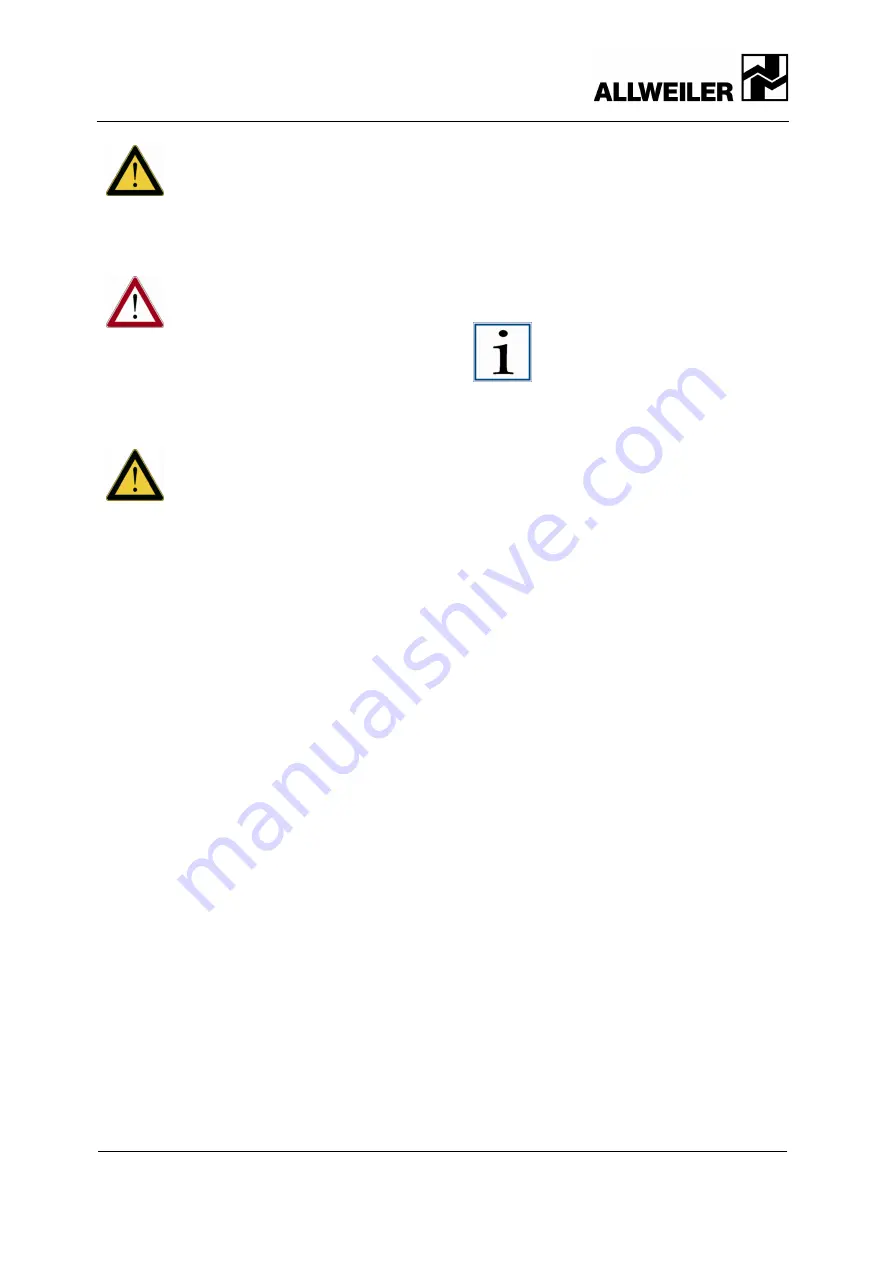
Installation and connection
Laying the pipes
16
Series AE1F, AE1L, AE.E, AE.N, AE.H, AE.V, AED1E,
AED2N
ID, ZD construction types
BA-2011.11
760.0002 GB - 150 500
Caution!
Excessive tightening will destroy
the pump’s antifriction bearing.
Observe our separate “V-belt”
instructions (VM 706.0001/ID
number 133 586).
Warning!
Danger of being caught, wound,
drawn in, and trapped.
Install safety guarding according to
DIN EN 809!
6.5.2 Space requirement for
maintenance and repair
Caution!
The pump must be accessible from
all sides in order to enable the
necessary visual inspections.
Provide enough room for maintenance and
repair tasks, especially for the replacement of
pumping elements. Disassembly dimensions
for the stator and rotor are provided in the
dimension sheet for the pump and pump unit.
Also make sure that all pipes can be installed
and removed without hindrance.
6.6 Laying the pipes
6.6.1 Nominal widths
The nominal widths of the suction and
pressure lines should match the nominal
widths of the pump branches. Any major
deviations, particularly on the suction side,
must be discussed with the factory.
Stopping devices must be present in the
suction and pressure lines.
6.6.2 Supports and flange
connections
Connect the pipes without tension to the pump
via the flange connections. The pipes require
support close to the pump and should screw in
easily to avoid twisting. After loosening of the
screws, the flanges may not be tilted, nor
spring, nor be under mutual pressure. Any
heat stress at the pipes must be kept away
from the pump with suitable measures, such as
installation of compensators.
6.6.3 Cleaning the pipes before
installation
It is essential to flush and clean the suction-
side pipes, gate valves, and valves before
installing the pump.
Use the cleaning, disinfectant, and flushing
agents recommended by the operator together
with the related process.
Notice!
Residual items from assembly,
such as screws, nuts, weld beads,
or pieces of metal will destroy the
pump's internal parts.
Warranty claims of any kind are invalidated
whenever damages are caused by such
residual items. Flange gaskets may not
protrude inward. Blank flanges, plugs,
protective film, and/or protective coatings on
flanges and sealing strips must be completely
removed.
6.6.4 Laying auxiliary piping for
additional equipment
All auxiliary piping needed to supply the shaft
seal and the jacketed casing (if present) for
heating and cooling the pump must be
attached without tension or leaks.
The lines for the quench liquid on a single-
acting mechanical seal with quench (versions
G0Q and G1Q) and for the buffering liquid on a
double-acting mechanical seal (version
G0D/G1D) should be laid with a large flow
cross-section when possible. The quench or
buffering liquid shall exit at the highest
connection on the mechanical seal casing.
The directions of flow for the flushing,
buffering, and quench liquids are indicated with
arrows in the sectional drawings.
To provide for auto-venting, lay the lines at a
constant gradient, keep them short, and
provide for positive flow characteristics.
Formation of air pockets and gas bubbles must
be avoided. If necessary to achieve this,
provide ventilation connections. Attach the
heating/cooling liquid outlet to the highest
connection on the jacketed casing (if present).