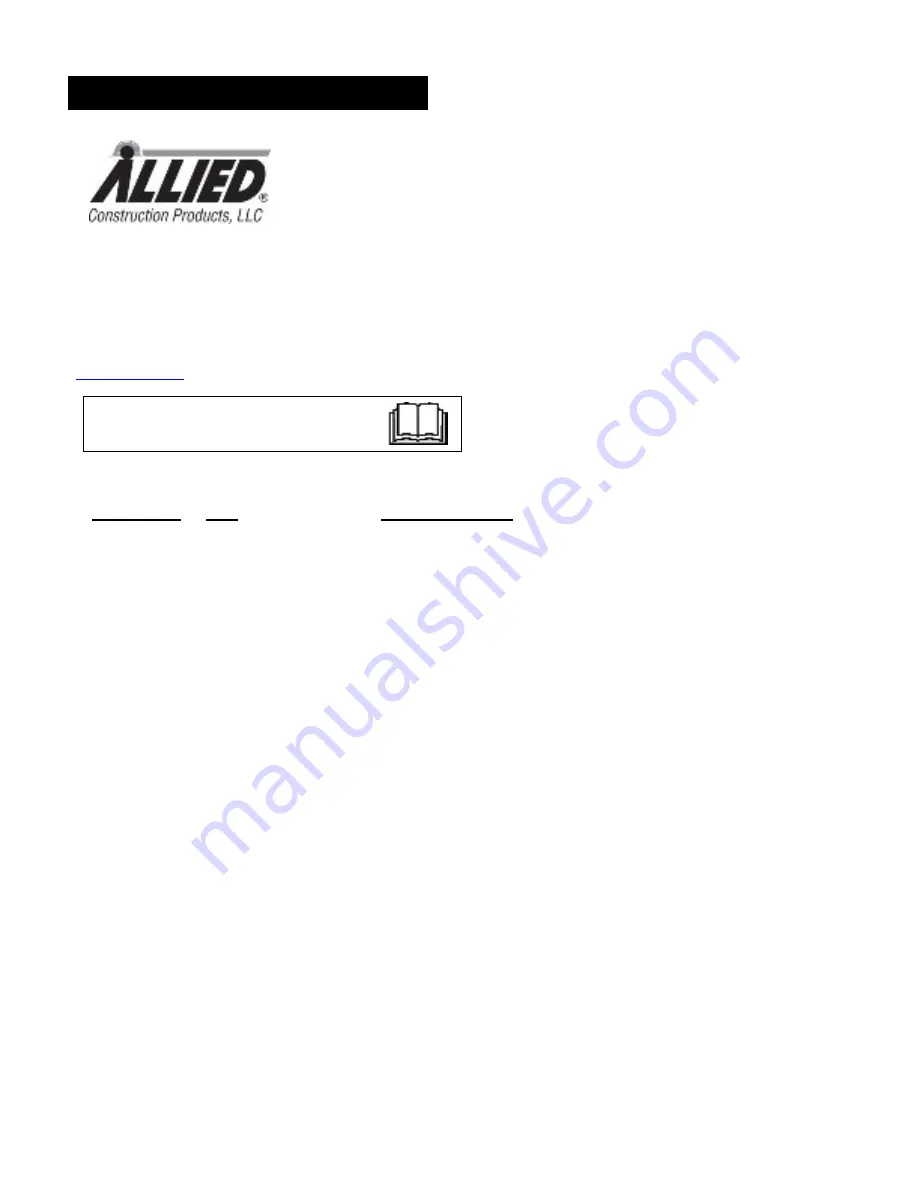
Allied Construction Products, LLC. www.alliedcp.com
i
TM103337_HP1600_18feb
Contact Information and Revision History
3900 Kelley Ave
Cleveland, Ohio 44114
E-mail: [email protected]
Tel: 216-431-2600
Fax: 216-431-2601
Continuous improvement of our products is an Allied policy. Allied reserves the right to change, edit, delete or modify the content
of this document, including descriptions, illustrations and specifications without prior notification. The content of this publication
describe the product at the time of its effective date, and may not reflect the product in the future. Specifications are based on
published information at the time of publication. When changes become necessary, these will be noted in the table below.
Earlier dated publications are immediately cancelled and superseded by publications with the most current date recorded.
Material not in conflict with the most recent effective date shall remain in effect. For product or document updates go to
www.alliedcp.com
Revision History for Document No. TM103337
Table of Revision History TM103337
Effective Date
Page
Summary of Change
18_feb
v
Revise Label Set
15_dec
Throughout
Minor revisions to text, tables and figures. Revise SR/MR bolt set.
13_may
21
Revise Bearing Lubrication Table 10.1.
10_oct
Throughout
Revise Safety Information
09_mar
31, 32, 33, 34
103335 add Begin SN-1600 to parts table & fig.
08_jul
7,8,9,12,32,34,36,38
Revise parts diagram
08_may
34
103335 revise parts diagram
08_apr
32-35
571576 revise bolt part number
07_mar
34, 35
103335 add parts table & fig. to include 572576 eccentric housing w/ weld-
on tamper plate. Use becomes standard configuration.
07_jan
32, 33
103335 End SN-1599 terminate 103342 & 103333. Create parts table &
fig. to include new bearing housing 571576. Begin SN-1600.
06_jun
6,27,31,33,35
Add new motor options. 719717 replaced by 572076.
04_oct
33,35
New hose 570748
04_jul
All
Original Issue of TM103337