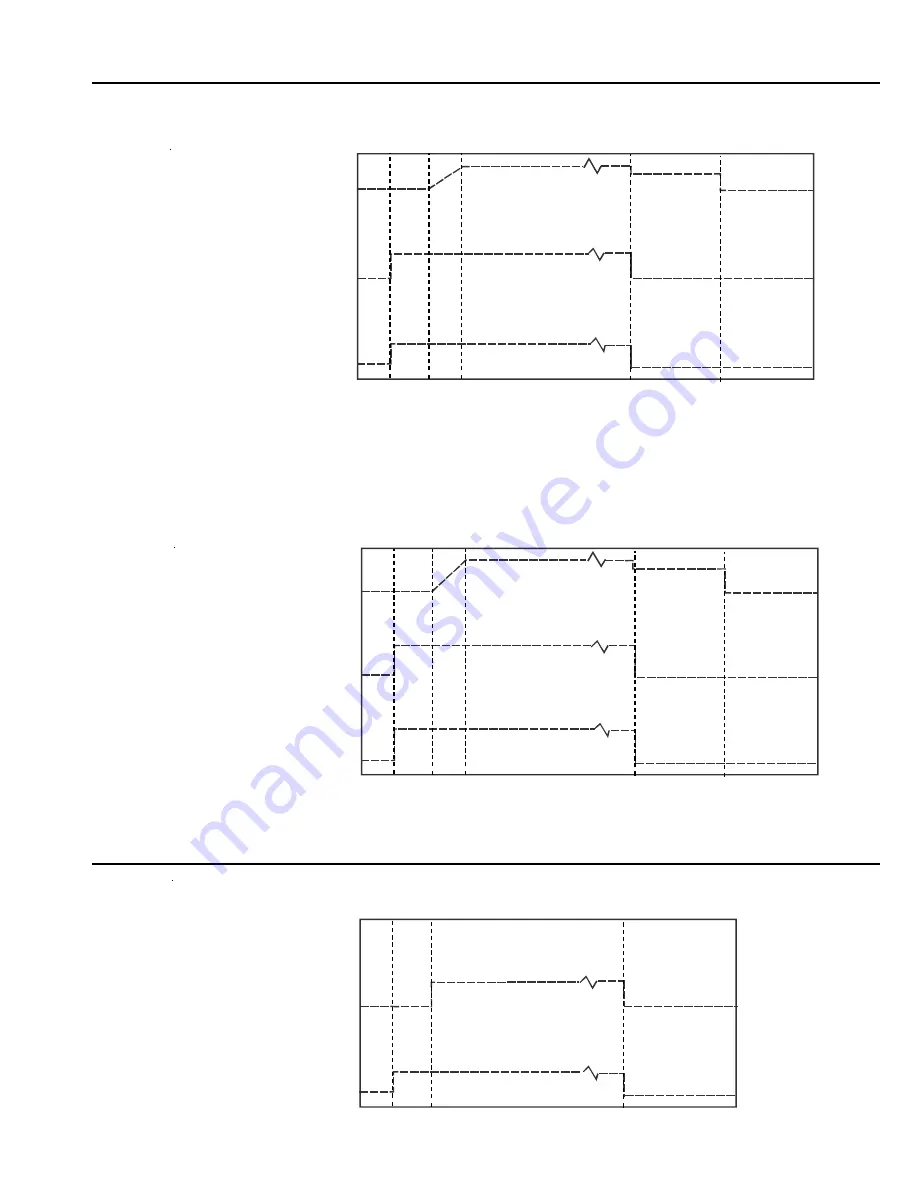
35
35
Timing Charts for Normal Cooling Operation
Example 1: Continuous Call For Low Stage Cooling Only
0 5 35 0 45
High
Low
Off
Circulator
Blower
Outdoor Fan
And
Compressor
Thermostat
Time (sec)
(Call For Cool)
High
Low
Off
High
Low
Off
(88% of Low)
Example 2: Continuous Call For High Stage Cooling Only
0 5 35 0 45
High
Low
Off
Circulator
Blower
Outdoor Fan
And
Compressor
Thermostat
Time (sec)
(Call For Cool)
High
Low
Off
High
Low
Off
(88% of High)
0 5 0
On
Off
On
Off
Circulator
Blower
Thermostat
(Call For Fan)
Time (sec)
Timing Chart for Normal Fan Operation