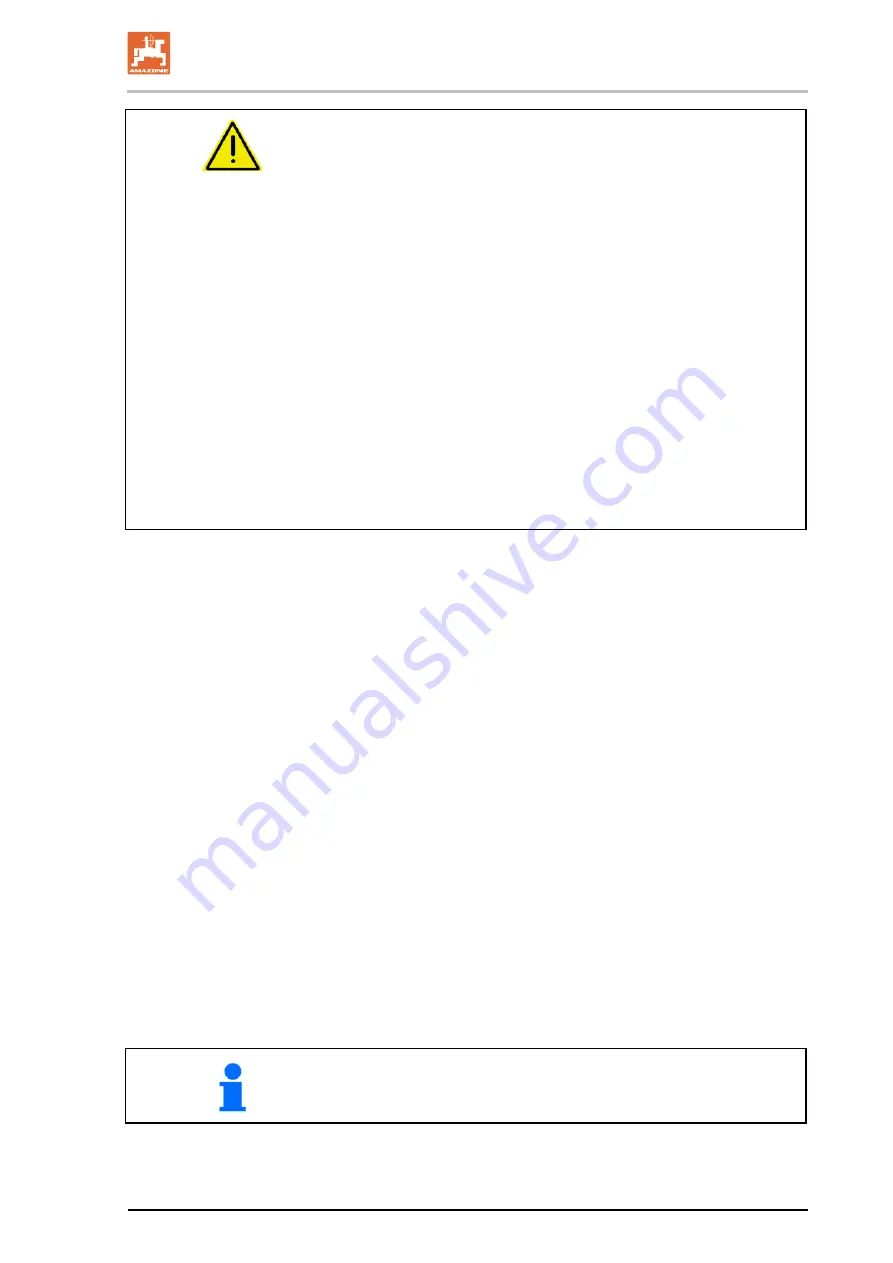
Coupling and uncoupling the machine
WARNING
Risk of crushing, being caught or pulled in, or impact when the
machine is unexpectedly released from the tractor.
•
Use the intended equipment to connect the tractor and the ma-
chine in the proper way.
•
When coupling the machine to the tractor's three-point hydraulic
system, ensure that the attachment categories of the tractor and
the machine are the same.
Upgrade the category II lower link pins on the machine to cate-
gory III using reducing sleeves if your tractor is equipped with
category III three-point hydraulics.
•
Only use the upper and lower link pins provided to couple up the
machine (original pins).
•
Check the upper and lower link pins for visible defects whenever
the machine is coupled. Replace the upper and lower link pins in
the event of clearly visible wear.
•
Secure the upper link pin and lower link pins in the attachment
points of the three-point attachment frame against unintentional
detachment using a linchpin.
•
Perform a visual inspection to ensure that the upper and lower
link hooks are correctly locked before reversing the tractor.
1. Secure the machine against unintentional rolling.
2. Always check for visible damage when coupling the machine:
3. Fasten the ball sleeves via the lower link pins in the hinging
points of the three-point attachment frame.
4. Secure each of the ball sleeves with linchpins to ensure that
they do not accidentally come loose.
5. Direct people out of the danger area between the tractor and
machine before you approach the machine with the tractor.
6. Drive the tractor up to the machine, so that you can couple the
top link.
7. Use bolts to couple the top link with the upper hinging point of
the three-point attachment frame.
8. Secure the top link with a linchpin.
9. Align the machine so that the lower hinging points of the ma-
chine hold the lower link hooks of the tractor.
10. Raise the three-point hydraulic system of the tractor until the
lower link hooks receive the ball sleeves and automatically inter-
lock.
11. Lift the front tank into its working position.
12. Direct people out of the danger area of the machine.
13. Perform a visual inspection to ensure that the upper and lower
links are correctly locked before reversing the tractor.
It may be necessary to remove the transportation device for ears
treatment or with tall crops to avoid damaging the grains.
FT
BAG0065.6 02.19
53
Summary of Contents for FT 1001
Page 59: ...Pump maintenance FT BAG0065 6 02 19 59...
Page 60: ......