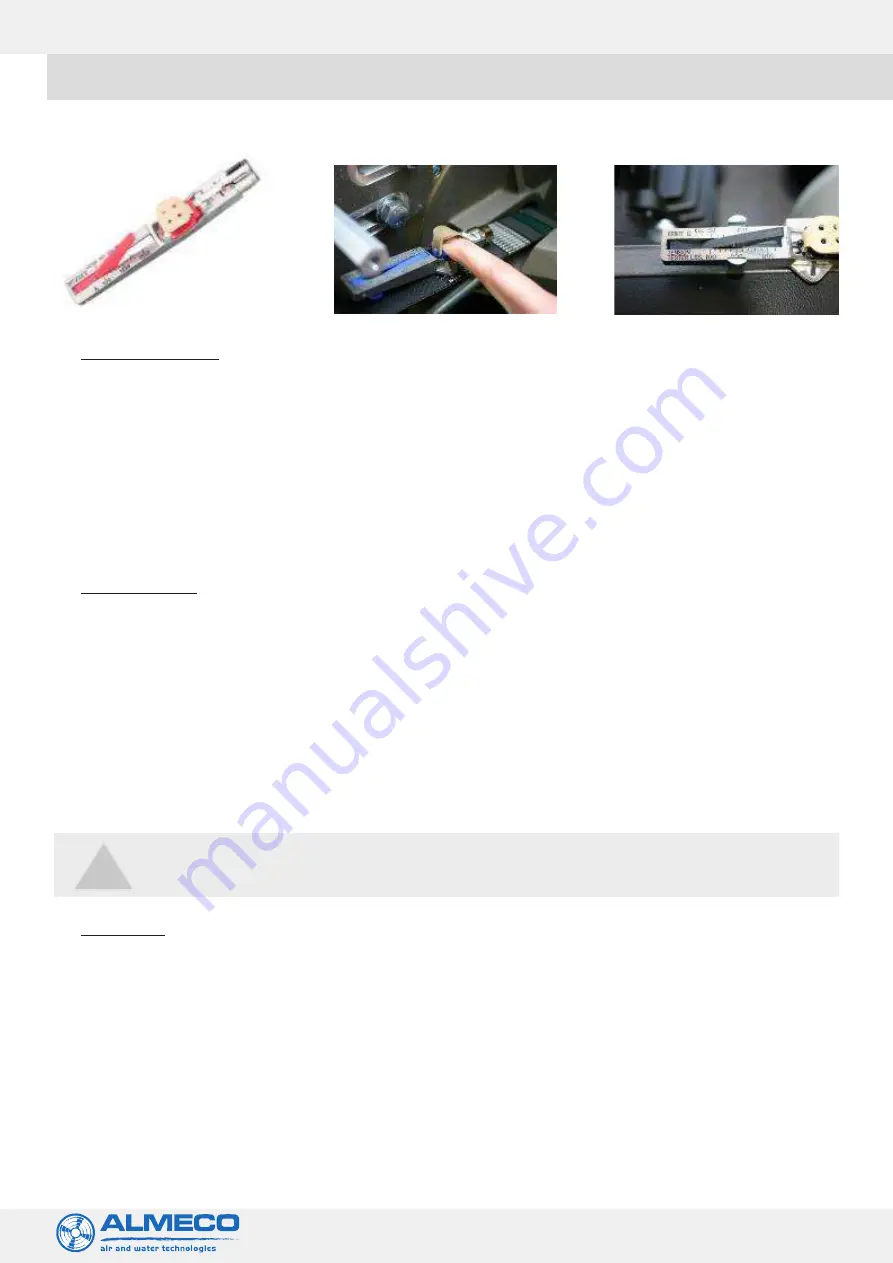
ALMECO nv
Air and water technologies
Royennestraat 51, B-7700 Moeskroen
[email protected] - www.almeco.eu
12
EP10A
compact blower
!
Image: EP10A Tension Gauge (ref: Krikit Gauge)
To remove a drive belt
•
Isolate the power supply.
•
Remove the belt guard.
•
Disconnect any ducting.
•
Loosen the 4 off M10 bolts clamping the motor mounting plate to the blower back plate, using a 17mm spanner or
socket.
•
Slacken the 2 off M12 nuts on adjustment screw above and below adjustment anchor cast into motor mounting
plate, slacken top nut using a 19mm spanner, to allow the blower head/back plate assembly to drop sufficiently to
facilitate the removal of the belt.
•
After removal ensure the pulleys are clear of any dust or debris. If the belt is to be re-used wipe with a dry cloth before
attempting to refit.
To refit a drive belt
•
Fit the new belt over the pulleys ensuring that it is correctly aligned with the poly-vee pulleys. Do not force the belt or
roll the belt onto the pulleys. Ensure the blower head is low enough to allow the belt to clear before attempting to fit.
•
Using the M12 nuts on the adjusting screw, apply sufficient tension to raise the blower head/back plate assembly into
its approximate position and lightly tighten the M10 bolts to hold the assembly in place.
•
Tension using the M12 nut on the upper side of the adjustment anchor checking the tension with ‘Krikit’ tension
gauge supplied. (Refer to figures 4 & 5). When the correct tension is achieved (50kg or110lbs on the scale), lock
adjuster by tightening the M12 nut on the underside of the adjustment anchor and tighten M10 bolts to approx.
20N/M.
•
After fitting a new belt, the tension should be re-checked after the unit has been run between 10-20 minutes. This is
due to initial stretch of a new belt.
•
Only drive belts supplied by Almeco should be used.
Blower heads
The EP10A’s head assembly comprises:
a. fan case
b. inlet ring
c. back plate
d.
impeller
e. spindle assembly
When replacing this compact blower head, the pulley and hub position must be checked. [Please note - This blower head
is a newer design with a different pulley position to older units supplied pre 2002.]
For standard metric frame motors the hub that the pulley mounts on must be 20-21mm from the motor flange face. If it is
a NEMA motor this dimension must be 14-15mm.
Drive belts supplied by Almeco should be used.