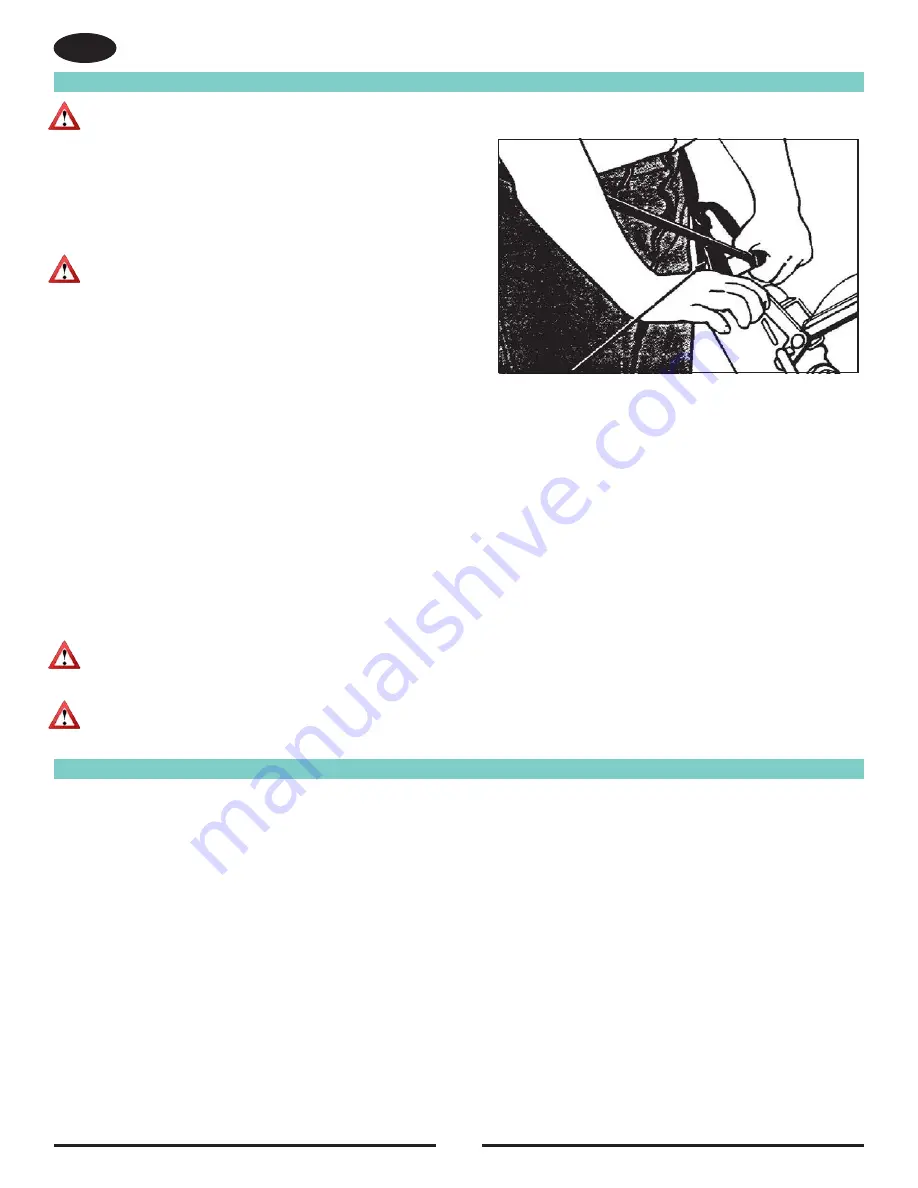
12
6. When drum is fully engaged with the surface, gradually adjust your pace for adequate finish removal. Keep sander in motion while
the drum is engaged with the surface or dwell marks will occur.
7. Move the machine in the direction of the grain in the wood whenever it is possible. Sand the surface at a constant pace.
8. Gradually feather-cut out at the termination point by easing the drum up with the control lever. (See Figure 13)
9. Repeat technique described in steps 5, 6, 7, and 8 and sand back down pass just made. When completed, begin a new pass by overlapping
previous pass half the width of the abrasive. Stagger termination points to prevent a distinct ridge and to promote a better blend when edging.
10. Empty contents of the dust bag into a metal container located outside the building. Dust bag should be emptied whenever full, as indicated
on bag.
WARNING: Serious operator injury could occur if the operator
has tied or strapped the loose end of the operator’s
belt strap to the machine. Always wrap the strap
so that you can let go and get away quickly in case
of bag fire or explosion.
4. Activate the control switch.
CAUTION: To prevent damage to the floor, make sure the
machine is in motion when the drum is engaged
with the floor.
5. Feather-cut in by easing the drum down onto the surface
with the control lever while the sander is in motion.
Operating Instructions
Figure 13
EN
WARNING:
Do not overfill dust bag or serious fire may result. Never leave a dust bag containing dust unattended.
Sanding dust can self ignite and cause a fire or explosion. Use only genuine American Sanders replacement bags.
CAUTION:
An overfilled dust bag may effect machine balance and performance. Do not handle or disturb dust bag and elbow
while sanding or damage to the floor may occur.
Sanding Cuts & Sandpaper
Initial Cut
The purpose of the initial cut is to remove old finish and gross imperfections on the floor surface. The sanding equipment should be adjusted to
heavy sanding pressure setting and a coarse abrasive belt should be used. If the surface is severely damaged by deep scratches, preexisting dwell
marks, uneven planks, etc., it may be necessary to sand across or diagonally to the grain to restore evenness to the surface. If these conditions are
not present, the initial cut should be done in the direction of the grain.
If glazing, loading, or burning takes place immediately into an initial cut, select a coarser abrasive. If this should occur during an initial cut, the
abrasive has dulled and must be replaced.
Final Cuts
The purpose of a finishing cut is to remove the scratches produced during the initial cut. Use a fine (60 - 80 grit) grain abrasive and a reduced
sanding pressure setting.
If the surface remains rough after a finishing cut, it may be necessary to use an even finer grain of abrasive (80 - 100 grit). Care should be taken in
selecting the grit size of the abrasive. A very fine grain will close the pores on a wood floor making admission of a stain difficult.
If glazing or burning should occur immediately into a finishing cut, reduce the sanding pressure. If it should occur during a finishing cut, the abrasive
has dulled and must be replaced.
Summary of Contents for American SANDERS FloorCrafter
Page 1: ...Belt Sander FloorCrafter Operator s Manual...
Page 2: ......
Page 17: ...17 Troubleshooting EN...
Page 19: ...19...
Page 21: ...21 Wiring Diagram RF081500 102120...
Page 37: ...37 07239A Serial Tag...
Page 39: ...39...