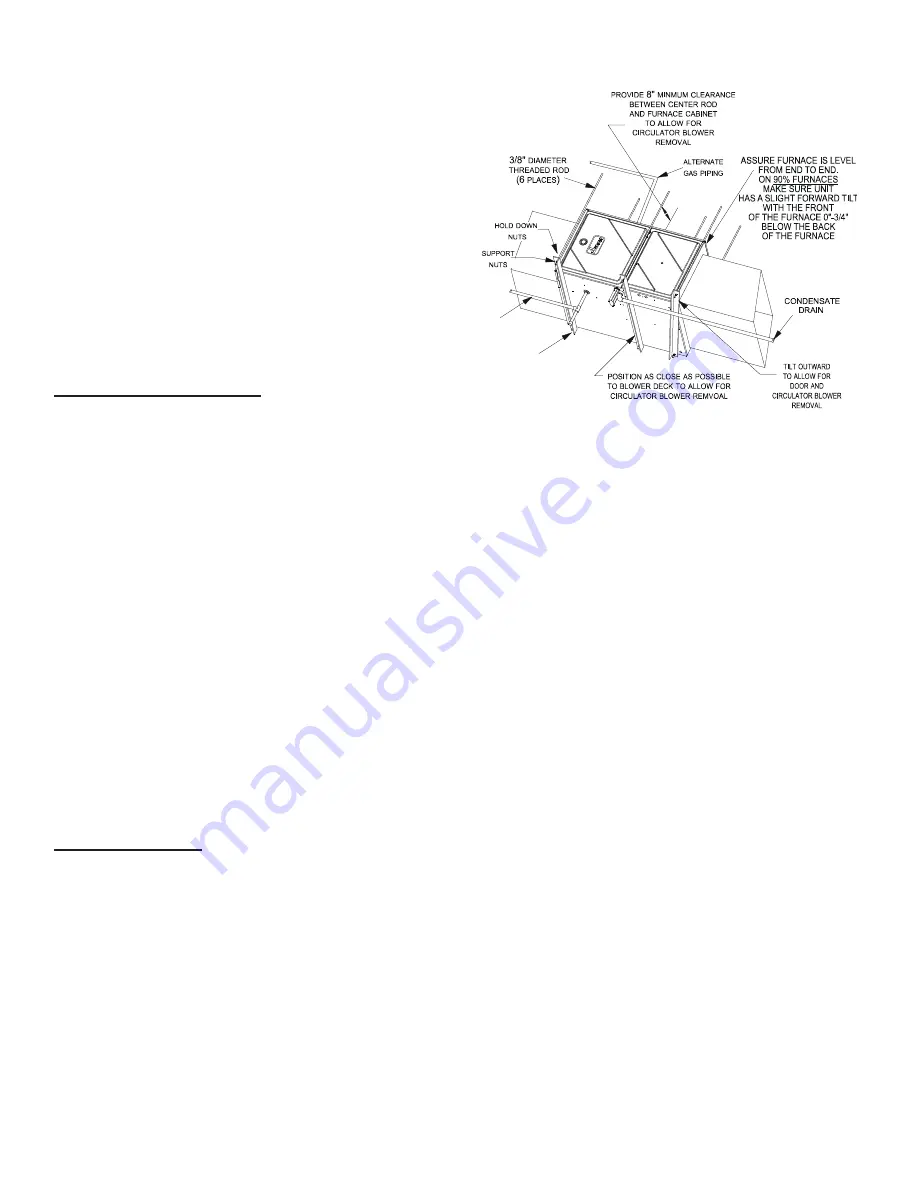
SYSTEM OPERATION
9
Combustion and Ventilation Air Requirements
section
in this manual or the installation instructions for details.
•
If the furnace is used in connection with a cooling unit,
install the furnace upstream or in parallel with the cooling
unit coil. Premature heat exchanger failure will result if
the cooling unit coil is placed ahead of the furnace.
•
If the furnace is installed in a residential garage, position
the furnace so that the burners and ignition source are
located not less than 18 inches (457 mm) above the floor.
Protect the furnace from physical damage by vehicles.
•
If the furnace is installed horizontally, the furnace access
doors must be vertical so that the burners fire horizontally
into the heat exchanger. Do not install the unit with the
access doors on the “up/top” or “down/bottom” side of
the furnace.
C
learances and Accessibility
Installations must adhere to the clearances to combustible
materials to which this furnace has been design certified. The
minimum clearance information for this furnace is provided
on the unit’s clearance label. These clearances must be
permanently maintained. Refer to Specification Sheet for
minimum clearances to combustible materials. Clearances
must also accommodate an installation’s gas, electrical,
and drain trap and drain line connections. If the alternate
combustion air intake or vent/flue connections are used on
a 90% furnace, additional clearances must be provided to
accommodate these connections. Refer to
Vent Flue Pipe and
Combustion Air Pipe
section in this manual or the installation
instructions for details.
NOTE:
In addition to the required
clearances to combustible materials, a minimum of 24 inches
service clearance must be available in front of the unit.
A furnace installed in a confined space (i.e., a closet or
utility room) must have two ventilation openings with a total
minimum free area of 0.25 square inches per 1,000 BTU/hr of
furnace input rating. One of the ventilation openings must be
within 12 inches of the top; the other opening must be within
12 inches of the bottom of the confined space. In a typical
construction, the clearance between the door and door frame
is usually adequate to satisfy this ventilation requirement.
Furnace Suspension
If suspending the furnace from rafters or joist, use 3/8”
threaded rod and 2”x2”x1/8” angle iron as shown in the
following figure. If the furnace is installed in a crawl space it
must also be suspended from the floor joist or supported by
a concrete pad. Never install the furnace on the ground or
allow it to be exposed to water. The length of rod will depend
on the application and the clearances necessary.
2" 2" 1/8"
ANGLE
IRON
(3
PLACES
)
X
X
GAS
PIPING
90% Suspended Furnace Shown
Existing Furnace Removal
NOTE:
When an existing furnace is removed from a venting
system serving other appliances,
the venting system may be
too large to properly vent the remaining attached appliances.
The following vent testing procedure is repro duced from
the
American National Standard/National Standard of
Canada for Gas-Fired Central Furnaces ANSI Z21.47,
latest edition, CSA-2.3b, latest edition Section 1.23.1.
The following steps shall be followed with each appliance connected
to the venting system placed in operation, while any other appliances
connected to the venting system are not in operation:
a. Seal any unused openings in the venting system;
b. Inspect the venting system for proper size and horizontal pitch,
as required by the National Fuel Gas Code, ANSI Z223.1
or the CSA B149 Installation Codes and these instructions.
Determine that there is no blockage or restriction, leakage,
corrosion and other deficiencies which could cause an unsafe
condition;
c. In so far as practical, close all building doors and windows
and all doors between the space in which the appliance(s)
connected to the venting system are located and other spaces
of the building. Turn on clothes dryers and any appliance
not connected to the venting system. Turn on any exhaust
fans, such as range hoods and bathroom exhausts, so they
shall operate at maximum speed. Do not operate a summer
exhaust fan. Close fireplace dampers;
d. Follow the lighting instructions. Place the appliance being
inspected in operation. Adjust thermostat so appliance shall
operate continuously;
e. Test for draft hood equipped spillage at the draft hood relief
opening after 5 minutes of main burner operation. Use the
flame of a match or candle;
f. After it has been determined that each appliance connected
to the venting system properly vents when tested as outlined
above, return doors, windows, exhaust fans, fireplace dampers
and any other gas burning appliance to their previous
conditions of use;
g. If improper venting is observed during any of the above tests,
the common venting system must be corrected.