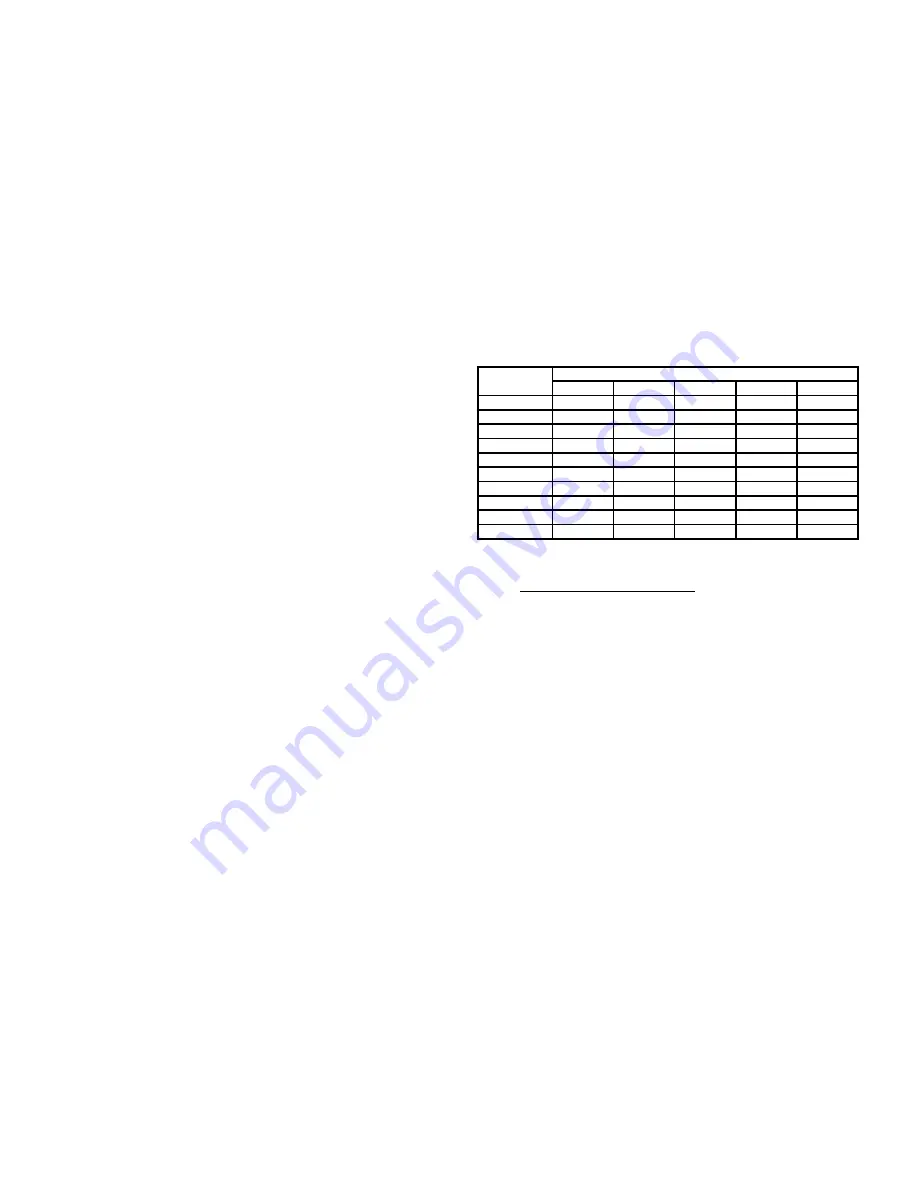
29
For furnaces being converted to LP gas, it is strongly
recommended that a LPLP03 kit also be installed. The
use of this kit will prevent the furnace from firing when
the LP gas supply pressure is too low to support proper
combustion.
All conversions must be performed by a qualified installer,
or service agency.
Gas Valve
This unit is equipped with a 24 volt gas valve controlled
during furnace operation by the integrated control
module. As shipped, the valve is configured for natural
gas. The valve is field convertible for use with propane
gas by replacing the regulator spring with a propane
gas spring from an appropriate manufacturer’s propane
gas conversion kit. Taps for measuring the gas supply
pressure and manifold pressure are provided on the valve.
The gas valve has a manual ON/OFF control located on
the valve itself. This control may be set only to the “ON”
or “OFF” position. Refer to the lighting instructions label
or Startup Procedure & Adjustment for use of this control
during start up and shut down periods.
Gas Piping Connections
The gas piping supplying the furnace must be properly sized
based on the gas flow required, specific gravity of the gas, and
length of the run. The gas line installation must comply with
local codes, or in their absence, with the latest edition of the
National Fuel Gas Code, NFPA 54/ANSI Z223.1 or CAN/CSA
B149.1-15 in Canada.
To connect the furnace to the building’s gas piping, the
installer must supply a ground joint union, drip leg, manual
shutoff valve, and line and fittings to connect to gas valve.
In some cases, the installer may also need to supply a
transition piece from 1/2” pipe to a larger pipe size.
The following stipulations apply when connecting gas
piping. Refer to
Gas Piping Connections
figure for typical
gas line connections to the furnace.
• Gas piping must be supported external to the furnace
cabinet so that the weight of the gas line does not
distort the burner rack, manifold or gas valve.
•
Use black iron or steel pipe and fittings for building
piping. Where possible, use new pipe that is properly
chamfered, reamed, and free of burrs and chips. If
old pipe is used, be sure it is clean and free of rust,
scale, burrs, chips, and old pipe joint compound.
•
Use pipe joint compound on male threads ONLY.
Always use pipe joint compound (pipe dope) that
is APPROVED FOR ALL GASES. DO NOT apply
compound to the first two threads.
•
Use ground joint unions.
• Install a drip leg to trap dirt and moisture before it can
enter the gas valve. The drip leg must be a minimum
of three inches long.
•
Install a 1/8” NPT pipe plug fitting, accessible for test
gauge connection, immediately upstream of the gas
supply connection to the furnace.
• Always use a back-up wrench when making the
connection to the gas valve to keep it from turning.
The orientation of the gas valve on the manifold must
be maintained as shipped from the factory. Maximum
torque for the gas valve connection is 375 in-lbs;
excessive over-tightening may damage the gas valve.
•
Install a manual shutoff valve between the gas
meter and unit within six feet of the unit. If a union
is installed, the union must be downstream of the
manual shutoff valve, between the shutoff valve and
the furnace.
• Tighten all joints securely.
Natural Gas Capacity of Pipe
In Cubic Feet of Gas Per Hour (CFH)
Length of
Nominal Black Pipe Size
Pipe in Feet
1/2"
3/4"
1"
1 1/4"
1 1/2"
10
132
278
520
1050
1600
20
92
190
350
730
1100
30
73
152
285
590
980
40
63
130
245
500
760
50
56
115
215
440
670
60
50
105
195
400
610
70
46
96
180
370
560
80
43
90
170
350
530
90
40
84
160
320
490
100
38
79
150
305
460
(Pressure 0.5 psig or less and pressure drop of 0.3" W.C.; Based on
0.60 Specific Gravity Gas)
CFH =
BTUH Furnace Input
Heating Value of Gas (BTU/Cubic Foot)
• Connection method must be in compliance with all
local and national codes. US: National Fuel Gas
Code (NFGC) NFPA 54-2012/ANSI Z223.1-2012 and
the Installation Standards, Warm Air Heating and Air
Conditioning Systems ANSI/NFPA 90B.
In Canada, CANADA: National Standard of Canada,
Natural Gas and Propane Installation Code
(NSCNGPIC) CSA B149.1-15.
Connect the furnace to the building piping by one of
the following methods:
─ Rigid metallic pipe and fittings.
─ Semi-rigid metallic tubing and metallic fittings.
Aluminum alloy tubing must not be used in
exterior locations. In order to seal the grommet
cabinet penetration, rigid pipe must be used to
reach the outside of the cabinet. A semi-rigid
connector to the gas piping may be used from
there.
•
Use listed gas appliance connectors in accordance
with their instructions. Connectors must be fully in
the same room as the furnace.
• Protect connectors and semi-rigid tubing against
physical and thermal damage when installed. Ensure
aluminum-alloy tubing and connectors are coated to
protect against external corrosion when in contact
with masonry, plaster, or insulation, or subjected to
repeated wetting by liquids such as water (except rain
water), detergents, or sewage.