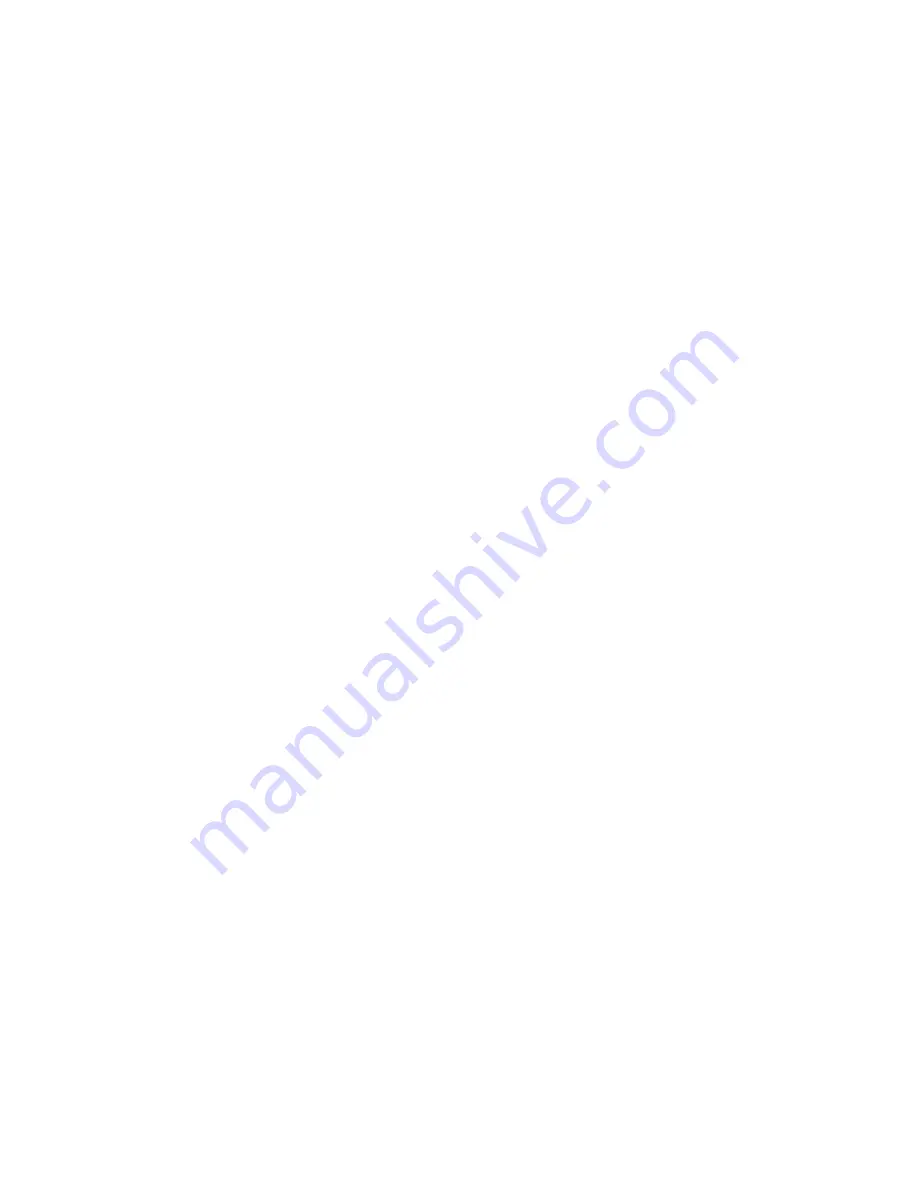
SYSTEM OPERATION
25
used, a connecting duct must be installed between the unit
and the utility room wall so the blower will not interfere with
combustion air or draft. The room, closet, or alcove must not
be used as a return air chamber.
When the furnace is used in connection with a cooling unit,
the furnace should be installed in parallel with or on the
upstream side of the cooling unit to avoid condensation in
the heating element. With a parallel flow arrangement, the
dampers or other means used to control the flow of air must
be adequate to prevent chilled air from entering the furnace
and, if manually operated, must be equipped with means to
prevent operation of either unit unless the damper is in the
full heat or cool position.
When the furnace is heating, the temperature of the return
air entering the furnace must be between
55°F
and
100°F
.
UPRIGHT FILTER INSTALLATIONS
Depending on the installation and/or customer preference,
differing filter arrangements can be applied. Filters can be
installed in the central return register and a side panel external
filter rack kit (upflow filter kit # EFR02). As an alternative
a media air filter or electronic air cleaner can be used as
the requested filter. Refer to the following minimum filter
requirement charts for determination of the minimum filter area
to ensure proper unit performance.
The following
figures
show possible filter locations.
NOTE:
A ductwork access
door must be used in counterflow applications to allow filter
removal. If the filter rack is used, the side of the plenum must
be at least as tall as dimension “A” shown in the following
illustration. For dimension of “A” refer to the following chart.
Refer to Minimum Filter Area tables to determine filter area
requirement.
NOTE:
Filters can also be installed elsewhere
in the duct system such as a central return.
Horizontal Installations
Filter(s) must be installed external to the furnace casing for
horizontal installations. For most installations it is preferable
to use a central return with filters installed in the duct behind
the return air grill. In this way filter replacement is relatively
simple by merely removing the grille, rather than going into
the attic or crawl space.
ADDITIONAL FILTERING ACCESSORIES
External Filter Rack Kit (EFR02)
The external filter rack kit is intended to provide a location
external to the furnace casing, for installation of a permanent
filter on upflow model furnaces. The rack is designed to mount
over the indoor blower compartment area of either side panel,
and provide filter retention as well as a location for attaching
return air ductwork.
Electronic Air Cleaner (ASAS and GSAS) or Media Air
Cleaner (AMU and GMU)
The electronic air cleaner and media air cleaner are multi-
positional high efficiency air filtration devices that can be
installed in any position, except with the access door facing
down. The best location for the air cleaner is in the return
air duct next to the blower compartment. Before installing
the air cleaner, consider the application. The electronic air
cleaner must be readily accessible for periodic inspection and
cleaning of the pre-filters and electronic cells while the media
air cleaner must be readily accessible for periodic inspection
and replacement of the Media Air Cleaner (AMU and GMU)
filter cartridge (3 per carton) M0-1056, M1-1056, M2-1056,
M8-1056, to maintain maximum efficiency and trouble-free
operation. Carbon Filters 1156-3 and 1856-3 (set of 3) are also
available. See Product Catalog for exact filter for your model.
NORMAL SEQUENCE OF OPERATION
Power Up
1. 115 VAC power applied to furnace.
2. Integrated ignition control module performs internal
checks.
3. Integrated ignition control module LED will light.
4. Integrated ignition control monitors safety circuits contin-
uously.
5. Furnace awaits call from thermostat.
Normal Heating Sequence
1. R and W thermostat contacts close, initiating a call for
heat.
2. Integrated control module performs safety circuit checks.
3. The induced draft blower is energized causing pressure
switch contacts to close. Induced draft blower remains
energized for pre-purge period.
4. Ignitor warm up begins after pre-purge is completed.
The ignition control has a WARM UP PERIOD OF 17
SECONDS.
5. Gas valve opens at end of ignitor warm up period, deliv-
ering gas to burners to establish flame.
6. The control checks for a signal from the flame sensor
within seven (4) seconds after the gas valve is energized.
Gas will only continue to flow if a flame signal is present.
7. Circulator blower is energized on heat speed following a
fixed thirty (30) second blower on delay.
8. Furnace runs, integrated control module monitors safety
circuits continuously.
9. R and W thermostat contacts open, allowing the gas valve
to cycle off.
10. Induced draft blower is de-energized following a fifteen
(15) -second post purge.
11.
Circulator blower is de-energized following heat off delay
period.
12. Furnace awaits next call from thermostat.