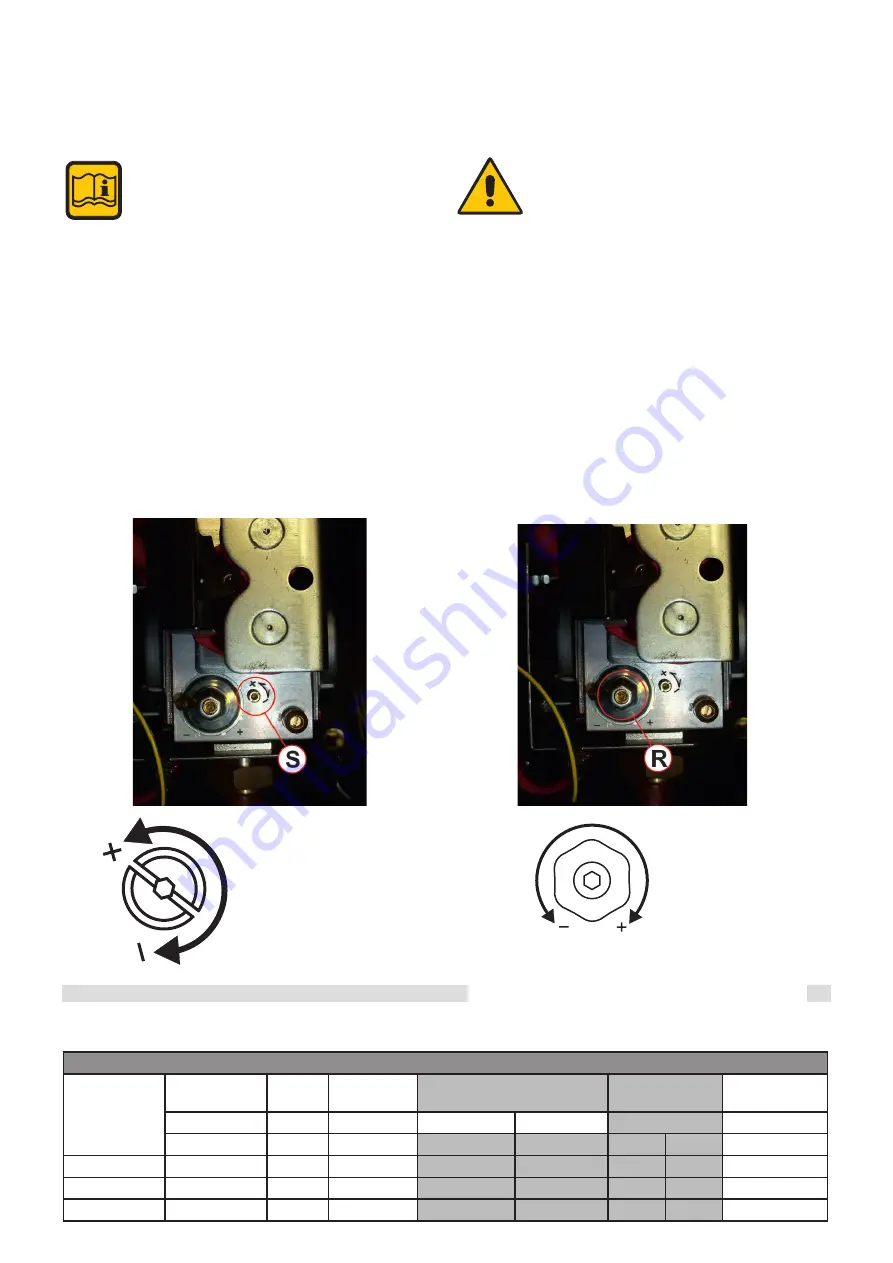
37
All of the instructions below are provided for the
exclusive use of
authorised assistance
personnel.
3.13 BURNER ADJUSTMENT
(S)
MAXIMUM POWER
ADJUSTING SCREW
(R)
MINIMUM POWER
ADJUSTING SCREW
- Remove the cap and insert the CO2 analysis probe into the
fl
ue gas
output of the intake/exhaust terminal, see chap. 3.12.2.
All boilers are factory calibrated and tested. If necessary,
recalibrate the gas valves (MODULE1, MODULE 2, etc.)
2) Adjustment at minimum power
:
- Start the boiler in “calibration” mode at MINIMUM POWER (see
3.12.1)
- Once the burner is on, check that the CO2 value at “MINIMUM”
power corresponds with what is indicated in the “NOZZLES - PRES-
SURES” table.
- If necessary, correct the value by turning (using a 2.5 mm Allen
key) screw
“R”
; CLOCKWISE increases it and ANTICLOCKWISE
decreases it (refer to the “NOZZLES - PRESSURES” table).
1) Adjustment at maximum power:
- Start the boiler in “calibration” mode at MAXIMUM POWER (see
3.12.1)
- Once the burner is on, check that the CO2 value at “MAXIMUM”
power corresponds with what is indicated in the “NOZZLES - PRES-
SURES” table.
- If necessary, correct the value by turning adjusting screw
“S”
CLOCKWISE to decrease it and ANTICLOCKWISE to increase it
(see the NOZZLES-FLOW RATES-PRESSURES table).
Instructions for the installer
ARES TEC ErP:
440-550-660-770-900
Type of
Gas
Supply pressure Ø Noz-
zles
Diaphragm
Fan speed
CO
2
levels
Power at ignition
[mbar]
(mm)
[mm]
Min.
Max.
[%]
[%]
FL Min.
FU Max.
Min.
Max.
IG
Nat. gas (G20)
20
9
-
28
108
8.8
8.8
50
Nat. gas (G25)
25
9
-
28
113
9.1
8.5
50
Propane (G31)
37
9
-
28
101
10.8
10.6
50
NOZZLES - PRESSURES - FLOW RATES TABLE
+/- 0.2%