!
There is a short in the motor, either phase to phase or phase to ground
!
The heatsink temperature exceeds 90°C (195°F)
!
The driver is in its reset state and is not ready to accept pulses
Both ends of the output are uncommitted, so it can be wired as a sourcing or sinking output. The figure shows
a typical connection as a sourcing output.
R
LIMIT
A resistor may be needed to limit the current through the Fault Output. The value, and power rating of the
resistor is dependent on the value of Vdc, the voltage drop across the input, and the current requirements of
the input.
SD17040C
Fault Output
FAULT+
FAULT–
R
LIMIT
*
V
DC
+5 to +24V
Open Collector Sourcing Output
PLC Input
Shielded, Twisted
Pair Cable
Ic
FAULT OUTPUT Electrical Specifications
V
DC
max:
V
CE
SAT
:
30Vdc
1Vdc @ 20 mA
Power Dissipation: 20 mW max.
Ic max: 20 mA
SAT
Summary of Contents for SD17040C
Page 15: ......