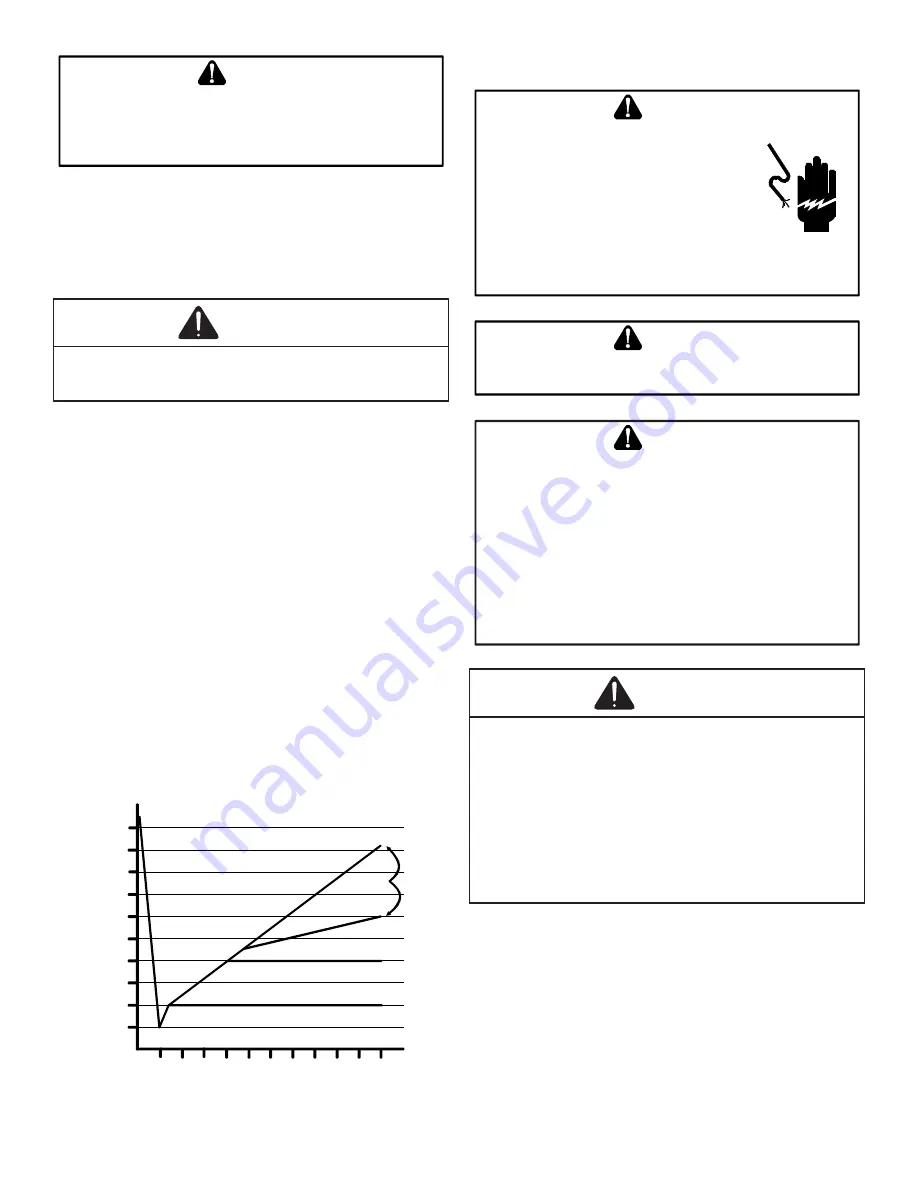
8
U
SE
REFRIGERANT
CERTIFIED
TO
AHRI
STANDARDS
. U
SED
REFRIGERANT
MAY
CAUSE
COMPRESSOR
DAMAGE
,
AND
THE
WARRANTY
. M
OST
PORTABLE
MACHINES
CANNOT
CLEAN
USED
REFRIGERANT
TO
MEET
AHRI
STANDARDS
.
IS
NOT
COVERED
UNDER
CAUTION
Start-up Procedure Detail
Liquid and suction valves on condensing unit are closed to
contain the charge within the unit. The unit is shipped with
the valve stems closed and caps installed. Do not open
valves until the indoor coil and line set is evacuated.
CAUTION
Prolonged operation at suction pressures less than 20 PSIG
for more than 5 seconds will result in overheating of the
compressor and permanent damage to it.
1. Connect the vacuum pump with
500
micron capability
to the service valves.
2. Evacuate the system to
500
microns or less using
gas and liquid service valves. Using both valves is
necessary.
3. Close pump valve and hold vacuum for 10 minutes.
Typically pressure will rise during this period.
• If the pressure rises to 1000 microns or less and
remains steady the system is considered leak-
free; proceed to start-up.
• If pressure rises above 1000 microns but holds
steady below 2000 microns, moisture and/or
noncondensibles may be present or the system
may have a small leak. Return to step 2: If the
same result is encountered check for leaks as
previously indicated and repair as necessary then
repeat evacuation.
• If pressure rises above 2000 microns, a leak is
present. Check for leaks as previously indicated
and repair as necessary then repeat evacuation.
5000
4500
4000
3500
3000
2500
2000
1500
1000
500
0 1 2 3 4 5 6 7 8 9 10
LEAK(S)
PRESENT
MINUTES
V
ACU
UM
IN
MI
CR
O
NS
CONDENSIBLES OR SMALL
LEAK PRESENT
NO
LEAKS
NO
CONDENSIBLES
ELECTRICAL CONNECTIONS
HIGH VOLTAGE!
D
ISCONNECT
ALL
POWER
BEFORE
SERVICING
.
M
ULTIPLE
POWER
SOURCES
MAY
BE
PRESENT
. F
AILURE
TO
DO
SO
MAY
CAUSE
PROPERTY
DAMAGE
,
PERSONAL
INJURY
OR
DEATH
DUE
TO
ELECTRIC
SHOCK
. W
IRING
MUST
CONFORM
WITH
NEC
OR
CEC
AND
ALL
LOCAL
CODES
. U
NDERSIZED
WIRES
COULD
CAUSE
POOR
EQUIPMENT
PERFORMANCE
,
EQUIPMENT
DAMAGE
OR
FIRE
.
WARNING
T
O
AVOID
THE
RISK
OF
FIRE
OR
EQUIPMENT
DAMAGE
,
USE
COPPER
CONDUCTORS
.
WARNING
GROUNDING REQUIRED!
A
LWAYS
INSPECT
AND
USE
PROPER
SERVICE
TOOLS
. L
ACK
OF
INSPECTION
OR
IMPROPER
TOOLS
MAY
CAUSE
EQUIPMENT
DAMAGE
OR
PERSONAL
INJURY
. A
LL
DISCONNECTED
GROUNDING
DEVICES
MUST
BE
RECONNECTED
BEFORE
INSTALLING
OR
SERVICING
. M
ULTIPLE
COMPONENTS
OF
THIS
UNIT
MAY
CONDUCT
ELECTRICAL
CURRENT
;
THESE
ARE
GROUNDED
. I
F
SERVICING
THE
UNIT
,
ANY
DISCONNECTION
OF
GROUNDING
WIRES
,
SCREWS
,
STRAPS
,
CLIPS
,
NUTS
OR
WASHERS
USED
TO
COMPLETE
THE
GROUND
MUST
BE
RETURNED
TO
THEIR
ORIGINAL
POSITION
AND
PROPERLY
FASTENED
.
CAUTION
NOTICE
•
Never install a phase-advancing capacitor. As this
unit is equipped with an inverter, installing a phase-
advancing capacitor will not only deteriorate power
factor improvement effect, but also may cause capacitor
abnormal heating accident due to high-frequency waves.
•
Do not change the setting of the protection devices. If
the pressure switch, thermal switch, or other protection
device is shorted and operated forcibly, or parts other
than those specified by Goodman are used, fire or
explosion could result.
•
Do not connect the ground wire to gas pipes, sewage
pipes, lightning rods, or telephone ground wires.
The condensing unit rating plate lists pertinent electrical
data necessary for proper electrical service and
overcurrent protection. Wires should be sized to limit
voltage drop to 2% (max.) from the main breaker or fuse
panel to the condensing unit. Consult the NEC, CEC, and
all local codes to determine the correct wire gauge and
length.
Summary of Contents for VXC20 Series
Page 6: ...6...
Page 26: ...26 Troubleshooting 1 This message is displayed when using the CTK04 thermostat...
Page 27: ...27 Troubleshooting 1 This message is displayed when using the CTK04 thermostat...
Page 29: ...29 Troubleshooting 1 This message is displayed when using the CTK04 thermostat...
Page 39: ...39...
Page 40: ...40...
Page 41: ...41...
Page 57: ...57...
Page 58: ...58...