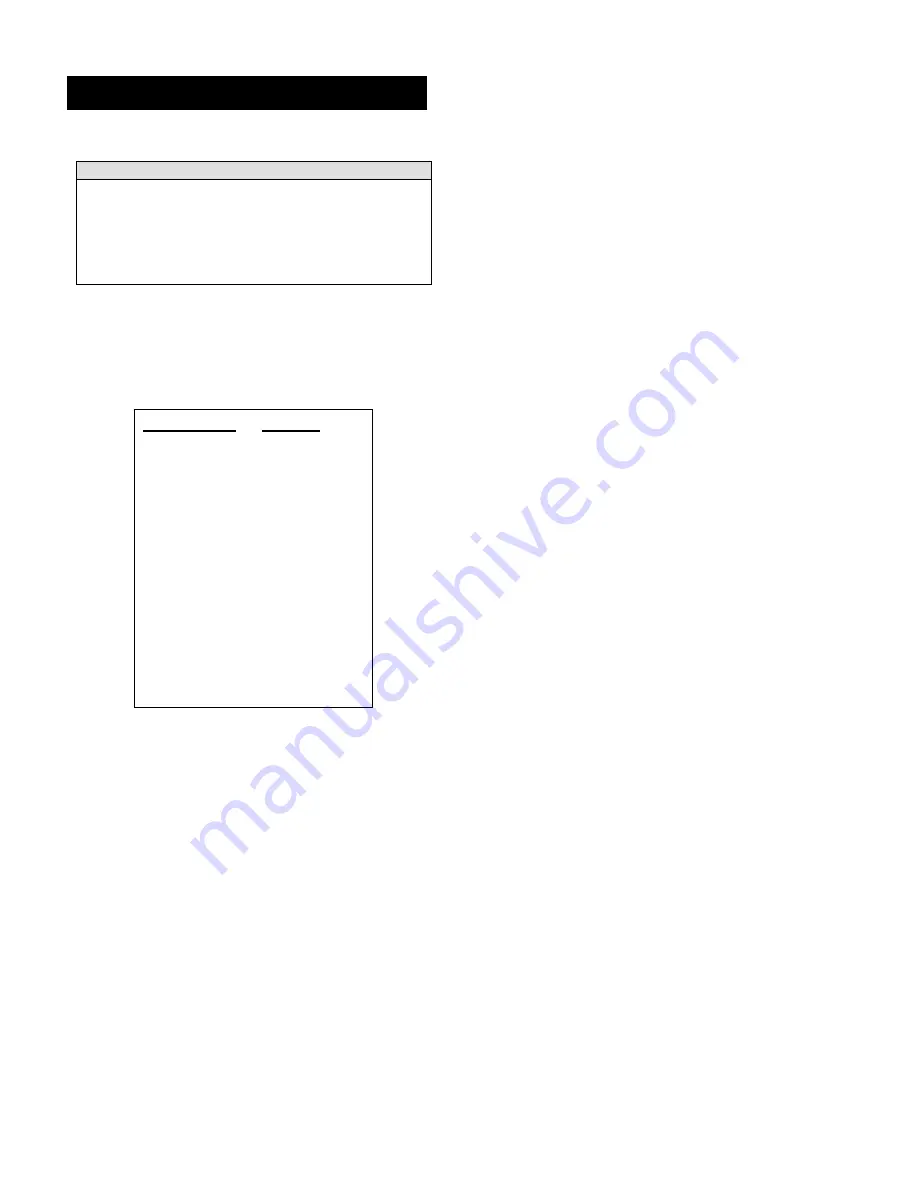
Allied Construction Products, LLC www.alliedcp.com
TM577696_HP400B_16aug
8
6.0 Mounting Information – [cont'd]
6.1.3 XSF Mounting Kits
IMPORTANT
Complete information about the carrier is required,
including the make, model, series and serial
number. Carriers equipped with a quick coupler
will require additional information. (NOTE: The
XSF frame has limited fit-up with carriers equipped
with quick mounting couplers).
Match he carrier’s pin diameter with the proper
mounting kit listed in Table 6.2. Eliminate any gap
using the supplied spacers having varying
thicknesses.
Table 6.2 XSF Mounting Kits
Bucket Pin
Part No.
25 mm
A101735
30 mm
100207
35 mm
100283
38 mm
100364
40 mm
100204
45 mm
100324
50 mm
101808
1.00”
100208
1.25”
100209
1.50”
A100210