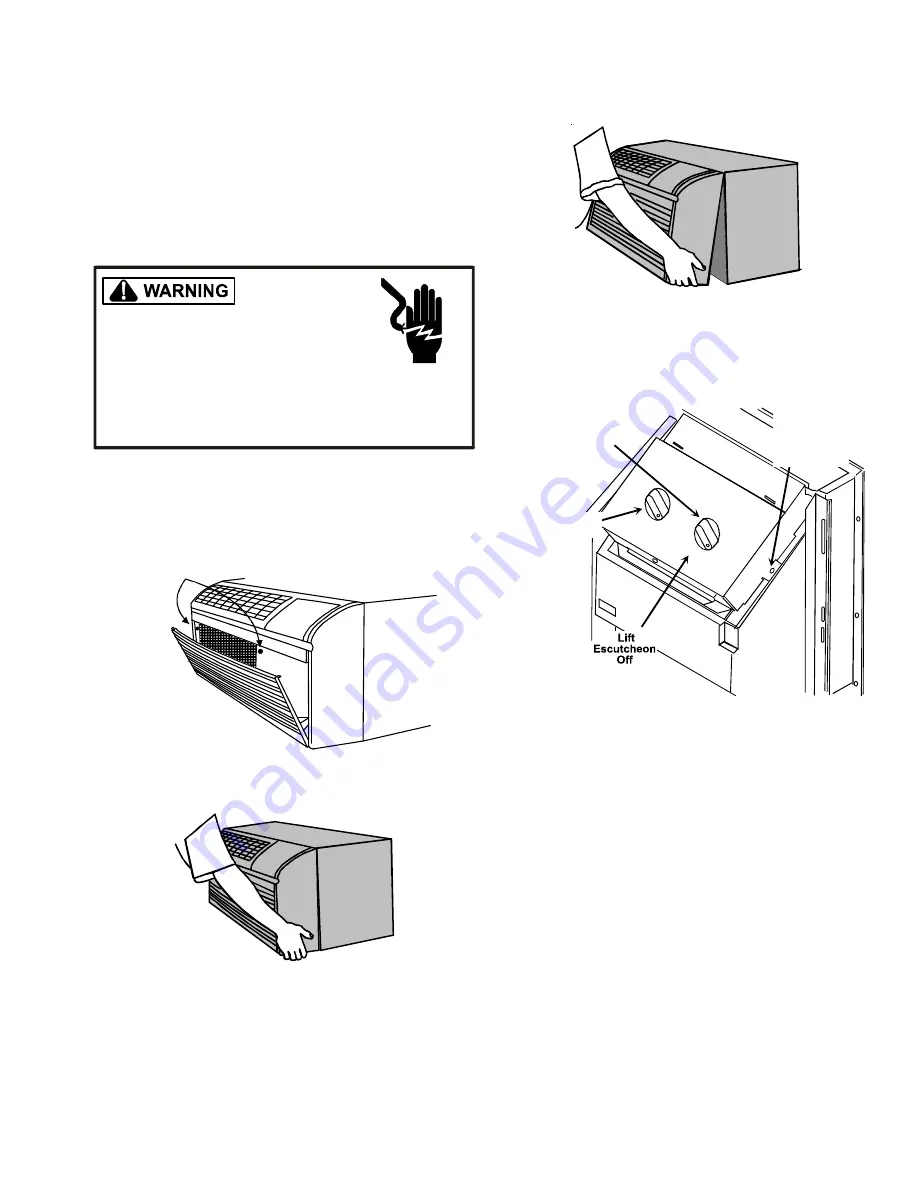
ACCESSORY INSTALLATIONS
51
Remote Thermostat High Fan Kit
Description
When a wall mounted thermostat is used, the PTAC unit will
operate in low speed only. Following these instructions will
allow the PTAC unit to operate on high speed only. This kit
contains twenty labels, enough for ten units.
HIGH VOLTAGE
D
ISCONNECT
ALL
POWER
BEFORE
SERVICING
OR
INSTALLING
THIS
UNIT
.
M
ULTIPLE
POWER
SOURCES
MAY
BE
PRESENT
.
F
AILURE
TO
DO
SO
MAY
CAUSE
PROPERTY
DAMAGE
,
PERSONAL
INJURY
OR
DEATH
.
1. Remove the two screws securing the front to the chas-
sis.
NOTE:
Not all installations will use these screws.
Holes to
secure front
2. Grasp the cabinet front as shown.
3. Pull the bottom of the cabinet front away from the chas-
sis until the retaining clips disengage.
4. Lift the cabinet front off the chassis.
5. Remove the unit control knobs by pulling the knobs off
the control shafts.
Pull To Remove
Mode Switch Knob
Control Panel
Cover Screws
Located on
Both Sides of
Control Panel
Pull To Remove
Thermostat Knob
6. Lifting the front edge of the escutcheon, slide the tabs at
the top of the escutcheon out of the retaining holes and
remove the escutcheon.
7. Remove the control panel cover by removing the two
screws holding the control panel cover in place. Tilt the
control panel forward to gain access to the wiring.
IMPORTANT NOTE:
Disconnect power to the unit and/or
turn the Master Switch on the control board to OFF when
connecting or altering wiring to any terminal - failure to do so
may result in shorting the fuse or damaging the control board.
8. On the control board switch BK16 along with all other
wires on the “FAN HIGH” and RD17 and all other wires
on the “FAN LOW” 1/4 inch terminals.
Summary of Contents for R-22
Page 5: ...ACCESSORY INSTALLATIONS 5 ...