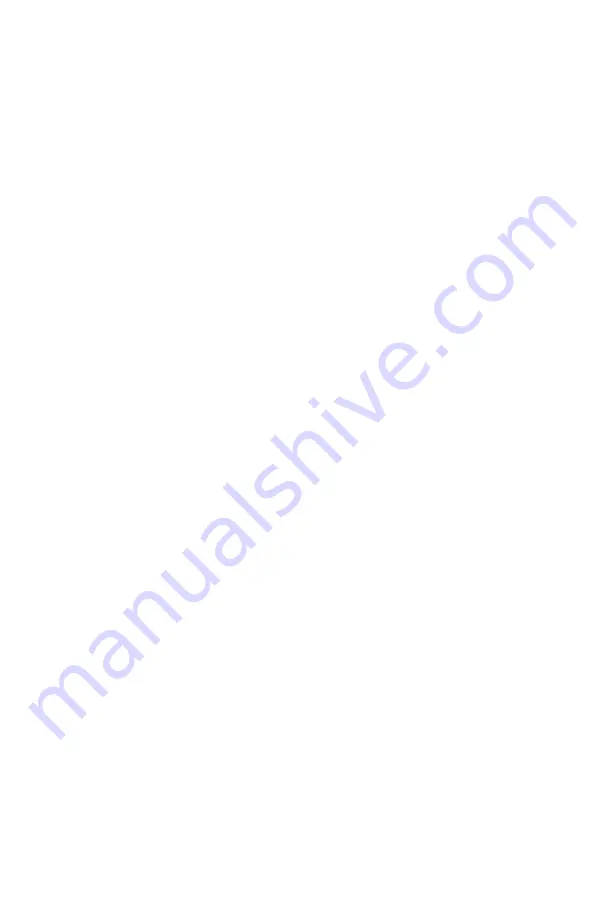
- 12 - LINQ8ACM(CB)
8.
Battery Backup: select whether the output will be backed up in the event of a power failure.
Uncheck the associated box to disable battery back for that output.
9.
Over/Under Current: Enter both the High and Low current limits for the associated output.
If either of these limits are exceeded an alert message and/or email notification will be generated.
10.
Over/Under Voltage: Enter both the High and Low voltage limits for the associated output.
If either of these limits are exceeded an alert message and/or email notification will be generated.
11. Click on the button labeled
Submit to save the settings.
Temperature Settings:
1. Click on the
Temperature tab at the top of the screen.
2. Enter the high temperature threshold in Celsius.
3. Click on the button labeled
Submit to save the settings.
Battery Service Date(s):
If batteries are not being used uncheck the box under
Present to disable battery monitoring.
1. Click on the
Batteries tab at the top of the screen.
2. Enter the date the batteries were installed under
Installation Date for each connected power supply.
3. Enter the date for battery service under
Service Date for each connected power supply.
NOTE: Batteries should be inspected at least once a year. Even through the expected battery life is
five (5) years it is recommended replacing batteries every four (4) years.
4. Click on the button labeled
Submit to save the settings
Power Supply Settings:
If only one (1) power supply is being used uncheck the box under
Present next to the unused power supply to
disable monitoring.
1. Click on the
Power Supplies tab at the top of the screen.
2.
Over/Under Voltage: Enter both the High and Low voltage limits for the associated input.
If either of these limits are exceeded an alert message and/or email notification will be generated.
3.
Over/Under Current: Enter both the High and Low current limits for the associated input.
If either of these limits are exceeded an alert message and/or email notification will be generated.
4. Click on the button labeled
Submit to save the settings
Output Current Calibration:
During the initial setup all outputs need to be calibrated to insure accurate current readings.
1. Click on the
Calibration tab at the top of the screen.
2. With all loads disconnected click on the tab labeled
Calibrate All Zero Offset Currents to set all output
currents to zero.
3. Connecting each output one at a time, measure the current draw and enter this value for this output
under
Actual.
4. Click on the button labeled
Calibrate Gain to save the settings.
5. Repeat steps 3 & 4 for all remaining outputs.
When replacing or adding a new device the output needs to be recalibrated.
1. Click on the
Calibration tab at the top of the screen.
2. With the load disconnected from the output, click on the tab labeled
Calibrate Offset for the output to set its
current to zero.
3. Connect the output, measure the current draw and enter this value under
Actual.
4. Click on the button labeled
Calibrate Gain to save the settings.
5. Repeat steps 3 & 4 for all remaining outputs.
B. Timer Setup:
Click on the
Timers tab to access the timers setup screen.
1. Click on the
Add New Timer bar.
2.
Timer Label: Enter a descriptive name for the timer function.
3.
Timer Start Date: Enter the date on which the timing function will start (i.e. 10/09/2019).
4.
Timer Interval: Using the pulldown menu select the interval the time will operate.
5.
Timer Start Time: enter the time that the timer event will start.
6.
Timer Actions: Select the function for each output that will occur during the timer event.
7. Click on the button labeled
Submit to save the settings.
To add additional timer events, repeat steps 1-7.
C. Network Setup:
1. Click on the
TCP/IP tab to access the IP settings screen.
2. Click on the
Configure IP Settings tab at the top of the screen to access the IP setup.
3. In the
Method field use the pulldown menu select the method that the IP Address for the LINQ8ACM(CB)
will be obtained: “Static” or “DHCP”, then follow the appropriate steps below.